Metal processing
Innovative Anlagen für die Metallbearbeitung
Construction Technology
Bautechnologie für Profis
Arbeiten bei LISSMAC
Innovation und Vielfalt unter einem Dach
LISSMAC – uns bewegen Ideen
Wir setzen auf Erfahrung und Systemkompetenz. Vor diesem Hintergrund umfasst die LISSMAC Maschinenbau GmbH vier Geschäftsbereiche: Construction Technology, Metal Processing, Plant Engineering und MT-Handling. Weltweit sorgen mehr als 400 Mitarbeiter an fünf Standorten in Deutschland, Frankreich, den USA und den Vereinigten Arabischen Emiraten für höchste Zufriedenheit bei den Kunden.
Vier Geschäftsbereiche
Imagefilm
News
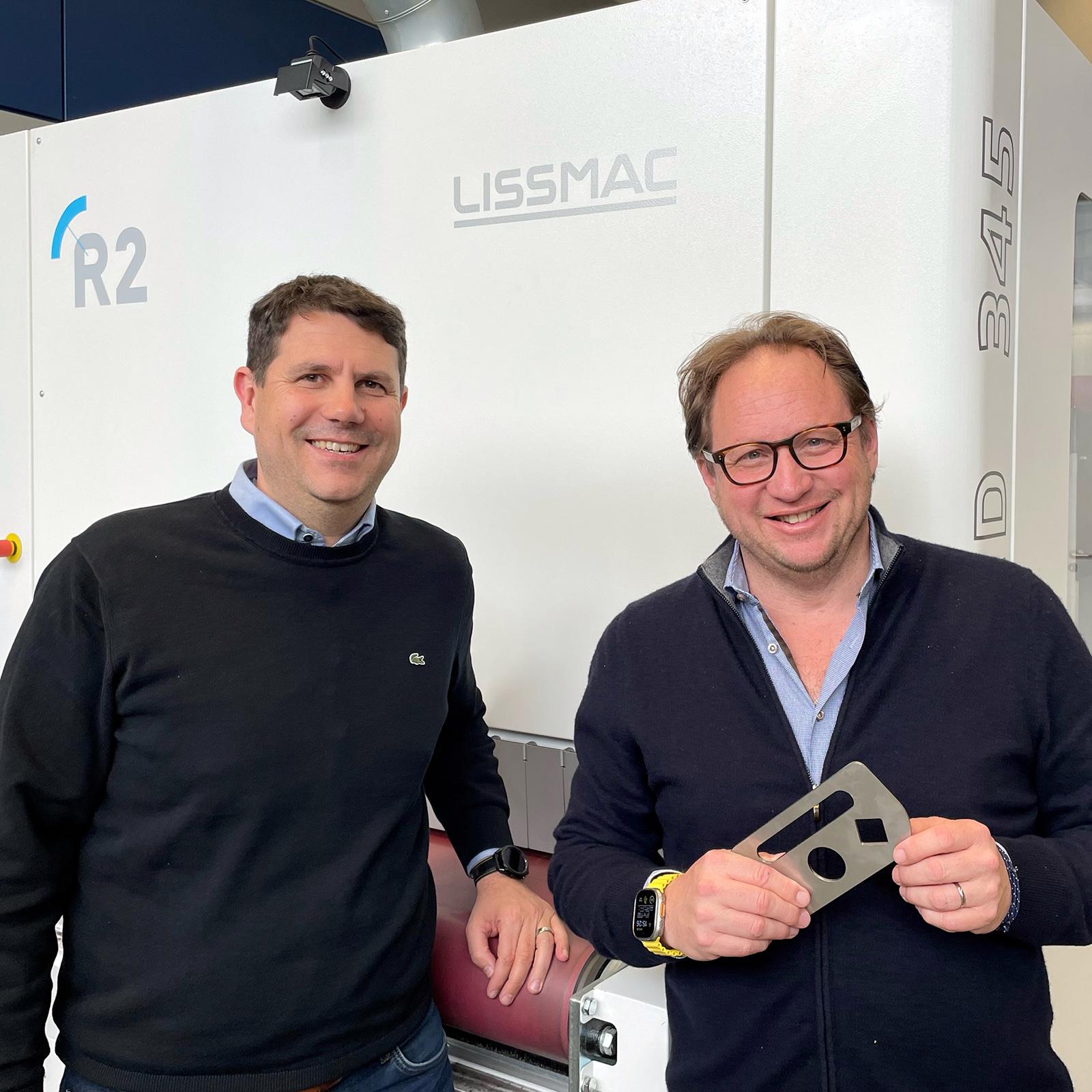
Bevorstehender Führungswechsel bei der LISSMAC Maschinenbau GmbH
Bevorstehender Führungswechsel bei LISSMAC Sehr geehrte Damen und Herren, hiermit möchten wir Sie über eine wichtige Veränderung in der Geschäftsführung der LISSMAC Maschinenbau GmbH informieren. Unser langjähriger Mitarbeiter und Geschäftsführer Daniel Keller wird das Unternehmen zum 13.04.2025 verlassen. Seit dem 01.02.2025 ist sein Nachfolger Herr Thomas Hoffmeister bereits im Amt, er wird künftig gemeinsam mit Dr. Hinrich Dohrmann das Unternehmen führen. Daniel Keller:Im letzten Jahr traf ich nach sorgfältiger Abwägung die Entscheidung, mich nach über zweieinhalb Jahrzehnten bei LISSMAC beruflich neu zu orientieren und eine Position außerhalb des Unternehmens anzutreten. Diese Entscheidung ist mir nicht leichtgefallen, da LISSMAC für mich stets eine Herzensangelegenheit war. Meine Karriere bei LISSMAC habe ich 1998 begonnen, sie führte mich durch verschiedene Positionen und Abteilungen, zu Beginn des Jahres 2022 wurde ich zum Geschäftsführer ernannt. In diesen mehr als zweieinhalb Jahrzehnten durfte ich an der Entwicklung der Firma LISSMAC mitwirken und sie in meinen verschiedenen Aufgabenbereichen mitgestalten. Es war eine sehr intensive Zeit, die mein Leben geprägt hat und die ich nie missen möchte. Gemeinsam haben wir viel erreicht. Diese Erfolge sind das Resultat gemeinsamer Anstrengungen und des unermüdlichen Einsatzes aller Mitarbeiter. Ich möchte mich bei allen Kollegen, Geschäftspartnern und Kunden für die vertrauensvolle Zusammenarbeit und Unterstützung bedanken. Die Erfahrungen und Beziehungen, die ich in meiner Zeit bei LISSMAC aufbauen durfte, werden mich auch in Zukunft begleiten. Mein Name ist Thomas Hoffmeister – ich bin neuer Geschäftsführer bei LISSMAC Maschinenbau GmbH: Mit 53 Jahren bringe ich nicht nur Erfahrung, sondern vor allem Leidenschaft und Unternehmergeist mit. Geboren in Deutschland, aufgewachsen in Italien, der Schweiz und den USA, habe ich früh gelernt, dass Erfolg aus Verantwortung, Beständigkeit und Innovation entsteht – Werte, die mich bis heute antreiben. Meine Wurzeln liegen in einer Unternehmerfamilie, was mir von klein auf gezeigt hat, wie wichtig unternehmerisches Denken, Verantwortung und nachhaltiges Handeln sind. Nach meinem Studium des Wirtschaftsingenieurwesens an der Boston University und einem MBA von der London Business School führte mich meine Karriere rund um den Globus – von Thailand über Ägypten bis China. Stationen bei ABB und der Dresdner Bank haben mir wertvolle Einblicke gegeben, bevor ich 2016 mein eigenes Unternehmen gründete und zwischenzeitlich verkauft habe. Nun freue ich mich darauf, mit voller Energie und einem großartigen Team LISSMAC weiter gemeinsam voranzubringen. Unser Unternehmen ist bestens aufgestellt, um die Herausforderungen der Zukunft nicht nur zu meistern, sondern neue Maßstäbe zu setzen. Mit starken Mitarbeitern, einer soliden Marktposition und großen Investitionen in unseren Standort in Bad Wurzach haben wir alle Voraussetzungen für nachhaltigen Erfolg. Ich freue mich, gemeinsam mit Ihnen die Zukunft zu gestalten!
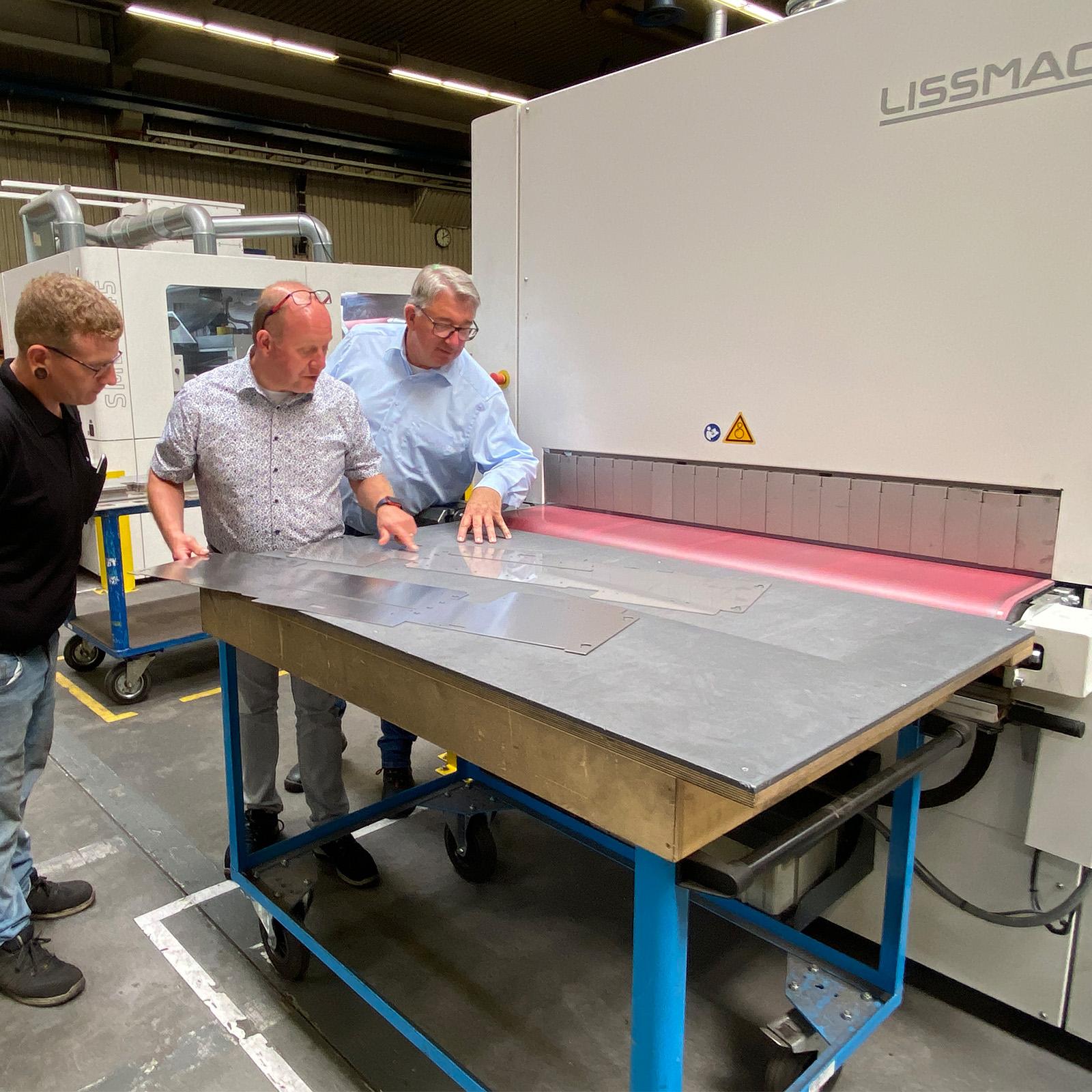
Gratfreie Blechteile für Kassenautomaten und Signaltechnikkomponenten
Gratfreie Blechteile für Kassenautomaten und Signaltechnikkomponenten Gerade der Fiberlaser erfordert aufgrund der beim Schneiden entstehenden Grate eine nachgeschaltete leistungsstarke Entgrattechnik. Ein weltweit agierendes Unternehmen aus Nordrhein-Westfalen investierte mehrfach in diese Techniken und entwickelte dabei parallel eine optimierte Produktionslogistik und einen durchgängigen Material-Flow. Text: Annedore Bose-Munde Welches Produktions-Knowhow in den Dingen steckt, die uns täglich begegnen, ist oft auf den ersten Blick nicht erkennbar, beispielsweise in Park- oder Signallösungen. Das nordrhein-westfälische Familienunternehmen Scheidt & Bachmann gehört zu den führenden Anbietern von Systemlösungen für ein mobiles Leben. So stellt Scheidt & Bachmann unter anderem Kassenautomaten und Terminals für Parkhäuser oder Busse her, Signaltechnikkomponenten und Schrankenanlagen, beispielsweise für die Deutsche Bahn, oder Managementsysteme für Tankstellen und Ladesäulen. Im Jahr 1872 gegründet, entwickelte sich das Unternehmen vom Maschinenbauer zum global agierenden Systemanbieter mit insgesamt etwa 3.500 Mitarbeitern weltweit. Seit jeher zeichnet Scheidt & Bachmann eine hohe Fertigungstiefe aus – nahezu alle Komponenten und Bauteile aus Metall werden inhouse gefertigt. Die Vorfertigung von Scheidt & Bachmann ist in Mönchengladbach angesiedelt, Montagelinien stehen in der Slowakei und in den USA. Scheidt & Bachmann stellt zu 90 Prozent Edelstahlteile her sowie einige Teile aus Aluminium und Stahl. Im Bereich Blechverarbeitung wird in Mönchengladbach mit 90 Mitarbeitern ein breites Portfolio an Blechfertigungsartikeln hergestellt. Die Ansprüche an die Bearbeitungsergebnisse und auch an die Bearbeitungstechnologien sind dabei in den letzten Jahren kontinuierlich gestiegen. Vor 2006 wurden Laserzuschnitte nach dem Zuschnitt auf Paletten abgelegt, gestapelt und dann einzeln entnommen. Im Anschluss wurden diese manuell sowie mit einfacher Technik geschliffen. Dies war recht aufwendig und erforderte einen hohen manuellen Aufwand und mitunter auch mehrfachen Durchlauf. Durchlaufzeiten, Logistik