Metal processing
Attrezzature innovative per la lavorazione del metallo
Construction Technology
Tecnologia delle costruzioni innovativa per professionisti
Trabajar en LISSMAC
Innovación y diversidad baja un mismo techo
LISSMAC - Spinti dalle idee
Ci affidiamo all'esperienza e alla competenza del sistema. In questo contesto, LISSMAC Maschinenbau GmbH comprende quattro divisioni aziendali: Tecnologia delle costruzioni, lavorazione dei metalli, impiantistica e movimentazione MT. In tutto il mondo, più di 400 dipendenti in cinque stabilimenti in Germania, Francia, Stati Uniti ed Emirati Arabi Uniti garantiscono il massimo livello di soddisfazione del cliente.
Quattro ambiti di competenza
Film aziendale
News
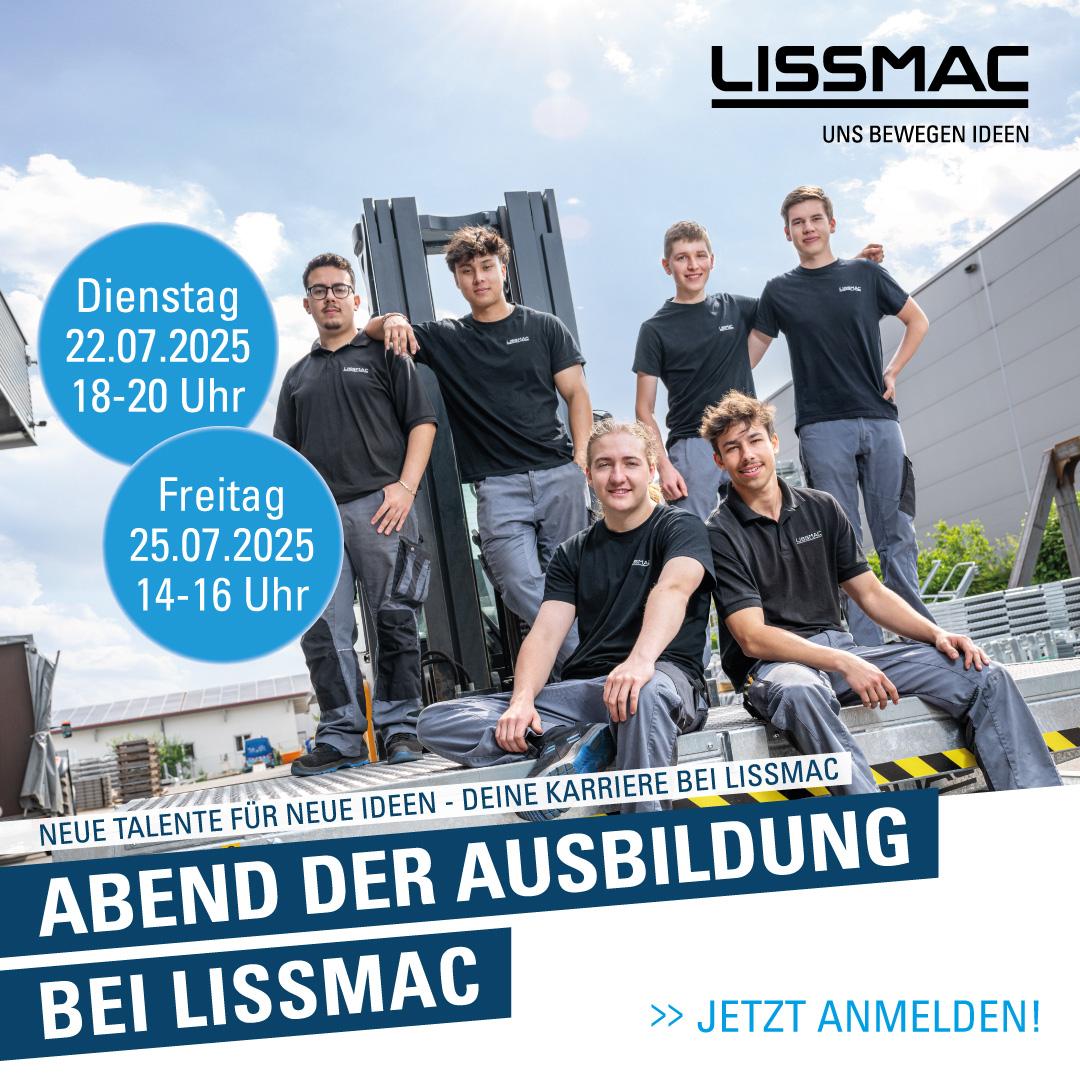
Training evening 2025
Become part of our team and visit us on the evening of training: Tuesday 22.07.2025 // 6-8 pmFriday 25.07.2025 // 2-4 pm Take a look behind the scenes Gain insights into the working environment Find out about our apprenticeships You can expect informative discussions with our trainees and training managers Parents are also very welcome Registration possible at short notice:to jobs@lissmac.com or by phone: 07564 307-202 or -228or PM via Instagram We are offering many exciting professions for the start of training in 2026.Here you can find information about the vacancies. We look forward to receiving numerous applications!
