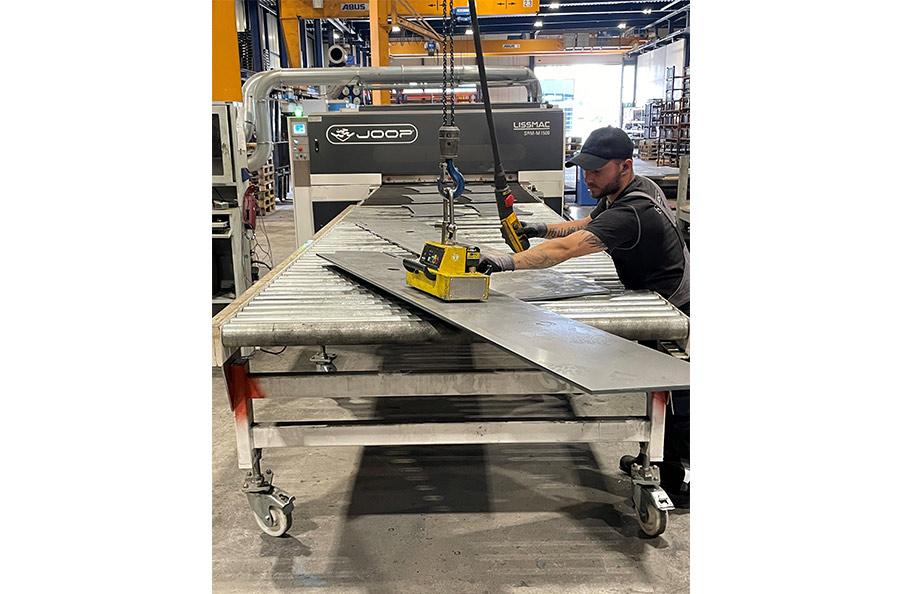
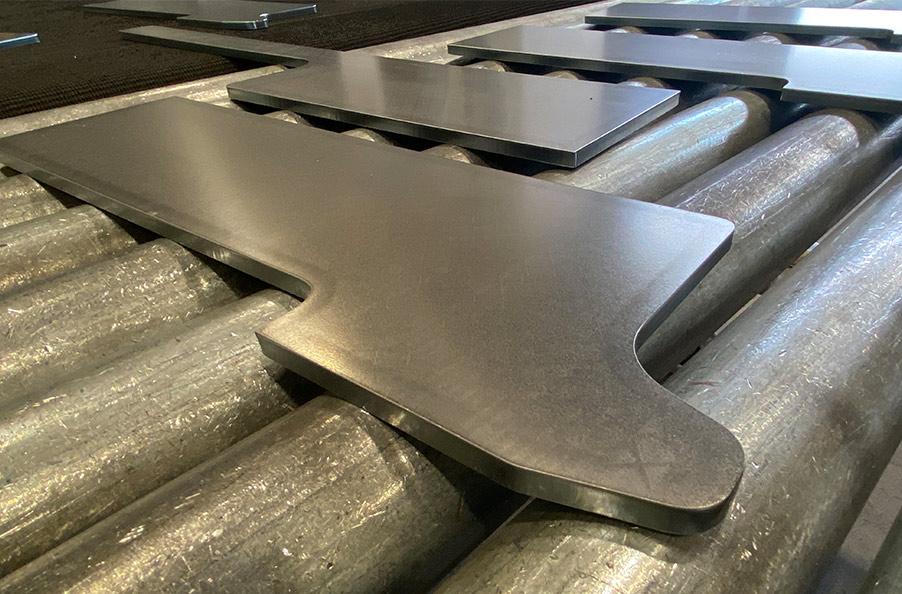
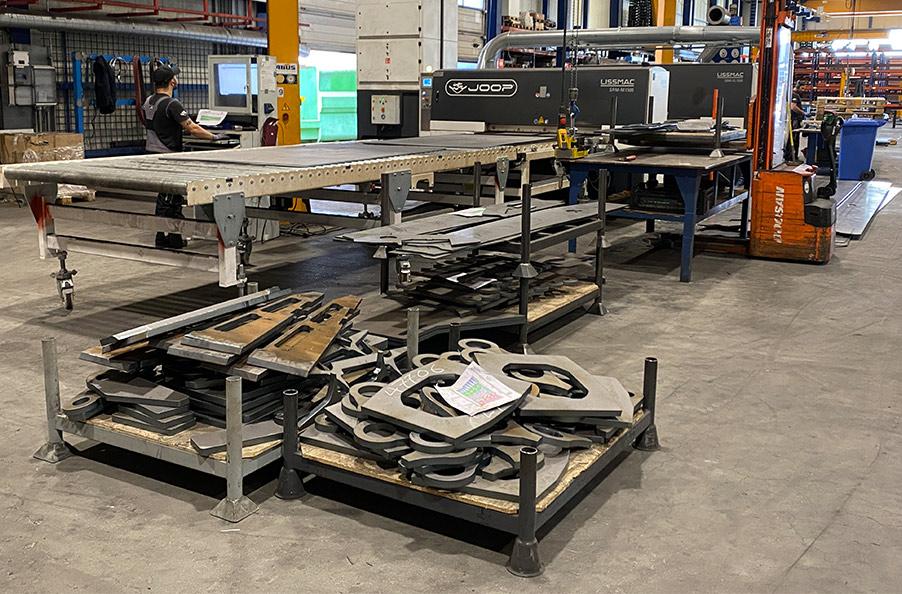
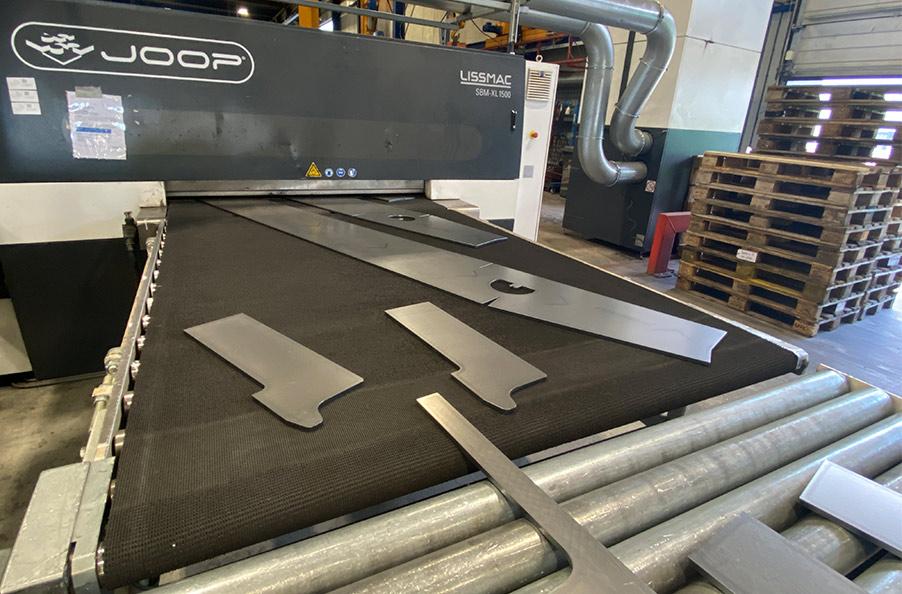
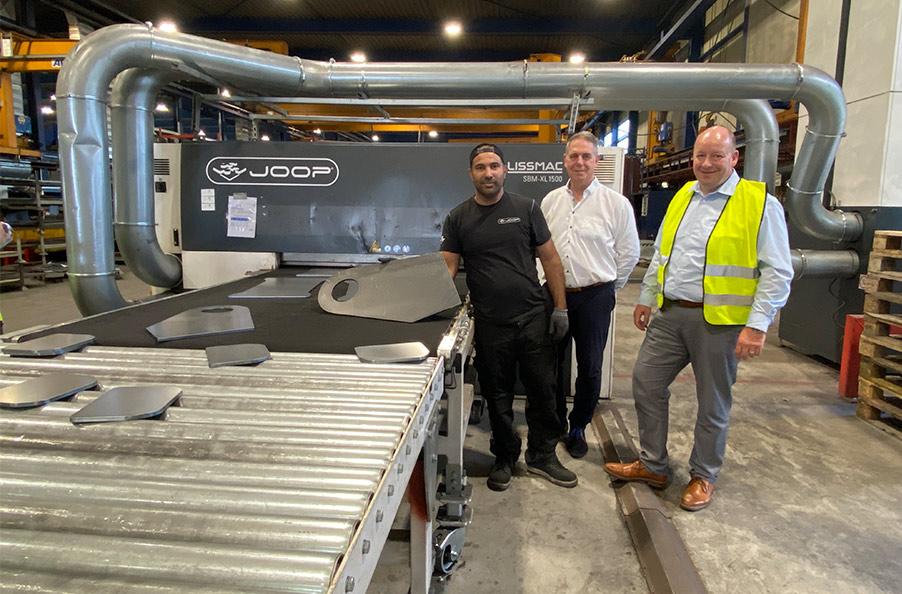
Fokus liegt vollumfänglich auf der Automatisierung
07. November 2024
Es braucht immer Visionäre und Vorreiter, um etwas Neues auf dem Markt zu etablieren. Ein niederländisches Stahlservicecenter ist so ein Vorreiter. Hier soll die Dickblechbearbeitung automatisiert werden. Ein wichtiger Lösungsbaustein dafür sind zwei neue Bearbeitungsstrecken von Lissmac die angeschafft wurden.