und Kosten waren ebenfalls nicht optimal. Mit den Thema Kantenverrundung wurde dann im Jahr 2006 die erste Lissmac-Anlage angeschafft: eine SBM S 1000 für die Bearbeitung von Blech- und Laserteilen. Das beidseitige Kantenverrunden von Innen- und Außenkonturen in nur einem Arbeitsgang sorgt seitdem für deutlich mehr Prozesseffizienz und für Zeitersparnis. Was zu diesem Zeitpunkt noch fehlte, war eine strukturierte, angepasste Produktionslogistik. Fiberlaser wurde durch leistungsstarke Entgrattechnik ergänzt Als im Jahr 2019 in einem nächsten Schritt modernisiert und in neue Anlagentechnik investiert werden sollte, standen mehrere Kriterien auf dem Plan: Durch die Anschaffung eines Lasers der Firma Trumpf mit Fibertechnologie setzten die Entscheider von Scheidt & Bachmann auf die Technologievorteile des Verfahrens. Die Anschaffung der neuen Schneidtechnik erforderte also unmittelbar auch moderne und leistungsfähige Entgrattechnik. Mit Blick auf die Mitarbeiterschonung sollten zudem ergonomische Verbesserungen für die Werker erreicht werden. Also wurden vor der Anschaffung der neuen Anlage zwei Anlagenhersteller kontaktiert und Referenzteile zur Probenbearbeitung geschickt. Die Entscheidung fiel schlussendlich auf eine SBM-L 1500 von Lissmac, die zum Entgraten und beidseitigen Kantenverrunden eingesetzt wird. „Mit einem Schleifdurchgang erfolgt mit dieser Anlage eine beidseitige Bearbeitung. Und diese ist auch so gut, dass tatsächlich ein Durchgang genügt, um ein qualitativ hochwertiges Schleifergebnis zu erreichen“, sagt Jörg Würker, Leiter Mechanische Fertigung und Leiter Blechverarbeitung bei der Scheidt & Bachmann GmbH. Aufwendige Nachbearbeitungen sind nicht mehr nötig. Und er nennt einen weiteren wichtigen Aspekt: die Arbeitssicherheit für Monteure, die ja dann in den USA greift. „Wenn ein scharfkantiger Artikel in einer Montagelinie ist, kann sich der Monteur verletzen – und dadurch schnell ein rechtliches Problem auftreten“, so Würker. Dass mit allen Testteilen auch die technischen Parameter übergeben wurden, sei zudem gerade in der Startphase mit der neuen Anlage sehr hilfreich gewesen. „Davon haben wir durchaus profitiert“, so Würker. Auch Dirk Schürstedt, Gebietsverkaufsleiter Metal Processing bei der Lissmac Maschinenbau GmbH, der Scheidt & Bachmann seit 2019 betreut, erinnert sich an den Erstkontakt und an einen pragmatischen und konstruktiven Entscheidungsprozess. Er ergänzt: „Alle Bearbeitungen der Proben werden bei Lissmac grundsätzlich exakt und umfassend dokumentiert und dem Kunden zur Verfügung gestellt. Also welche Maschine wurde für die Bearbeitung verwendet, welches Werkzeug, welche Geschwindigkeiten, welche Drehzahlen und so weiter.“ Der Kunde könne damit von Beginn an gute Bearbeitungsergebnisse erzielen. Im Laufe der Zeit und basierend auf den Erfahrungen der Produktion erfolge dann in der Regel noch ein Feintuning der Anlage, welches immer besser auf die Prozesse abgestimmt werden kann. Für die Werker war das Handling mit der neuen Anlagentechnik erst einmal neu, sodass eine zielgerichtete Bedienerschulung in die Anwenderoberfläche durchgeführt wurde. Insgesamt – da sind sich Jörg Würker und Dirk Schürstedt einig – konnte das Projekt zügig und konstruktiv umgesetzt werden. Heute werden auf der Anlage Bleche mit Dicken von 0,8 bis 10 mm bearbeitet. Die Größe der jeweiligen Blechzuschnitte reicht dabei von der Handy- bis zur Tischgröße. Die Anlage wurde im Jahr 2023 zudem mit einer Nassabsaugung nachgerüstet, um auch Aluminium bearbeiten zu können und eine Materialtrennung zu gewährleisten. Schaffung einer optimierten Produktionslogistik Mit der Anschaffung der SBM L 1500 im Jahr 2019 wurde bereits deutlich, dass die Produktionslogistik optimiert werden muss. Als im Jahr 2021 dann zwei vollautomatisierte Trumpf-Fiberlaser-Schneidmaschinen mit angeschlossenem Stopa-Lager angeschafft wurden, stand das Thema wieder im Raum und sollte nun zu Ende gedacht werden. „Wenn der Mitarbeiter das Teil aus der Laseranlage herausnimmt, sollte er es auch direkt auf der Schleifmaschine ablegen. Der durchgängige Material-Flow war uns wichtig und sollte umgesetzt werden“, sagt Würker. Auch um manuelle Arbeiten und hohe Durchlaufzeiten zu vermeiden. Dementsprechend wurden im Jahr 2022 zwei weitere Anlagen angeschafft, mit denen dieser nahtlose Prozess realisiert werden konnte. „Wir setzen auf stabile und funktionierende Beziehungen. Deshalb haben wir uns wieder für Lissmac-Technologie entschieden – diesmal für zwei Anlagen mit Rotationsbürstentechnologie, mit denen wir Entgraten und zudem Kantenverrunden können in einer einstellbaren Qualität und Tiefe“, so der Leiter Blechverarbeitung. „Gekauft wurden zwei universelle Schleif- und Entgratmaschinen SMD 345 S-Edition. Beide Anlagen arbeiten diesmal im einseitigen Betrieb. Mit ihnen kann man jedoch ein definiertes Oberflächenfinish wie den klassischen Bürstschliff erzeugen. Dadurch ist eine höhere Flexibilität möglich und es können Kosten im Einkauf gespart werden“, ergänzt Lissmac-Spezialist Schürstedt. Mit Blick auf das Thema Flexibilität wurden auch diese beiden Anlagen mit einer Nassabsaugung ausgerüstet. Technologiesupport ist wichtig Fest steht: Bei Scheidt & Bachmann ist man mit den Bearbeitungsergebnissen der Lissmac-Anlagen sehr zufrieden. „Seit die neuen Anlagen im Einsatz sind, erzielen wir verlässlich sehr gute Entgratergebnisse“, so Jörg Würker. Dazu kommen ein zielgerichteter Technologiesupport und ein verlässlicher Service. Für Dirk Schürstedt ist es wichtig, mit passgenauer Technik auf die individuellen Produktionsgegebenheiten und Anforderungen des Kunden reagieren zu können. „Es macht Spaß, die Bedürfnisse des Kunden über Jahre begleiten zu können. Auch wir als Maschinenbauer entwickeln die Anlagen stetig weiter. Dafür ist die Rückmeldung des Kunden wichtig“, sagt er. Momentan liegt ein großer Fokus auf der Bedienbarkeit der Anlagen. Diese sollen möglichst einfach und selbsterklärend zu handhaben sein, um dem Werker die Arbeit zu erleichtern.