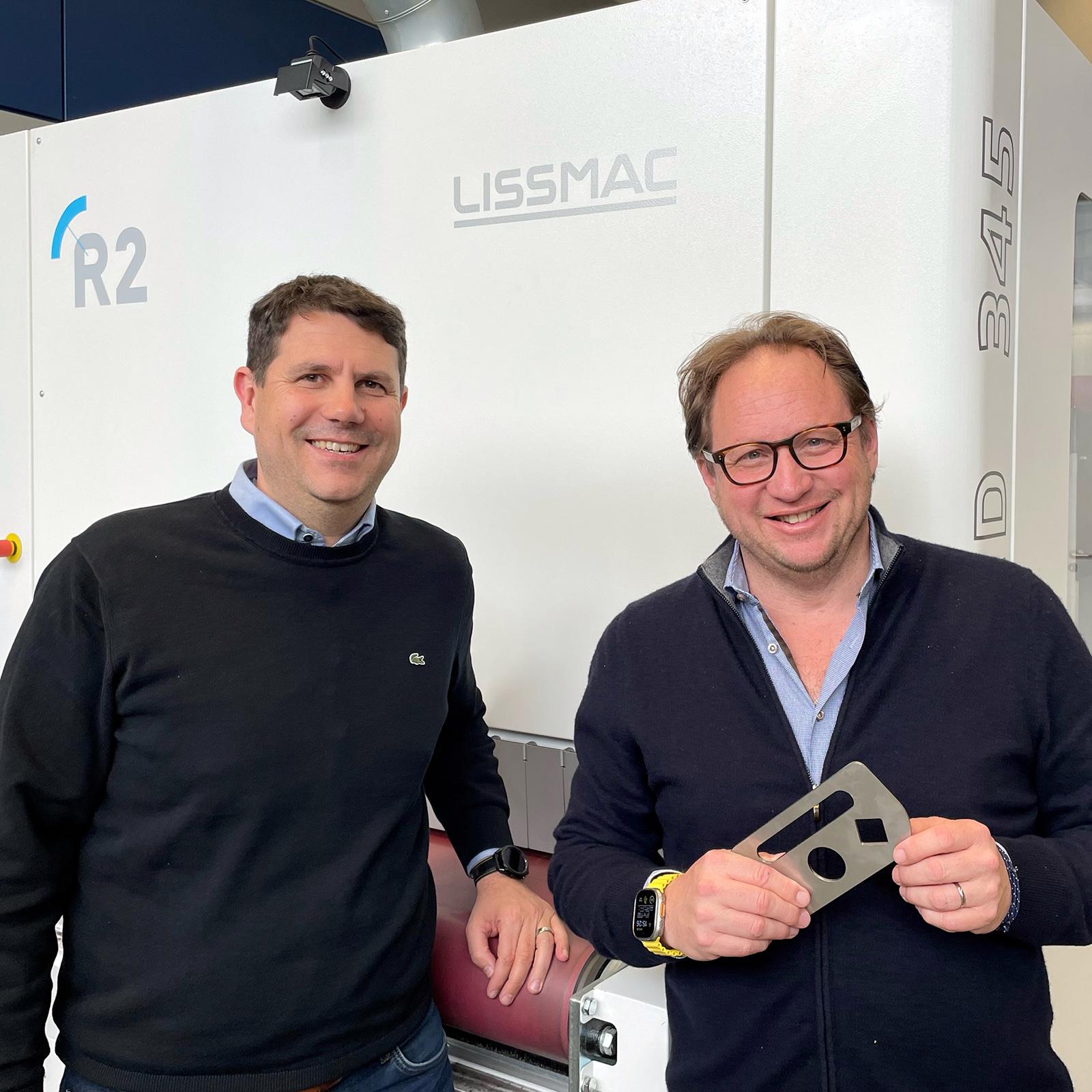
Upcoming change in management at LISSMAC
Upcoming change in management at LISSMAC Dear Ladies and Gentlemen, We would like to inform you about an important change in the management of LISSMAC Maschinenbau GmbH. Our long-standing employee and Managing Director Daniel Keller will be leaving the company on 13.04.2025. His successor, Mr. Thomas Hoffmeister, has already been in office since 01.02.2025 and will manage the company together with Dr. Hinrich Dohrmann. Daniel Keller:Last year, after careful consideration, I made the decision to reorient myself professionally after more than two and a half decades at LISSMAC and take up a position outside the company. This decision has not been easy for me, as LISSMAC has always been a matter close to my heart. I started my career at LISSMAC in 1998, which took me through various positions and departments, and I was appointed Managing Director at the beginning of 2022. In these more than two and a half decades, I have been able to contribute to the development of LISSMAC and help shape it in my various areas of responsibility. It was a very intense time that shaped my life and that I would never want to miss. We achieved a lot together. These successes are the result of joint efforts and the tireless commitment of all employees. I would like to thank all my colleagues, business partners and customers for their trusting cooperation and support. The experience and relationships that I was able to build up during my time at LISSMAC will continue to accompany me in the future. My name is Thomas Hoffmeister - I am the new Managing Director at LISSMAC Maschinenbau GmbH: At 53 years old, I bring not only experience but, above all, passion and an entrepreneurial spirit. Born in Germany and raised in Italy, Switzerland, and the USA, I learned early on that success stems from responsibility, consistency, and innovation – values that continue to drive me today. Coming from a family of entrepreneurs, I was taught from a young age the importance of entrepreneurial thinking, responsibility, and sustainable action. After studying Manufscturing Engineering at Boston University and earning an MBA from the London Business School, my career took me around the globe – from Thailand to Egypt to China. Positions at ABB and Dresdner Bank provided me with valuable insights before I founded my own company in 2016, which I have since sold. Now, I’m excited to drive LISSMAC forward with full energy together with an outstanding team. Our company is excellently positioned to not only meet the challenges of the future but to set new standards. With strong employees, a solid market position, and strategic investments in our site in Bad Wurzach, we have everything we need for enduring success. Let’s shape the future together!