Text: Annedore Bose-Munde
Seit 1966 ist das Familienunternehmen Joop van Zanten als Komplettanbieter für das Plasma- und Autogenschneiden von Stahl auf dem Markt. Das Stahlservicecenter im niederländischen Veenendaal hat heute über 40 Mitarbeiter und bearbeitet Stahlbleche im Bereich von 2 mm bis 300 mm. Dazu kommt Bohren und Gewindeschneiden, Abkanten, Richten, Strahlen und Schweißen.
Bart Kroesbergen ist seit 2018 Betriebsleiter bei Joop van Zanten. Er blickt zurück: „Vor sechs Jahren gab es bei Joop van Zanten noch viel Handarbeit. Doch gerade mit Blick auf die Wettbewerbsfähigkeit, den Fachkräftemangel und die Zukunftsausrichtung sollte sich etwas ändern.“ Zwei Fragen standen dabei von Beginn an im Raum: „Können wir automatisieren, um die Arbeit attraktiver und effizienter zu machen? Und vor allem: Können wir Kosten sparen?“ Bereits 2018 war das Produktspektrum des Stahlbearbeiters sehr breit. Deshalb war ein weiterer Punkt sehr wichtig: die Flexibilität.
„Die Firma soll für die nächsten 20 Jahre aufgestellt werden. Zunehmend erfolgt eine Komponentenfertigung für Endproduzenten. Dazu wurden viele Technologien in Haus geholt, wie Schweißen, maschinelle Bearbeitungen und Kanten. Wir versuchen die Prozesse so umzusetzen, dass sie möglichst weit automatisiert sind. Damit soll die Vorhersagbarkeit bei neuen Produkten und die Reproduzierbarkeit der Produkte sichergestellt werden, ebenso eine konstante Qualität und natürlich auch die Wettbewerbsfähigkeit in Europa“, definiert Managing Director Kroesbergen den Weg und das Ziel.
Seit 2018 hat das Familienunternehmen gemeinsam mit einem externen Direktor, eine neue Strategie für das Unternehmen umgesetzt. Gleichzeitig wird zudem die nächste Familiengeneration auf eine Managementposition vorbereitet. Zusammen mit Bart Kroesbergen, der einen umfassenden betriebswirtschaftlichen Hintergrund hat, konnten so Erfahrung, Wissen und der gemeinsame Veränderungswille bereits viel bewegen. Schon heute zählt Joop van Zanten zu den modernsten Stahlbearbeitungsunternehmen in den Niederlanden, zeichnet sich durch seinen hohen Automatisierung- und Digitalisierungsgrad aus und treibt das Thema Industrie 4.0 konsequent voran.