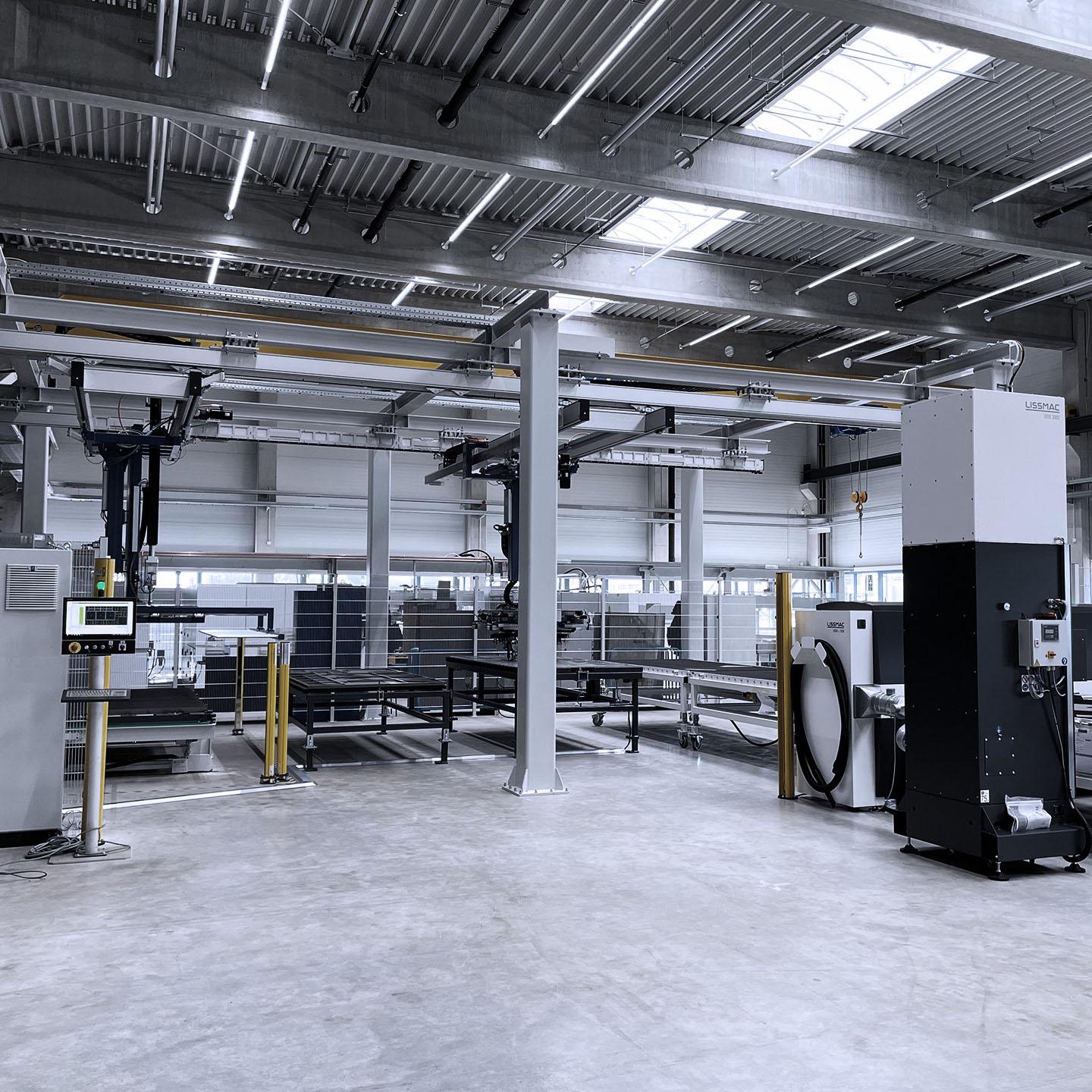
Lissmac automatisiert mit Partnern die Schleif-und Entgrattechnik
Automatisierte Prozesse sorgen für Effizienz in der Blechbearbeitung. So beispielsweise die automatisierte Ausschlagvorrichtung, die die Lissmac Maschinenbau GmbH auf der Euroblech vorstellt. Sie dient dem Trennen von Laserkomponenten, die an Mikrostegen auf der Blechtafel befestigt sind. Vier separat ansteuerbare und mit einem Vakuumsauger ausgestattete Greifereinheiten entfernen gezielt die Laserbauteile aus dem Restegitter, nachdem die Mikrostege durch den Ausstoßvorgang abgetrennt wurden. Danach werden die Bauteile auf einem Förderband für die nächsten Prozessschritte – das Entgraten und Kantenverrunden – abgelegt. Das System erfordert keine optische Bildverarbeitung, da es auf den Geometriedaten des Schnittplans basiert und automatisch die benötigte Anzahl an Sauggreifern ermittelt. Es kann flexibel für verschiedene Blechgrößen und -stärken angepasst werden. Die möglichen Bauteilgrößen reichen in der aktuellen Anlagenausführung von DIN A5 bis zum Europaletten-Format. Bearbeitet werden können Bleche mit Dicken von 1 mm bis 8 mm und mit einem maximalen Gewicht von 90 kg. Ein zeitaufwendiges Abräumen von Hand ist nicht mehr nötig. Durch einen Pufferplatz im Lager wird der Prozess vom Laserschneiden entkoppelt. Die Ausschlagvorrichtung kann für bestehende Schneidanlagen oder für Hochregale nachgerüstet werden und ist herstellerunabhängig einsetzbar. Mit der Automationszelle, die der Bad Wurzacher Maschinenbauer zusammen mit der J. Schmalz GmbH entwickelt hat, wird die Beladung von Lissmac-Schleifmaschinen automatisiert. Die Zelle setzt auf Robotik-Technologie sowie KI-Software und 3D-Vision-Sensoren des Automatisierungstechnik-Herstellers. So werden die Bauteile mit Hilfe einer visuellen 3D-Bauteileerkennung von Schmalz identifiziert, um so sortenreine Bauteile von einer Palette aufzunehmen. Anschließend werden sie mit einem Matrix-Greifer auf ein Förderband gelegt. Im nächsten Prozessschritt kann dann entgratet werden.Durch die Kombination von Beladerobotern mit den Vakuumgreifern von Schmalz und durch die Anbindung an die Schleifanlage wird mehr Effizienz der Produktionsabläufe gewährleistet: Manuelles Beladen wird reduziert, damit eine Entgratmaschine von einer einzelnen Person bedient werden kann. Erstmals wird auf der Euroblech auch die SBM-L-Evo-Baureihe als Vorserienmodell präsentiert. Gezeigt wird die SBM-L 1000 G1S2 Evo − eine Entgratmaschine für beidseitiges Entgraten und Kantenverrunden von gestanzten sowie laser- und feinplasmageschnittenen Blechen in einem Arbeitsgang. Das neue Spitzenmodell der beidseitig arbeitenden Entgratmaschinen von Lissmac ist seit April 2024 als Serienmaschine verfügbar. Aus dem Lissmac-Produktsortiment von einseitig und beidseitig bearbeitenden Schleif- und Entgratmaschinen für die Dünn- und Dickblechbearbeitung werden in Hannover zudem die SBM-L 1500 G1S2 für hocheffizientes beidseitiges Entgraten und Kantenverrunden von Stanz-, Laser- oder HD-Plasmaschneidteilen gezeigt und die SMD 35 REER (S-Edition) für eine gleichmäßige Kantenverrundung an allen Kanten bis zu einem Radius von 2 mm sowie für ein richtungsloses Finish und die Kleinteile- und Dünnblechbearbeitung. Außerdem wird die SMD 123 RE präsentiert, die für das Entgraten und ein gleichmäßiges Kantenverrunden an allen Kanten sowie die Oberflächenbearbeitung von Werkstücken aus Stahl, Edelstahl und Aluminium eingesetzt werden kann. Und gezeigt wird auch die SBM- XS 300 G1E1 Alu Mix für die Entgratung und gleichmäßige Kantenverrundung von Kleinteilen in einem Arbeitsgang. Messebesucher sind herzlich eingeladen, sich am Lissmac-Stand, Halle 14, Stand 14-K06, über bewährte Technologien und die neuen Features für Industrie 4.0 zu informieren.
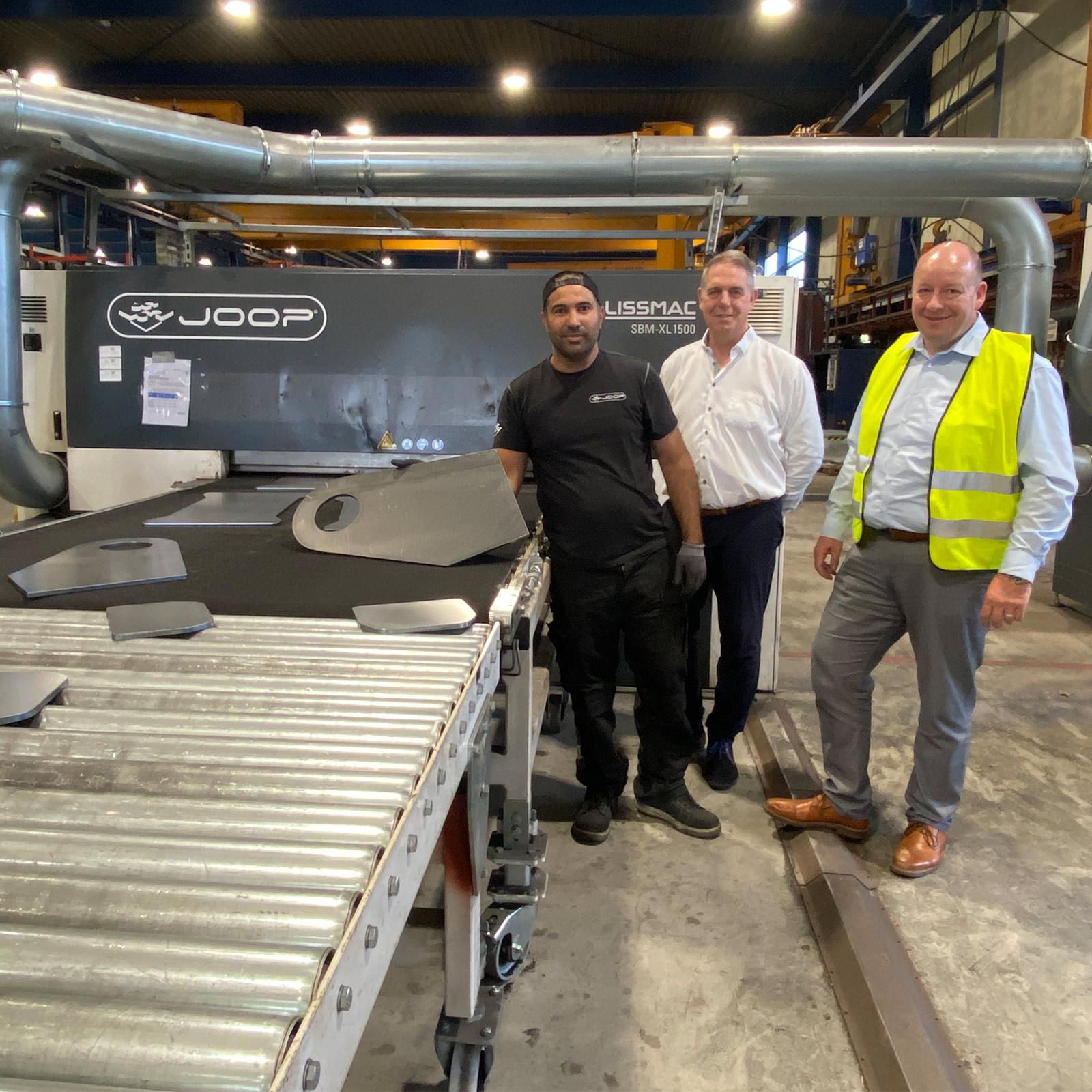
Fokus liegt vollumfänglich auf der Automatisierung
Es braucht immer Visionäre und Vorreiter, um etwas Neues auf dem Markt zu etablieren. Ein niederländisches Stahlservicecenter ist so ein Vorreiter. Hier soll die Dickblechbearbeitung automatisiert werden. Ein wichtiger Lösungsbaustein dafür sind zwei neue Bearbeitungsstrecken von Lissmac die angeschafft wurden. Text: Annedore Bose-Munde Seit 1966 ist das Familienunternehmen Joop van Zanten als Komplettanbieter für das Plasma- und Autogenschneiden von Stahl auf dem Markt. Das Stahlservicecenter im niederländischen Veenendaal hat heute über 40 Mitarbeiter und bearbeitet Stahlbleche im Bereich von 2 mm bis 300 mm. Dazu kommt Bohren und Gewindeschneiden, Abkanten, Richten, Strahlen und Schweißen. Bart Kroesbergen ist seit 2018 Betriebsleiter bei Joop van Zanten. Er blickt zurück: „Vor sechs Jahren gab es bei Joop van Zanten noch viel Handarbeit. Doch gerade mit Blick auf die Wettbewerbsfähigkeit, den Fachkräftemangel und die Zukunftsausrichtung sollte sich etwas ändern.“ Zwei Fragen standen dabei von Beginn an im Raum: „Können wir automatisieren, um die Arbeit attraktiver und effizienter zu machen? Und vor allem: Können wir Kosten sparen?“ Bereits 2018 war das Produktspektrum des Stahlbearbeiters sehr breit. Deshalb war ein weiterer Punkt sehr wichtig: die Flexibilität. „Die Firma soll für die nächsten 20 Jahre aufgestellt werden. Zunehmend erfolgt eine Komponentenfertigung für Endproduzenten. Dazu wurden viele Technologien in Haus geholt, wie Schweißen, maschinelle Bearbeitungen und Kanten. Wir versuchen die Prozesse so umzusetzen, dass sie möglichst weit automatisiert sind. Damit soll die Vorhersagbarkeit bei neuen Produkten und die Reproduzierbarkeit der Produkte sichergestellt werden, ebenso eine konstante Qualität und natürlich auch die Wettbewerbsfähigkeit in Europa“, definiert Managing Director Kroesbergen den Weg und das Ziel. Seit 2018 hat das Familienunternehmen gemeinsam mit einem externen Direktor, eine neue Strategie für das Unternehmen umgesetzt. Gleichzeitig wird zudem die nächste Familiengeneration auf eine Managementposition vorbereitet. Zusammen mit Bart Kroesbergen, der einen umfassenden betriebswirtschaftlichen Hintergrund hat, konnten so Erfahrung, Wissen und der gemeinsame Veränderungswille bereits viel bewegen. Schon heute zählt Joop van Zanten zu den modernsten Stahlbearbeitungsunternehmen in den Niederlanden, zeichnet sich durch seinen hohen Automatisierung- und Digitalisierungsgrad aus und treibt das Thema Industrie 4.0 konsequent voran. Investition in zwei effiziente, baugleiche Anlagen Der Kundenkreis von Joop van Zanten hat sich in den letzten Jahren geändert. Anfangs agierte das Unternehmen überwiegend als Massen-Stahl-Schneidebetrieb. Es ging um Kilogramm und schweren Stahl. Die Kunden kamen beispielsweise aus dem Brücken- oder Schiffbau. Doch das Unternehmen wollte und sollte flexibler werden und das Leistungsspektrum erweitern - auch mit Blick auf die Materialdicken. Jetzt liegt das Spektrum der verarbeiteten Materialdicken im Bereich von 2 mm bis 300 mm. Derzeit ist das kleinste Produkt einige Zentimeter groß, das größte fast 14 Meter. Insgesamt 90.000 verschiedene Teile wurden im Jahr 2023 gefertigt. Die Kunden kommen heute meist aus der Industrie, dem Maschinenbau und dem Transportbereich. Der Fokus der Fertigung liegt darauf, die Kunden mit einem kompletten Endprodukt zu beliefern, welches effizient gefertigt wurde. Die Prozesse sollen dabei so weit automatisiert werden, dass eine hohe Wirtschaftlichkeit abgebildet wird. Um diese Ziele zu erreichen, investierte das niederländische Unternehmen in zwei baugleiche Lissmac-Anlagen, jeweils bestehend einer Schlackeentfernungsmaschine SBM-M 1500 D2, einer Schleif- und Entgratmaschine SBM-XL 1500 G2S2 (Durchlassbreite beider Anlagen ist 1.500 mm) sowie Absaug- und Fördertechnik. Die erste Anlage wurde im Jahr 2019 gekauft, die zweite 2021. „Wir haben mehrere Produzenten besucht, mit Anlagenvertretern gesprochen und uns auch auf den gängigen Messen umgeschaut“, blickt Betriebsleiter Kroesbergen zurück. Doch ein Punkt überzeugte die Entscheider bei Joop van Zanten schlussendlich: die beidseitige Bearbeitung, welche die Lissmac-Anlagen ermöglichen. „Wir lassen mitunter Produkte durch die Anlagen laufen, die 20 Meter lang sind. Das ist mit der Lissmac-Technik in nur einem Prozessschritt möglich und bedeutet daher eine enorme Arbeitserleichterung“, so Kroesbergen. Das ansonsten erforderliche Handling und eine damit verbundene aufwendige Logistik in den Hallen entfällt. Bevor die Entscheidung für die Anlagenstrecke der Lissmac Maschinenbau GmbH gefallen ist, sind umfangreiche Tests gelaufen. Dies war auch aufgrund der hohen Teilevielfalt nötig. Die Praxistests erfolgten mit Blick auf die Produkte und Materialien. Es wurden Feineinstellungen vorgenommen und 2019 ist die Anlage dann in Betrieb gegangen. „Wir haben uns entschieden, dass alle bei uns gefertigten Teile durch die Lissmac-Anlage laufen. Natürlich sind die Oberflächenqualität und die Haptik nun besser. Aber es sieht auch jedes einzelne Teil einfach richtig gut aus“, sagt Bart Kroesbergen. Allein aufgrund der technischen Anforderungen wäre dies nur bei etwa 50 Prozent aller Teile nötig. Aber zwischenzeitlich sind die entgrateten und verrundeten Teile auch ein Qualitätsmerkmal für Joop van Zanten geworden, welches die Kunden zu schätzen wissen. Und dann ist da noch der immer vorausschauende Blick des Betriebsleiters auf vollautomatisierte Prozessabläufe. „Wenn man einen zweiten Bearbeitungsstrom in einem Prozess hat, der nicht automatisiert werden soll, ist es schwieriger, ganzheitlich zu automatisieren“, sagt er. Die zweite Anlage, die in einem anderen Produktionsbereich steht, wurde im Jahr 2021 gekauft. Die Produktionsmenge war deutlich gestiegen und bestimmte Produktionsspektren sollten logistisch effizient bearbeitet werden. Doch auch vor dem Hintergrund der Automatisierung, die noch deutlich ausgebaut werden soll, wurde diese baugleiche Anlage angeschafft. Ziel ist Automatisierung im Dickblechbereich Eine der beiden Lissmac-Straßen wird bereits in der automatisierten Produktion eingesetzt werden. Hier werden Stahlbleche bis zu 40 mm Dicke bearbeitet. Mit der zweiten Anlage werden Bleche bis zu 100 mm Materialdicke bearbeitet. Auch hier soll automatisiert werden. „Die Anforderung, dass die Anlagen für eine zukünftige Automation vorbereitet sein sollen, wurde von Joop van Zanten gleich beim Projektstart der ersten Anlage benannt“, blickt Robert Dimmler, Sales Director Metal Processing bei Lissmac, zurück. Dies sei auch vor dem Hintergrund einer reibungslosen Schnittstellenkommunikation zwischen unterschiedlichen Applikationen und Anlagen ein sehr wichtiger Punkt.Eine Anlagenstrecke, bestehend aus einer Schlackeentfernungsmaschine, einer Schleif- und Entgratmaschine sowie Absaug- und Fördertechnik, gehört für den Maschinenbauer zu den Standardapplikationen. „Doch der Blick von Joop van Zanten auf die von Beginn an angedachte Automatisierung war durchaus visionär. Eine Automation im Dickblechbereich war bis zu diesem Zeitpunkt noch unüblich“, sagt Dimmler. „Automation kennt man üblicherweise aus dem Dünnblechbereich. Dies sollte nun in den Dickblechbereich transformiert werden, in dem ganz andere Werkstückabmessungen und Teilegewichte üblich sind. Hier an der Lösungsfindung beteiligt zu sein, ist ein spannender Part und durchaus auch eine Herausforderung.“ „Unser Traum war es, innerhalb von zehn Jahren eine komplett automatisierte Fabrik zur Dickblechbearbeitung zu nutzen. Nicht die Frage ‚Werden wir das umsetzen können?‘ stand im Raum, sondern die Frage ‚Wie werden wir das konkret umsetzen können?‘“; sagt Bart Kroesbergen. Dafür seien auch Erfahrungen aus anderen Branchen mit in die Betrachtungen eingeflossen, beispielsweise aus dem Betonbau, wo es ebenfalls um sehr hohe Stückgewichte geht. Dieses optimistische Um-die-Ecke-Blicken überzeugte auch Maschinenbauer Lissmac. „Ein Anlagenhersteller entwickelt sich auch aufgrund seiner Kundenanforderungen weiter. Und wenn man einen visionären Kunden hat wie Joop van Zanten, dann triggert das auch uns“, ergänzt Robert Dimmler. Bei neuen Umsetzungsideen gehöre es einfach dazu, das eigene Korsett auch einmal abzulegen und über den Tellerrand hinauszuschauen. Herausforderung liegt im Stückteilgewicht und der Teilevielfalt Das Teilegewicht, die Teilevielfalt und die Komplexität der Strukturen erfordern mit Blick auf die Automatisierung neue Umsetzungsansätze. Das mechanische Abräumen der Teile mittels Robotik ist daher momentan noch nicht vollständig umgesetzt. Hier arbeitet Joop van Zanten gemeinsam mit der Messer Cutting Systems GmbH, der Beuting Metalltechnik GmbH & Co. KG und Lissmac an einer entsprechenden Lösung. Das Ziel, an dem die beteiligten Partner arbeiten, ist eine Lösung, die das Kernteilespektrum des Unternehmens im Dickblechbereich abdecken wird. Im nächsten Jahr sollen die Anlagen automatisiert laufen. Dass in dem niederländischen Stahlservicecenter alle Anlagen im Betrieb mit einer Software-Plattform und mit OPC UA-Schnittstellen verbunden sind, ist ein weiterer wichtiger Punkt für eine durchgängige Automatisierung. Auch Maschinenbauer Lissmac hat den OPC UA-Standard (Standard zur sicheren, herstellerübergreifenden Vernetzung für industrielle Anlagen) für die eigenen Produkte als Standard definiert. Ein Beispiel zeigt, wie wichtig die Thematik ist: Ein Kunde von Joop van Zanten fertigt das Frame von einer Anlage, die Chips produziert. Die erforderlichen Stahlplatten, die das Stahlservicecenter hierfür fertigt, dürfen nicht mit den Händen angefasst werden, damit das Fingerfett nicht auf die Anlagen kommt. Ohne Automatisierung wäre das nicht denkbar. Fest steht: Die Projektpartner arbeiten gemeinsam an einer durchaus visionären Aufgabenstellung. Doch um diese zu lösen, geht es um sehr pragmatische Dinge: die technische Umsetzung, den steten Austausch und das stete voneinander Lernen und einander unterstützen.
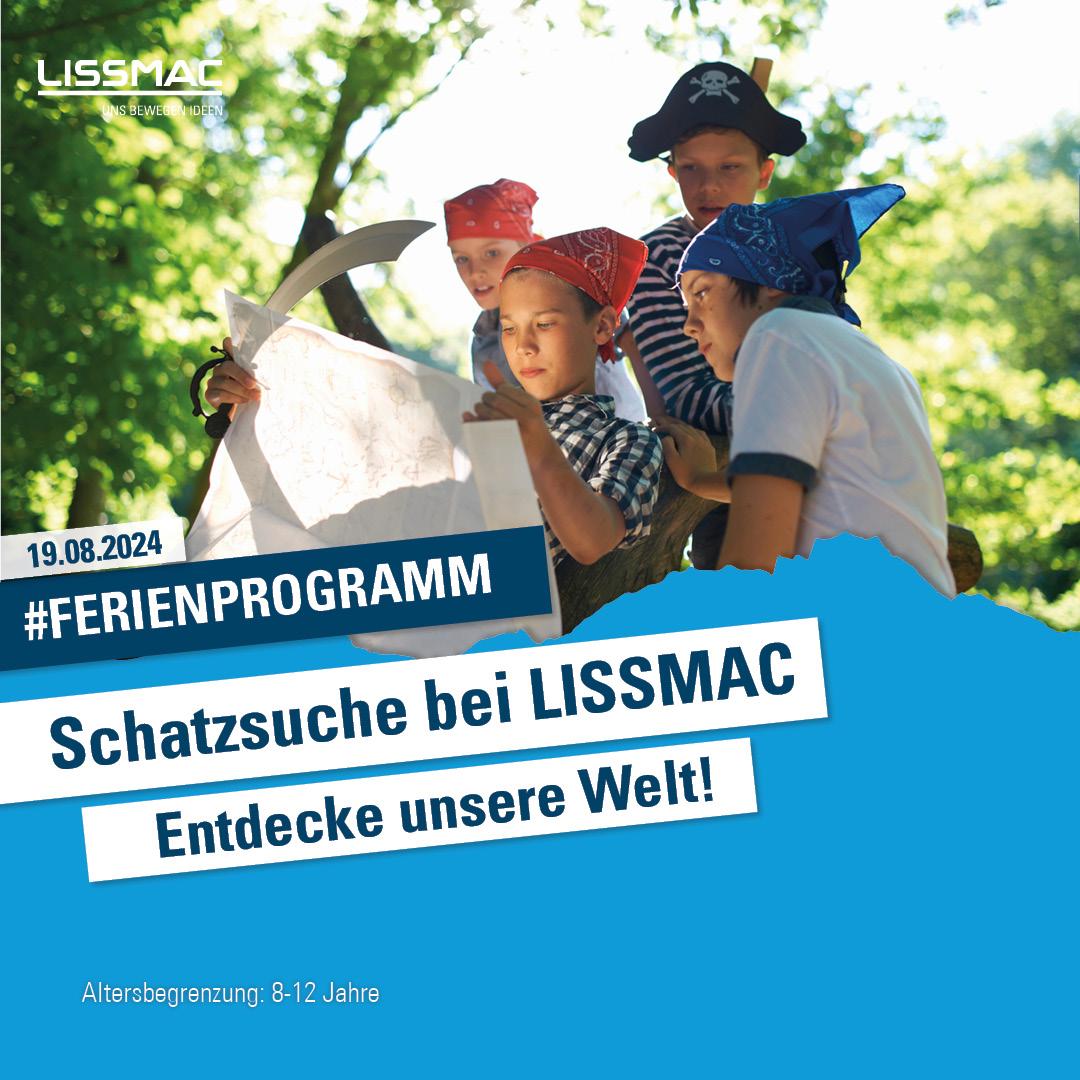
Hast Du Lust Dich auf die Suche nach dem Schatz bei LISSMAC zu machen?