Investition in zwei effiziente, baugleiche Anlagen
Der Kundenkreis von Joop van Zanten hat sich in den letzten Jahren geändert. Anfangs agierte das Unternehmen überwiegend als Massen-Stahl-Schneidebetrieb. Es ging um Kilogramm und schweren Stahl. Die Kunden kamen beispielsweise aus dem Brücken- oder Schiffbau. Doch das Unternehmen wollte und sollte flexibler werden und das Leistungsspektrum erweitern - auch mit Blick auf die Materialdicken. Jetzt liegt das Spektrum der verarbeiteten Materialdicken im Bereich von 2 mm bis 300 mm. Derzeit ist das kleinste Produkt einige Zentimeter groß, das größte fast 14 Meter. Insgesamt 90.000 verschiedene Teile wurden im Jahr 2023 gefertigt. Die Kunden kommen heute meist aus der Industrie, dem Maschinenbau und dem Transportbereich. Der Fokus der Fertigung liegt darauf, die Kunden mit einem kompletten Endprodukt zu beliefern, welches effizient gefertigt wurde. Die Prozesse sollen dabei so weit automatisiert werden, dass eine hohe Wirtschaftlichkeit abgebildet wird.
Um diese Ziele zu erreichen, investierte das niederländische Unternehmen in zwei baugleiche Lissmac-Anlagen, jeweils bestehend einer Schlackeentfernungsmaschine SBM-M 1500 D2, einer Schleif- und Entgratmaschine SBM-XL 1500 G2S2 (Durchlassbreite beider Anlagen ist 1.500 mm) sowie Absaug- und Fördertechnik. Die erste Anlage wurde im Jahr 2019 gekauft, die zweite 2021.
„Wir haben mehrere Produzenten besucht, mit Anlagenvertretern gesprochen und uns auch auf den gängigen Messen umgeschaut“, blickt Betriebsleiter Kroesbergen zurück. Doch ein Punkt überzeugte die Entscheider bei Joop van Zanten schlussendlich: die beidseitige Bearbeitung, welche die Lissmac-Anlagen ermöglichen. „Wir lassen mitunter Produkte durch die Anlagen laufen, die 20 Meter lang sind. Das ist mit der Lissmac-Technik in nur einem Prozessschritt möglich und bedeutet daher eine enorme Arbeitserleichterung“, so Kroesbergen. Das ansonsten erforderliche Handling und eine damit verbundene aufwendige Logistik in den Hallen entfällt.
Bevor die Entscheidung für die Anlagenstrecke der Lissmac Maschinenbau GmbH gefallen ist, sind umfangreiche Tests gelaufen. Dies war auch aufgrund der hohen Teilevielfalt nötig. Die Praxistests erfolgten mit Blick auf die Produkte und Materialien. Es wurden Feineinstellungen vorgenommen und 2019 ist die Anlage dann in Betrieb gegangen.
„Wir haben uns entschieden, dass alle bei uns gefertigten Teile durch die Lissmac-Anlage laufen. Natürlich sind die Oberflächenqualität und die Haptik nun besser. Aber es sieht auch jedes einzelne Teil einfach richtig gut aus“, sagt Bart Kroesbergen. Allein aufgrund der technischen Anforderungen wäre dies nur bei etwa 50 Prozent aller Teile nötig. Aber zwischenzeitlich sind die entgrateten und verrundeten Teile auch ein Qualitätsmerkmal für Joop van Zanten geworden, welches die Kunden zu schätzen wissen. Und dann ist da noch der immer vorausschauende Blick des Betriebsleiters auf vollautomatisierte Prozessabläufe. „Wenn man einen zweiten Bearbeitungsstrom in einem Prozess hat, der nicht automatisiert werden soll, ist es schwieriger, ganzheitlich zu automatisieren“, sagt er.
Die zweite Anlage, die in einem anderen Produktionsbereich steht, wurde im Jahr 2021 gekauft. Die Produktionsmenge war deutlich gestiegen und bestimmte Produktionsspektren sollten logistisch effizient bearbeitet werden. Doch auch vor dem Hintergrund der Automatisierung, die noch deutlich ausgebaut werden soll, wurde diese baugleiche Anlage angeschafft.
Ziel ist Automatisierung im Dickblechbereich
Eine der beiden Lissmac-Straßen wird bereits in der automatisierten Produktion eingesetzt werden. Hier werden Stahlbleche bis zu 40 mm Dicke bearbeitet. Mit der zweiten Anlage werden Bleche bis zu 100 mm Materialdicke bearbeitet. Auch hier soll automatisiert werden.