Termin: 19.08.2024 Max. 15 Teilnehmer Altersbegrenzung: 8-12 Jahre Bei der Schatzsuche wirst Du LISSMAC und die Produkte, sowie den Ablauf vom Blech bis zur Maschine kennenlernen. Zudem erwarten Dich spannende Projekte, die unsere Azubis gebaut haben. Eines dieser Projekte war ein Tischkicker. Am Ende unserer Schatzsuche erwarten Dich tolle Geschenke und Informationen zum Schnupperpraktikum, Ausbildungsstellen,…. Für Essen und Trinken ist ausreichend gesorgt! Alle Informationen & die Möglichkeit zur Anmeldung hier Anmeldung möglich per Telefon, E-Mail oder Einwurf der Anmeldekarte bei der Stadt Bad Wurzach. Zum Programmheft (LISSMAC S.29)
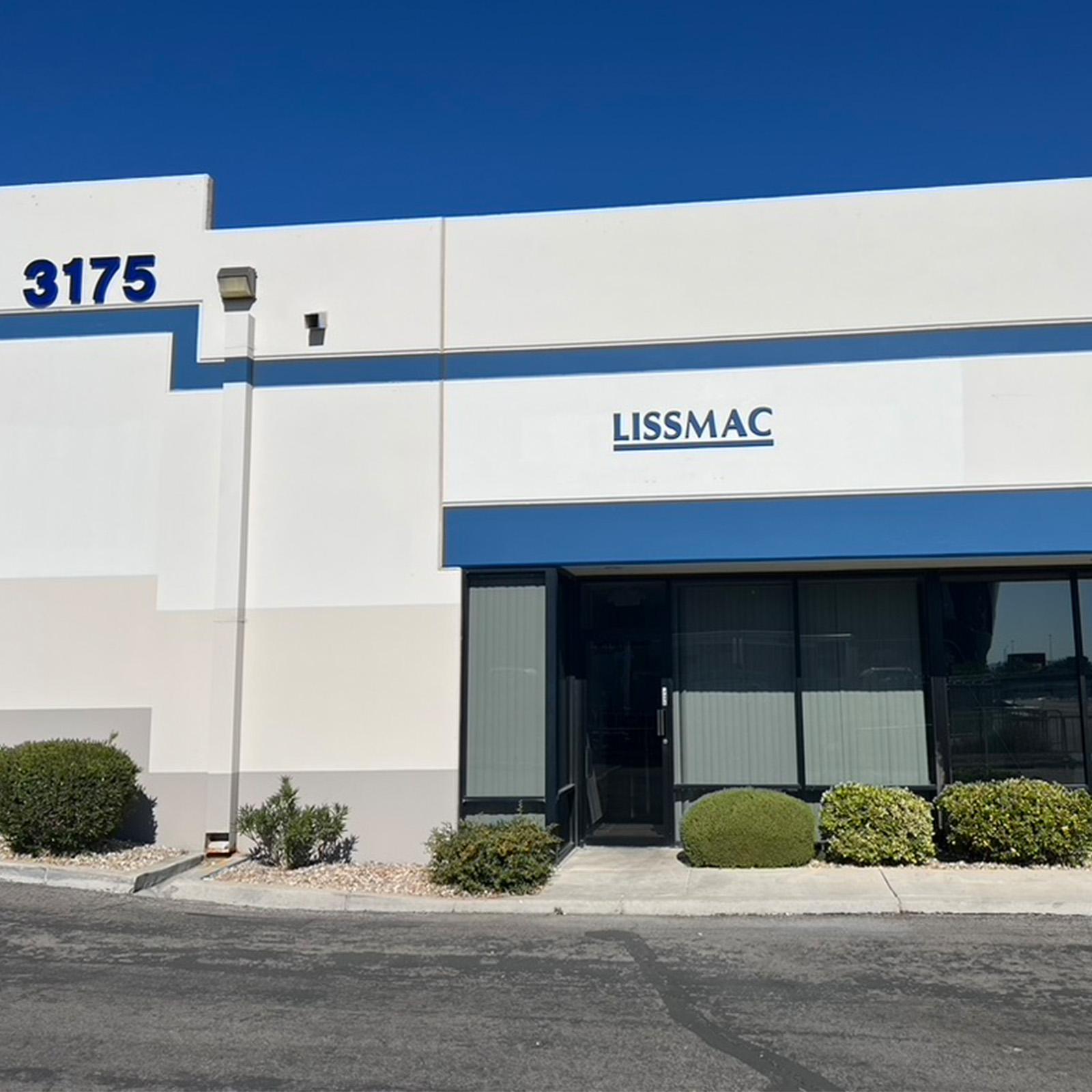
LISSMAC Corporation eröffnet neues Büro in Las Vegas
Zum 1. Januar 2024 eröffnete LISSMAC Corporation einen neuen Standort in Las Vegas, USA. Im ersten Schritt dient das Satellitenbüro in Las Vegas als Vertriebs- und Servicestandort für den Süden und die Westküste der USA. „Das neue Büro in Las Vegas ist für uns ein wichtiger Schritt, um unsere Vertriebs- und Serviceaktivitäten im Westen der USA auszubauen.“ sagt Ingo Heiland, Vice President der LISSMAC Corporation. „Las Vegas ist mit der World of Concrete, einer jährlichen Fachmesse für Beton und Maurerarbeiten, sowie der wiederkehrenden Industriemesse FABTECH ein wichtiger Messestandort für uns. Weiterhin ist Nevada im Südwesten geographisch günstig gelegen, und hat selber einen starken Industrie- und Bausektor.“ LISSMAC Corporation wurde 2007 in Mechanicville, New York gegründet und bedient seither den US-Markt mit innovativen und zuverlässigen Lösungen in den Geschäftsbereichen Construction Technology und Metall Processing. Mit 25 Mitarbeitenden, einem Showroom für Probebearbeitungen, einem Serviceteam und einem eigenen Ersatzteil- und Warenlager ist der Standort in Mechanicville bestens ausgestattet, um Kunden von der Produktberatung bis zum After-Sales zu betreuen. „Wir werden im kommenden Jahr den Standort in Las Vegas ausbauen und weitere Mitarbeitende einstellen, um das gleiche Niveau an Kundenbetreuung zu erreichen, wie in Upstate New York“ erklärt Ingo Heiland. „Das Ziel ist, sowohl bei langjährigen Referenzkunden in der Nähe sowie mittelfristig am eigenen Standort, Produktvorführungen im Geschäftsbereich Metal Processing durchzuführen. Außerdem ermöglichen zahlreiche Bauprojekte die Vorführungen unserer Produkte für den Tiefbau.“ ergänzt Norbert Zell, Standortleiter in Las Vegas. Das neue Büro befindet sich fünf Meilen vom Flughafen entfernt sowie gegenüber des Allegiant Stadiums, Austragungsort des Super Bowls LVIII im Februar, 2024. Seit 1. Januar 2024 bedient LISSMAC Corporation den Südwesten und West Coast der USA vom neuen Standort aus: LISSMAC Corporation Satellite Branch 3175 W Ali Baba Ln Suite 806 Las Vegas, NV 89118 USA
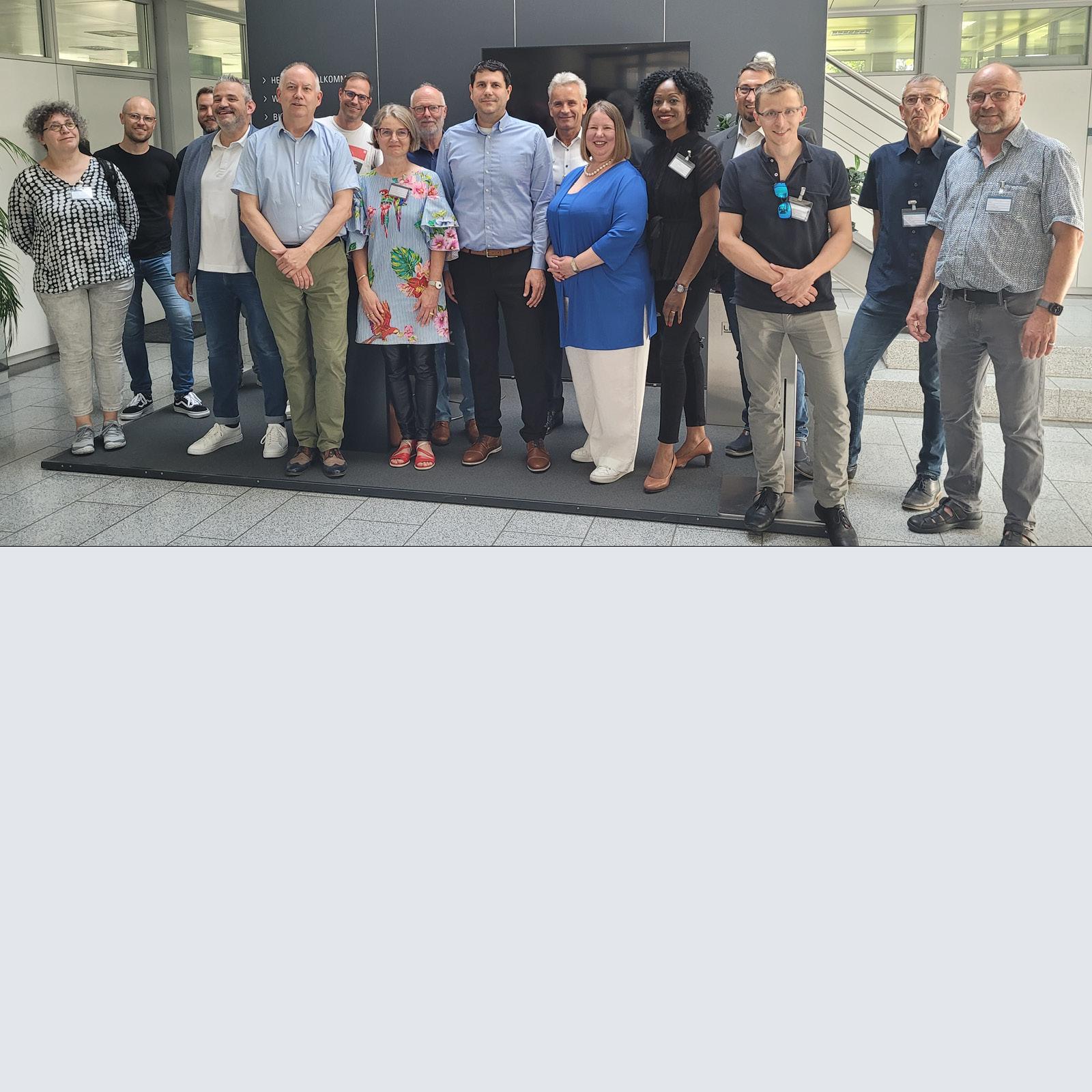
Werksbesichtigung HGV Bad Wurzach
Am 26.06.2024 hatten wir eine Besuchergruppe des Handels- und Gewerbevereins Bad Wurzach e.V. zu Gast. Der HGV ist ein Zusammenschluss von Gewerbetreibenden in Bad Wurzach. Die interessierten Gäste, hauptsächlich Geschäftsführer von Wurzacher Firmen, nützten die Gelegenheit zur Besichtigung unseres Unternehmens. Nach dem Empfang und der Begrüßung durch die Geschäftsführung wurden die Gäste in zwei Gruppen aufgeteilt und von Daniel Keller und Hinrich Dohrmann durch die Produktionshallen geführt. Den Besuchern wurde dabei auch die neue Halle gezeigt und die Digitalisierung und die Automation unserer Arbeitsprozesse erläutert, es wurde aber auch auf das aktuell schwierige wirtschaftliche Umfeld eingegangen, aber immer mit optimistischem Blick nach vorne. Im Anschluss an die einstündige Führung gab es bei einem Imbiss Gelegenheit für Fragen und lockere Gespräche.
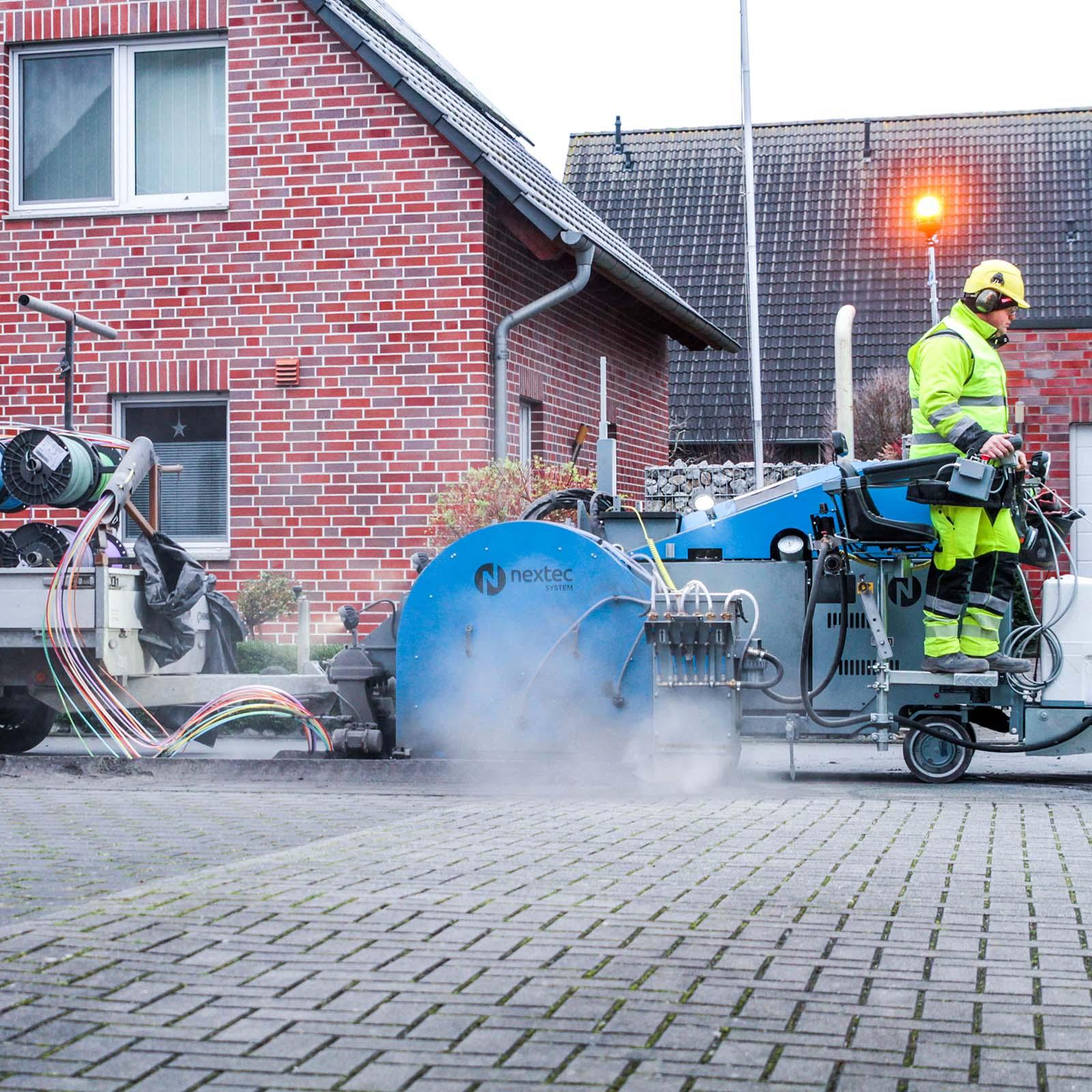
DIN 18220: EIN MEILENSTEIN FÜR DEN GLASFASERAUSBAU
DIN 18220 TRITT IN KRAFTAm 28.07.2023 wurde die „DIN 18220:2023-08. Trenching-, Fräs- und Pflugverfahren zur Legung von Leerrohrinfrastrukturen und Glasfaserkabeln für Telekommunikationsnetze“ verabschiedet. Im Rahmen einer Veranstaltung zur Gigabitstrategie des Bundesministeriums für Digitales und Verkehr (BMDV) wurde das Dokument feierlich übergeben. Durch § 126 Telekommunikationsgesetz (TKG) ist sie als anerkannte Regel der Technik ab Zeitpunkt der Veröffentlichung durch alle Beteiligten einheitlich anzuwenden. Die DIN 18220 soll zu einer kostengünstigen Beschleunigung und vor allem zur qualitativ hochwertigen Umsetzung des Glasfaserausbaus beitragen. Sie legt klare Einsatz- und Ausführungsbedingungen fest und setzt den rechtlichen Rahmen für die Erreichung eines Meilensteins im Breitband- und Glasfaserausbau. Die DIN 18220 erhöht die Investitionssicherheit für alle Beteiligten, insbesondere für Telekommunikationsunternehmen. Für das Trenching-Verfahren gab es bislang weder standardisierte Rahmenbedingungen noch einheitliche Grundsätze für die Anwendung. Bislang haben die meisten Kommunen vorwiegend die offene Bauweise als Legemethode zum Glasfaserausbau gewählt, da die Minderüberdeckung vor der Norm mindestens 60 cm betragen musste. Seit 2012 erlaubt das TKG den Einsatz mindertiefer Legung (Trenching, mindertiefe Legearten), wozu auch noch nicht genormte Verfahren wie das Trenching zählen. Allerdings konnte sich das Verfahren bisher nur schwer am Markt durchsetzen. Grund dafür sind vornehmlich Rechtsunsicherheiten für alle Beteiligten. Diese gehen zwangsläufig mit dem Fehlen von verbindlichen technischen Vorgaben, in Form einer verbindlichen Norm, für den Einsatz solcher alternativen Legemethoden einher. Die Schwierigkeit lag insbesondere in Differenzen zwischen Straßenbauverwaltungen, Bauausführenden und Telekommunikationsunternehmen über die konkrete Ausführung und Umsetzung. Infolgedessen kam es zu Verzögerungen im Ausbau der Glasfaserinfrastruktur. DAS ÄNDERT SICH DURCH DIE NEUE DIN 18220Bislang haben die meisten Kommunen vorwiegend die offene Bauweise als Legemethode zum Glasfaserausbau gewählt, da die Minderüberdeckung vor der Norm mindestens 60 cm betragen musste. Jetzt regelt die DIN 18220 Legearten für Minderbautiefen, was unter anderem auch das Diamanttrenching von LISSMAC betrifft (38 cm Legetiefe).„Mit der DIN 18220 kann der Glasfaserausbau künftig nicht nur einfacher, sondern auch qualitativ hochwertiger, schneller, kostengünstiger und ressourcenschonender erfolgen. Die DIN 18220 schafft die erforderliche Rechtssicherheit und Investitionssicherheit für alle Beteiligten“, beschrieb BMDV Staatssekretär Stefan Schnorr die Bedeutung der neuen Norm. DAS BEDEUTET DIE DIN 18220 FÜR LISSMACSeit rund 10 Jahren ist LISSMAC im Diamanttrenching aktiv. Aufgrund unserer Erfahrung im Bereich Fugenschneiden sind wir langjähriges Mitglied des VDMA (Verband Deutscher Maschinen- und Anlagenbau) und haben bei der Erstellung der Norm als Mitglied im Normungsausschusses mitgewirkt. Wir freuen uns sehr über die Anerkennung der alternativen Legemethoden für den Glasfaserausbau, unter anderem das LISSMAC Diamanttrenching, da die Norm Klarheit für die Bauwirtschaft, alle Kommunen, Gemeinden und Telekommunikationsunternehmen schafft. Hier erhalten Sie weitere Informationen über das Diamanttrenching nach DIN 18220 mit LISSMAC. Hier gelangen Sie zu den Hintergrundinformationen über die DIN 18220. Sehen Sie sich auch das Video zum Pilotprojekt "Glasfaser ohne Einblasen" mit der Telekom an.
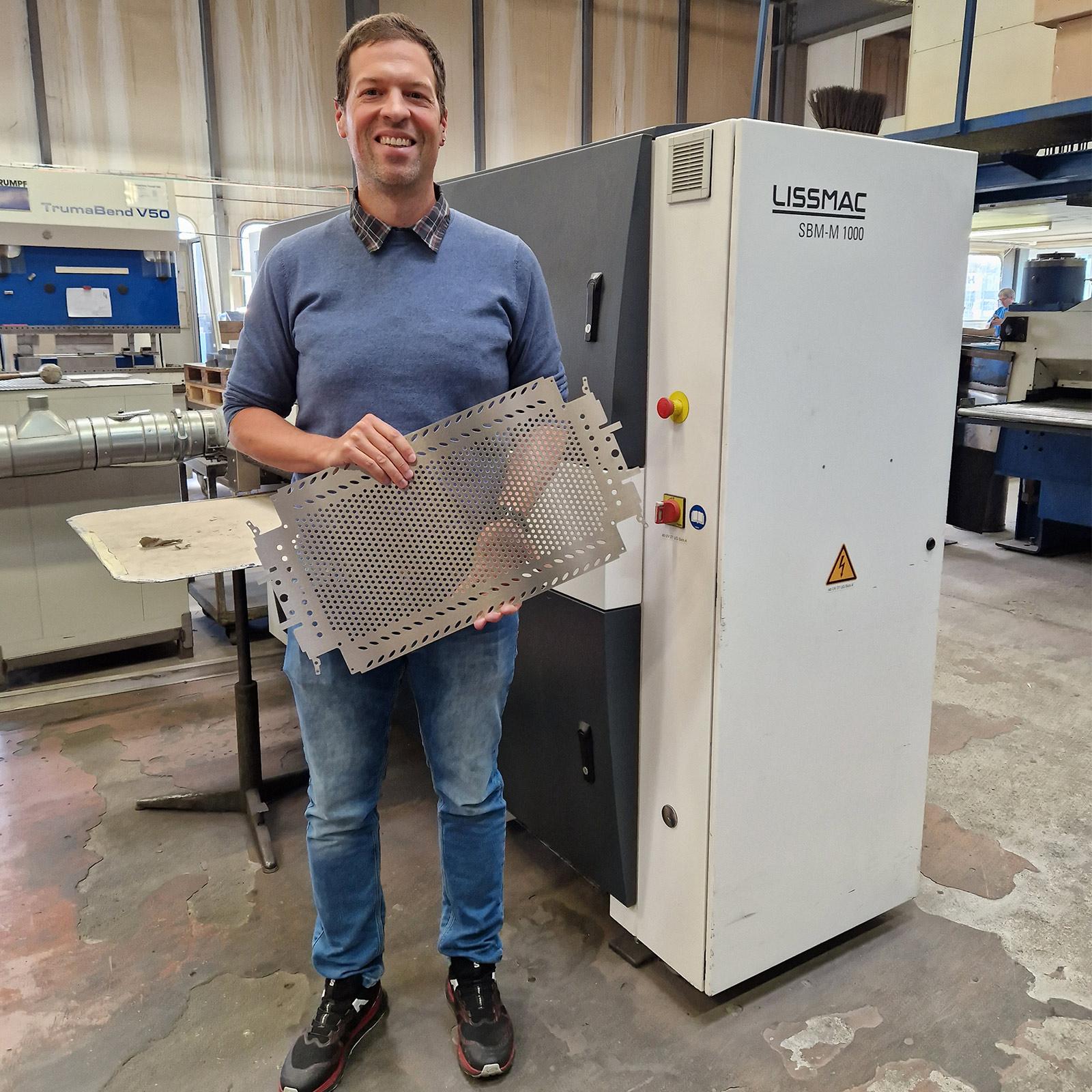
Prozesssicherheit durch zwei neue Schleif- und Entgratanlagen
In gleich zwei Schleif- und Entgratanlagen investierte ein Schweizer Blechbearbeiter. Sie werden für die Entfernung von Sekundärgraten eingesetzt sowie für ein optimales Oberflächenfinish. Im Fokus der Ersatzbeschaffungen standen dabei Flexibilität, Effizienzsteigerung und auch ein verlässlicher Service. Text: Annedore Bose-Munde Seit 54 Jahren ist die Ulrich Oppliger AG aus Lyssach in der Schweiz erfolgreich am Markt. Kernkompetenz des Unternehmens ist die Blechbearbeitung - vom Biegen über das Laserstanzen und -schneiden bis hin zum Schweißen, Richten und Entgraten. Gefertigt werden Prototypen, Einzelstücke oder Serien. Marc Burkhalter ist seit neun Jahren in der Firma. Zuerst war er zwei Jahre als Betriebsleiter tätig. Anschließend hat er vom Schwiegervater, dem Inhaber des Unternehmens, die Geschäfte übernommen und agiert nun seit sieben Jahren als Geschäftsführer. Er weiß, wie wichtig die Qualität der Teile ist. Um diese verlässlich sicherzustellen, und auch um künftig effizienter und prozesssicher produzieren zu können, investierte das Unternehmen nun in zwei neue Anlagen von Lissmac. Anschub für eine der Investitionen war ein Kundenteil, bei dessen Fertigung immer wieder ein technisches Problem auftrat. Für Unternehmen, welches chirurgische Instrumente entwickelt und vertreibt fertigt Oppliger seit mehreren Jahren Komponenten für Sterilisierschalen, welche später im Voroperationssaal zur Vorbereitung des OP-Bestecks eingesetzt werden. Die Stanzteile, die beim Kunden weiterverarbeitet werden, erhalten bei Oppliger durch anschließendes Schleifen ein abgestimmtes Oberflächenfinish. Und genau hier entstand das Problem: ein Sekundärgrat. Dazu kam, dass der Kunde immer höhere Stückzahlen beauftragte. Service ist wichtiges EntscheidungskriteriumDer Sekundärgrat musste oft von Hand weggeschliffen werden. Die alte Anlage war zudem häufig überlastet. Im Jahr 2018 war dann die Grenze erreicht. „Die wiederholte Unzufriedenheit mit der Qualität der Bauteile und die aufwendige manuelle Nachbearbeitung der Bauteile stellten weder den Kunden noch uns zufrieden. Für Medizintechnikprodukte sind ein passgenaues Oberflächenfinish und eine saubere Weiterbearbeitung schließlich unabdingbar. Wir mussten handeln“, blickt Marc Burkhalter zurück. Eine prozesssichere Lösung war also gefragt. Gemeinsam mit dem Kunden wurden vor der Neuanschaffung die Qualitätsanforderungen definiert. Und bei Oppliger wurde außerdem geprüft, inwieweit sich die Investition perspektivisch rentieren wird.Die konkrete Anwendung für die anzuschaffende Anlagentechnik war gegeben und so standen die Eckdaten für die neue Maschine auch schnell fest: Es sollte eine kompakte Anlage sein, denn der zur Verfügung stehenden Platz in der Halle war begrenzt. Und Marc Burkhalter nennt einen weiteren Entscheidungspunkt: „Wichtig war für mich, dass ich einen Ansprechpartner für den Schleifbereich habe. Ich wollte auch in diesem Punkt mit unserem langjährigen Servicepartner Wolfgang Kohler zusammenarbeiten. Hier klappt die Kommunikation, der Service funktioniert und eine schnelle Ersatzteilbeschaffung ist gewährleistet.