„Die Anforderung, dass die Anlagen für eine zukünftige Automation vorbereitet sein sollen, wurde von Joop van Zanten gleich beim Projektstart der ersten Anlage benannt“, blickt Robert Dimmler, Sales Director Metal Processing bei Lissmac, zurück. Dies sei auch vor dem Hintergrund einer reibungslosen Schnittstellenkommunikation zwischen unterschiedlichen Applikationen und Anlagen ein sehr wichtiger Punkt.
Eine Anlagenstrecke, bestehend aus einer Schlackeentfernungsmaschine, einer Schleif- und Entgratmaschine sowie Absaug- und Fördertechnik, gehört für den Maschinenbauer zu den Standardapplikationen. „Doch der Blick von Joop van Zanten auf die von Beginn an angedachte Automatisierung war durchaus visionär. Eine Automation im Dickblechbereich war bis zu diesem Zeitpunkt noch unüblich“, sagt Dimmler. „Automation kennt man üblicherweise aus dem Dünnblechbereich. Dies sollte nun in den Dickblechbereich transformiert werden, in dem ganz andere Werkstückabmessungen und Teilegewichte üblich sind. Hier an der Lösungsfindung beteiligt zu sein, ist ein spannender Part und durchaus auch eine Herausforderung.“
„Unser Traum war es, innerhalb von zehn Jahren eine komplett automatisierte Fabrik zur Dickblechbearbeitung zu nutzen. Nicht die Frage ‚Werden wir das umsetzen können?‘ stand im Raum, sondern die Frage ‚Wie werden wir das konkret umsetzen können?‘“; sagt Bart Kroesbergen. Dafür seien auch Erfahrungen aus anderen Branchen mit in die Betrachtungen eingeflossen, beispielsweise aus dem Betonbau, wo es ebenfalls um sehr hohe Stückgewichte geht.
Dieses optimistische Um-die-Ecke-Blicken überzeugte auch Maschinenbauer Lissmac. „Ein Anlagenhersteller entwickelt sich auch aufgrund seiner Kundenanforderungen weiter. Und wenn man einen visionären Kunden hat wie Joop van Zanten, dann triggert das auch uns“, ergänzt Robert Dimmler. Bei neuen Umsetzungsideen gehöre es einfach dazu, das eigene Korsett auch einmal abzulegen und über den Tellerrand hinauszuschauen.
Herausforderung liegt im Stückteilgewicht und der Teilevielfalt
Das Teilegewicht, die Teilevielfalt und die Komplexität der Strukturen erfordern mit Blick auf die Automatisierung neue Umsetzungsansätze. Das mechanische Abräumen der Teile mittels Robotik ist daher momentan noch nicht vollständig umgesetzt. Hier arbeitet Joop van Zanten gemeinsam mit der Messer Cutting Systems GmbH, der Beuting Metalltechnik GmbH & Co. KG und Lissmac an einer entsprechenden Lösung. Das Ziel, an dem die beteiligten Partner arbeiten, ist eine Lösung, die das Kernteilespektrum des Unternehmens im Dickblechbereich abdecken wird. Im nächsten Jahr sollen die Anlagen automatisiert laufen.
Dass in dem niederländischen Stahlservicecenter alle Anlagen im Betrieb mit einer Software-Plattform und mit OPC UA-Schnittstellen verbunden sind, ist ein weiterer wichtiger Punkt für eine durchgängige Automatisierung. Auch Maschinenbauer Lissmac hat den OPC UA-Standard (Standard zur sicheren, herstellerübergreifenden Vernetzung für industrielle Anlagen) für die eigenen Produkte als Standard definiert.
Ein Beispiel zeigt, wie wichtig die Thematik ist: Ein Kunde von Joop van Zanten fertigt das Frame von einer Anlage, die Chips produziert. Die erforderlichen Stahlplatten, die das Stahlservicecenter hierfür fertigt, dürfen nicht mit den Händen angefasst werden, damit das Fingerfett nicht auf die Anlagen kommt. Ohne Automatisierung wäre das nicht denkbar.
Fest steht: Die Projektpartner arbeiten gemeinsam an einer durchaus visionären Aufgabenstellung. Doch um diese zu lösen, geht es um sehr pragmatische Dinge: die technische Umsetzung, den steten Austausch und das stete voneinander Lernen und einander unterstützen.