“ Die WKS GmbH – Wolfgang Kohler Service GmbH mit Sitz in Bad-Zurzach in der Schweiz – ist als Service- und Vertriebsunternehmen auf Richt- und Entgratmaschinen spezialisiert. Zum Portfolio gehören auch Lissmac-Anlagen. Universelle Einstiegsmaschine für die Gratentfernung Der Entscheidungsprozess lief zügig. Das Teilespektrum und die räumlichen Gegebenheiten waren gesetzt. Und so entschied sich der Schweizer Blechbearbeiter im Jahr 2020 für eine Trockenschliff-Anlage SBM-M 1000 S2 von Lissmac. Die Schleif- und Entgratmaschine ist eine universelle Einstiegsmaschine für die Entfernung von Schneidgraten bei Laser- und Stanzteilen. Die Blechteile erhalten zudem einen optimalen Oberflächenschliff. Bertrand Laroche ist Area Sales Manager Metal Processing bei der Lissmac Maschinenbau GmbH. Er hat den Prozess begleitet. „Die SBM-M 1000 S2 ist hinsichtlich des Aufbaus und der Bedienung eine funktionelle Maschine. Für die Applikation bei Oppliger hat die Anlage genau gepasst“, sagt er. Durch die zwei gegenläufigen Bänder sowie die beidseitige Bearbeitung sei keine Zurückführung der Teile erforderlich. Zudem sei weniger Stellfläche erforderlich. Der Maschinentyp stand also schnell fest. Nach einem Besuch des Vorführzentrums von Lissmac in Bad Wurzach wurde lediglich die Anlagenauslegung sowie die Absaugung angepasst und das Schleifkorn konkretisiert. Gekauft und installiert wurde die Schleif- und Entgratmaschine dann im Jahr 2020. „Unser Kunde ist zufrieden. Seitdem die neue Anlage im Einsatz ist, gibt es keinerlei Probleme mehr mit dem Sekundärgrat. Zudem hat sich die Oberflächenqualität durch das feine Schleifkorn noch etwas verbessert“, freut sich Marc Burkhalter. Anfangs wurden auf der neuen Anlage ausschließlich Teile für den Hersteller der medizinischen Instrumente gefertigt. Zwischenzeitlich wird sie auch für andere Anwendungen genutzt, insbesondere für Teile, die beidseitig bearbeitet werden sollen. Dies sind überwiegend Industrieteile aus Edelstahl-Dünnblech. Scharfe Kanten an dünnen Edelstahlteilen entfernen, kostensparend und mit wenig Energieaufwand - das ist der Fokus der SBM-M 1000 S2. „Für Lissmac war dies die erste Applikation bei der Lyssacher Firma. Es ist schön, dass wir dieses seit langem am Markt bewährte Anlagenkonzept hier platzieren konnten“, freut sich Gebietsverkaufsleiter Bertrand Laroche. Powergrip-Gurt gewährleistet Effizient und Flexibilität Ein Jahr später stand eine weitere Ersatzbeschaffung an. Die Vorgängeranlage lief unzuverlässig, hatte ein hohes Ausfallrisiko und die Ersatzteilbeschaffung war schwierig. Dazu kam, dass auch kleinere Teile bandentgratet werden sollten. Oppliger schaute sich auf den gängigen Messen um. Und mit dem Wissen, dass Lissmac ebenfalls Anlagen in diesem Segment herstellt, ist die Schweizer Firma diesmal auch gezielt auf den Bad Wurzacher Maschinenbauer zugegangen. Die Eckdaten für die neue Anlage standen fest: Bearbeitung eines möglichst großen Teilespektrums an Edelstahlteilen, also eine hohe Flexibilität. Und auch diesmal sollte es wieder eine möglichst kleine Baugröße sein. Außerdem sollte neben den gesetzten Funktionalitäten das Preis- Leistungsverhältnis stimmen und die Lieferfristen sollten akzeptabel sein. Zudem sollte die Wolfgang Kohler Service GmbH wieder als Partner agieren. Entschieden hat sich Marc Burkhalter für die Entgratmaschine SMD 123 RE. Technisches Highlight der Anlage ist auch hier der Powergrip-Gurt, auf dem die Teile bei der Bearbeitung liegen und durch die hohe Haftkraft und ohne Magnet oder Vakuum fixiert werden. „Wir sind die einzigen, die in der Branche mit einem solchen Transportgurt arbeiten. Das heißt: Gegenüber dem Kunden ist ein höherer Beratungsaufwand erforderlich als bei anderen, bekannten Technologien“, sagt Bertrand Laroche. Doch der Powergrip-Gurt sei nicht nur flexibel, sondern auch sehr energieeffizient. Ein Vakuum, so Laroche weiter, sei beispielsweise laut, brauche viel Energie und sei nicht für alle Teilegeometrien geeignet. Marc Burkhalter ist von der Technik, die seit der Installation verlässlich läuft, überzeugt. Gefertigt werden auf der neuen Anlage eher kleinere Teile für die verschiedensten Industriebereiche sowie Teile, bei denen die Optik eine Rolle spielt und ein gutes Oberflächenfinish wichtig ist. Effizienz und Stabilität für die Zukunft Oppliger, einer der ersten Laserbetreiber in der Schweiz, fertigt für Industriekunden der verschiedensten Branchen. Derzeit werden gut 600 Tonnen Stahlblech verarbeitet, davon etwa 50 Prozent Stahl und 50 Prozent Edelstahl. Mit Blick in die Zukunft sagt Geschäftsführer Burkhalter: „Gut wäre es, den derzeitigen Stand zu halten. Dabei setzen wir auf ein gesundes Wachstum, einen passgenauen Maschinenpark, Automation und das Knowhow, verschiedenste Kunden zu bedienen. Auch schlanke Prozesse sind wichtig: Die Effizienz soll in allen Bereichen ausgebaut werden, sowohl im Büro als auch in der Produktion.“ Auch Gebietsverkaufsleiter Laroche blickt nach vorn: „Wir möchten unsere Kunden zukünftig mit effizienteren Schleifmitteln unterstützen. Daran arbeitet Lissmac gemeinsam mit Schleifmittelherstellern. Dadurch soll die Leistung der Maschine verbessert und optimiert werden, also die Qualität und Performance gesteigert werden. Und mit Blick auf geeignete Anlagentechnik werden auch die Themen Fernwartung und Digitalisierung zunehmend umgesetzt.“ Kontakt:Ulrich Oppliger AGMarc BurkhalterIndustriestrasse 23421 Lyssach, Schweizwww.uoppligerag.ch*** Lissmac Maschinenbau GmbHBertrand LarocheLanzstraße 488410 Bad Wurzachwww.lissmac.com Textautor:Annedore Bose-MundeFreie Fachjournalistin für Technik und Wirtschaft in Erfurt www.bose-munde.de
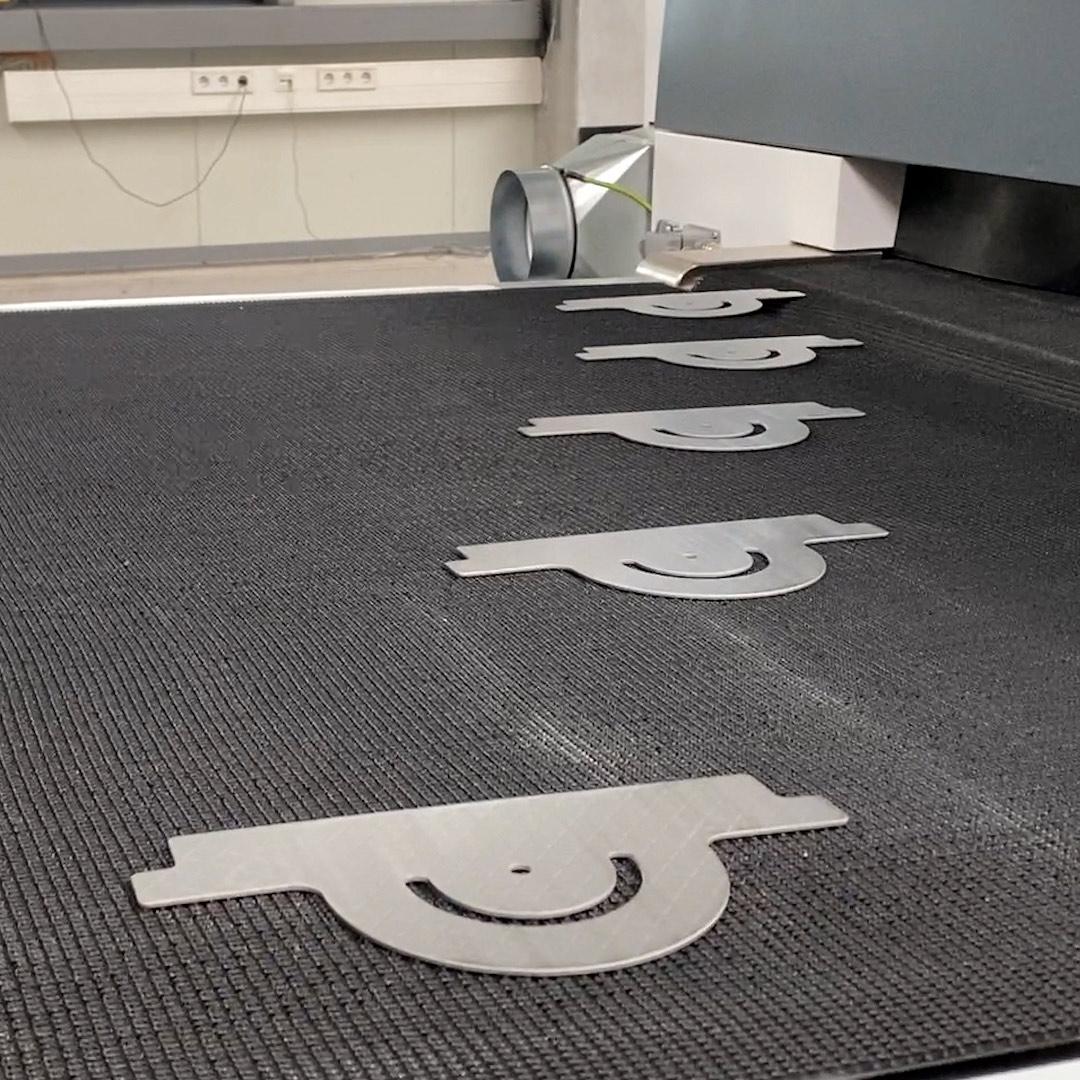
Wertschätzung für die Blechbearbeitung
Vor sechs Jahren starte ein Unternehmer in Bad Salzuflen im Bereich der industriellen Blech- und Metallfertigung. Mit seinen Investitionen in neue Anlagentechnik und der vier Jahre später erfolgten Gründung eines zweiten Unternehmens im Bereich Edelstahlfertigung verfolgt er klare Ziele: konsequente Materialtrennung, hohe Qualität und zufriedene Kunden.Text: Annedore Bose-MundeDie Blechwerk Bürger GmbH ist ein klassischer Zulieferer. Neben dem Laserkantteil mit oder ohne Kantenverrundung gehört auch die Fertigung ganzer Baugruppen zum Portfolio, angefangen von Schweißbau-Komponenten mit Pulverbeschichtung bis hin zur Endmontage. Das Unternehmen agiert über die ostwestfälischen Grenzen hinweg und setzt auf eine individuelle Kundenbetreuung sowie ein Miteinander auf Augenhöhe. Markus Bürger hat das Blechwerk im Jahr 2017 in Bad Salzuflen gegründet. Die Lico Metall Design GmbH & Co.KG wurde dann 2021 gegründet, der Unternehmens-Standort in Werther im Herbst 2022 bezogen und im Januar 2023 war hier der Start für die Produktion. Für die beiden Standorte gibt es ganz pragmatische Gründe. Zum einen ist es der Fokus auf das Material und zum anderen auf den Kundenkreis. Das Blechwerk Bürger ist auf die reine Stahlverarbeitung spezialisiert, Lico dagegen auf die Verarbeitung von Edelstahl und somit auch auf die Reinheit der Verarbeitung. Zudem werden durch die beiden Standorte auch unterschiedliche Kunden angesprochen und zwei Vertriebswege abgedeckt. „Beide Standorte sind 25 Kilometer, also etwa 30 Autominuten voneinander entfernt. Wir erreichen dadurch teilweise völlig unterschiedliche Kunden. Zudem möchten wir das Potenzial des Edelstahlmarktes mit Lico konsequent nutzen“, sagt Geschäftsführer Markus Bürger. Mit der Blechwerk-Neugründung und später mit dem Start von Lico wurde sukzessive in verschiedene Anlagentechnik investiert. Die erste, beidseitig bearbeitende Lissmac-Anlage wurde bereits kurz nach der Neugründung im Jahr 2018 angeschafft: eine SBM-M 900 S2. „Das war eine kleine, handliche und finanziell überschaubare Entgratmaschine. Nachdem diese zweischichtig ausgelastet war, haben wir 2022 in eine weitere Lissmac-Anlage investiert. Wir wollten den Prozess optimieren und effizienter gestalten“, blickt Bürger zurück. Mit der Entgratmaschine SBM-L 1500 G1S2 konnte dann nicht nur ein größeres Teilespektrum bearbeitet werden. Durch das Zulauf- und Ablaufband wurde auch die Effektivität in der Bearbeitung deutlich erhöht. Für Bürger war es von Beginn an wichtig, eine hohe Qualität sicherzustellen. Die Kunden sollten keine Teile mit Grat bekommen, der gerade bei lasergeschnittenen Teilen prozessbedingt entsteht. So werden die Werkstücke auf mögliche Nachfolgeprozesse wie das Schweißen oder Beschichten entsprechend vorbereitet.Beidseitige Bearbeitung in einem Arbeitsgang war der Türöffner Beim Kauf der Anlagentechnik ist Bürger bereits beim Unternehmensstart pragmatisch vorgegangen. So war ihm die Nähe zum Lissmac-Standort in Beckum wichtig. Dort informierte er sich über geeignete Maschinen, die seine Anforderungen und Eckdaten erfüllten. Dirk Schürstedt, Gebietsverkaufsleiter Metal Processing bei der Lissmac Maschinenbau GmbH, demonstrierte ihm die Möglichkeiten der Schleif und Entgratmaschine SBM-M S2. Die Anlage kann zur flexiblen Kantenverrundung genutzt werden. Durch die beidseitige Bearbeitung der Innen- und Außenkonturen in einem Arbeitsgang wird eine hohe Prozesseffizienz und Zeitersparnis erreicht. Die Anlage war kurzfristig verfügbar und so wurde dann auch nicht lange überlegt. „Ich entscheide schnell, wenn ich ein gutes Gefühl habe“, sagt Markus Bürger. „Hier hat nicht nur die Chemie gestimmt. Mich hat die Nähe zu Lissmac überzeugt. Und natürlich das beidseitige Bearbeitungsprinzip sowie die technischen Möglichkeiten, die die Anlage bietet und letztendlich auch die kurze Lieferzeit.“ Bei der Anschaffung der zweiten Anlage, die aufgrund des gestiegenen Auftragsvolumens nötig wurde, stand dann wieder eine Lissmac-Anlage im Fokus. Gegenüber der ersten Anschaffung, der SBM-M S2, ist die Entgratmaschine SBM-L 1500 nun deutlich größer. Neben der Arbeitsbreite von 1500 Millimetern, durch die ein breiteres Teilespektrum abgedeckt werden kann und so Kundenwünsche besser bedient werden können, verspricht sich Bürger perspektivisch auch eine Kostenersparnis bei den Schleifmitteln. Dazu kommt, dass durch die vor- und nachgeschalteten Transportbänder mehrere Teile gleichzeitig aufgelegt werden können. Das bedeutet für die Mitarbeiter eine deutliche Arbeitserleichterung. Durch ein zusätzliches Schleifband können zudem die beim Laserschneiden entstandenen Grate effizienter nachbearbeitet werden. Markus Bürger ist mit seinen beiden Unternehmen ein zufriedener Lissmac-Kunde. Mit Blick auf die Technik und mit Blick auf den Service, der beim Auftreten von Problemen sehr zeitnah reagiert. Und so soll Lissmac auch bei einem neuen geplanten Projekt mit im Boot sein. „Ab Herbst 2023 sollen die Laserteile, die dann auf einer neuen Tru Laser 5030 mit Fiber Technologie gefertigt werden, direkt mit einem Astes Sortiersystem an eine Doppelband-Schleifmaschine von Lissmac übergeben werden, um dort automatisch den Schleifprozess zu starten“, blickt Bürger voraus. Er ist zuversichtlich, was die Auftragslage betrifft, sieht großes Potenzial in der Technologie und freut sich auf die Umsetzung des vollautomatischen Prozesses.Durch konsequente Materialtrennung zweiten Kundenkreis generiert Ein Schlüsselthema für die Arbeiten im Blechwerk war und ist immer die Materialtrennung. Ursprünglich war sowohl der Stahlbereich als auch der Edelstahlbereich in Bad Salzuflen angesiedelt. Doch Bürger war mit der Lösung nicht zufrieden. Im Stahlbereich werden andere Mengen verarbeitet als im Edelstahlbereich. Die Anarbeitung der Teile unterscheidet sich und es geht natürlich auch um die Reinheit und die Verarbeitungsqualität der Edelstahlteile. Insbesondere dann, wenn die Teile für Lebensmittelanlagen- oder Medizintechnik-Hersteller genutzt werden, ist dies ein wichtiger Punkt. Um eine aufwendige Materialtrennung bei der Bearbeitung der unterschiedlichen Teile und bei allen Logistikprozessen zu vermeiden, entschied sich Markus Bürger für die Gründung der Lico Metall Design. „Die Fehlerquote ist bei einer gemischten Fertigung deutlich höher. Natürlich passiert es, dass trotz aller Aufmerksamkeit Metallstäube verschleppt werden oder die Teile mit Ölen oder Fetten kontaminiert werden können“, sagt Bürger. Deshalb habe er sich dafür entschieden, beide Materialien komplett räumlich zu trennen, um hundert Prozent Wertschöpfung erhalten zu können und um die Akzeptanz der Kunden dementsprechend zu erhöhen. Das sei die richtige Entscheidung gewesen, denn so könne mit Lico ein neuer und separater zweiten Kundenkreis erschlossen werden. Die neu gegründete Lico konzentriert sich nun auf die Fertigung hochwertiger Edelstahlbauteile - auch mit Blick auf die in der Unternehmensgruppe angesiedelte Baugruppenfertigung. Den Plan, den Edelstahl-Bereich weiter auszubauen hatte Markus Bürger bereits seit längerer Zeit. Und so suchte er nach dem passenden Grundstück, einem passenden Geschäftsführer und Mitgesellschafter sowie nach passender Technik. Während es beim Grundstück und auch bei einem geeigneten Geschäftsführer für Lico durchaus langwierig war, bis Bürger mit den Lösungen zufrieden war, ist die Entscheidung für die Lissmac-Technik schnell gefallen. Am Lico-Standort in Werther steht eine Trockenschliff-Anlage SMD 123 RE. Sie wird für das Entgraten und die allseitig gleichmäßige Kantenverrundung aller Werkstückkanten an Außen- und Innenkonturen sowie ein optimales Oberflächenfinish der Edelstahlteile genutzt. Zudem steht an dem Standort eine SBM-M 1500 zur Verrundung von Kanten.Mehr Wahrnehmung für die Zulieferer erreichen Gerade im Bereich der Blechbearbeitung wird viel Geld in die Anlagentechnik investiert. Zulieferer und Lohnfertiger müssen zudem durchweg Qualitätsarbeit leisten, um bestehen zu können. Doch die Wahrnehmung am Markt ist für Markus Bürger oft kaum gegeben. Deshalb wünscht er sich für seine Unternehmen, aber auch für die Branche, mehr Wertschätzung. „Die Blechverarbeitungsbranche leistet sehr viel. Das Potenzial, was sich hier bietet, ist riesig: neue Technologien, komplexe Automatisierung und zahlreiche Perspektiven“, sagt Bürger. Und genau dies sieht er auch als Perspektive für seine Unternehmen. „Mir ist es wichtig, ein gesundes Unternehmen zu leiten, es stabil auf dem Markt zu platzieren und zu halten sowie zudem mit guten Mitarbeitern, Lieferanten und Kunden auf Augenhöhe zusammenarbeiten.“ Diese Ehrlichkeit auf Augenhöhe schätzt auch Dirk Schürstedt vom Anlagenbauer Lissmac. „Markus Bürger sagt mir direkt, was er von einer Maschine erwartet und was gegebenenfalls verbessert werden könnte. Diese offene Kommunikation treibt uns durchaus an und bedeutet eine Herausforderung, die wir brauchen“, sagt er. Fest steht: Hier ist die beidseitige Wertschätzung gegeben - auf Augenhöhe.