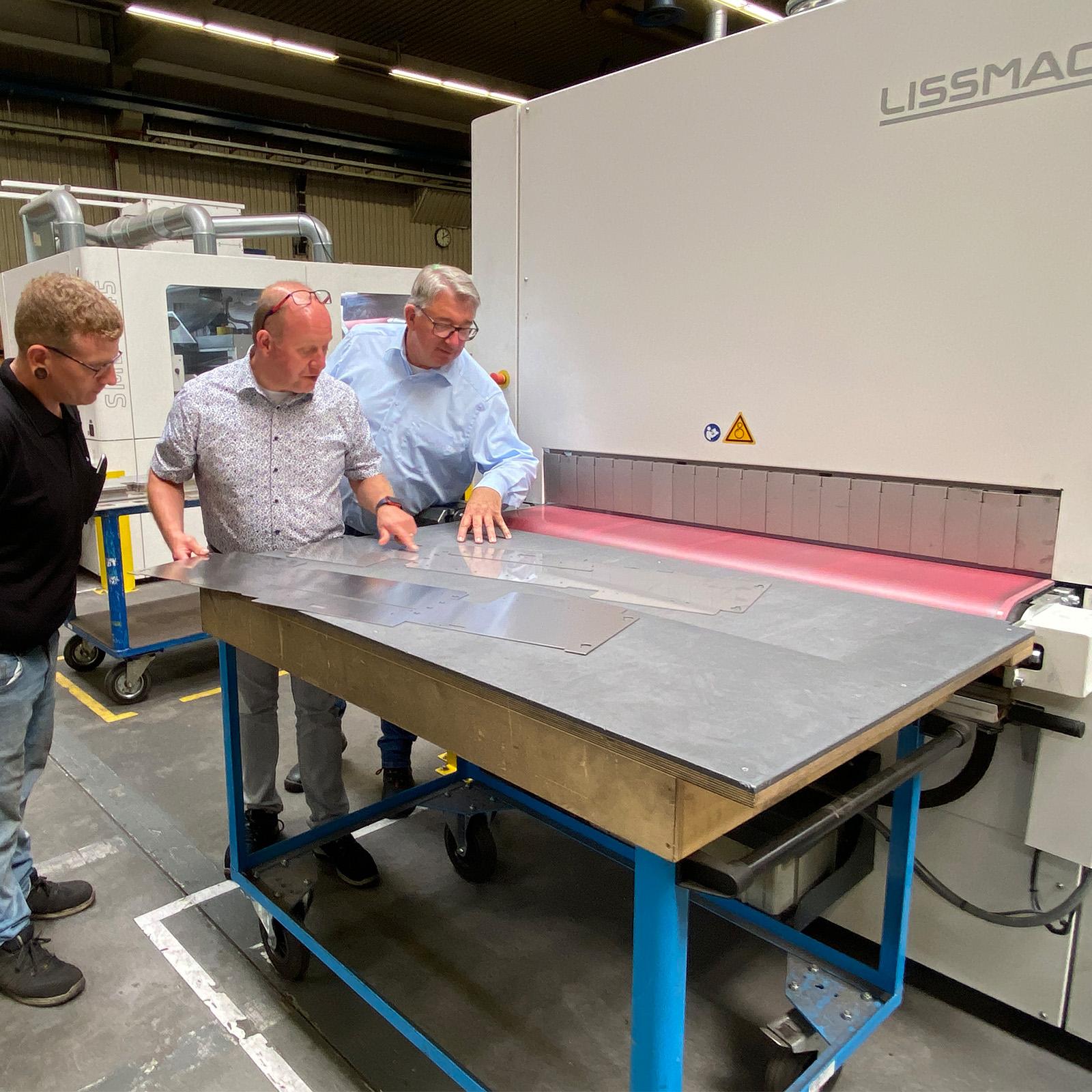
Burr-free sheet metal parts for pay stations and signaling technology components
Burr-free sheet metal parts for pay stations and signaling technology components Fiber lasers in particular require a powerful downstream deburring technique due to the burrs that occur during cutting. A global company from North Rhine-Westphalia has invested in this technology multiple times and, in doing so, has developed optimized production logistics and a continuous material flow. Text: Annedore Bose-Munde The production know-how that goes into the things we encounter every day is often not apparent at first glance, for example in parking or signaling solutions. The family-owned company Scheidt & Bachmann, based in North Rhine-Westphalia, manufactures pay stations and terminals worldwide, for example for parking garages or buses, as well as signaling technology components and barrier systems, for example for Deutsche Bahn. Founded in 1872, the company has grown from a machine manufacturer to a global system provider with a total of around 3,500 employees worldwide. Scheidt & Bachmann's prefabrication is based in Mönchengladbach, with assembly lines in Slovakia and the USA. 90 percent of Scheidt & Bachmann's production is stainless steel parts, as well as some aluminum and steel parts. In the sheet metal processing area in Mönchengladbach, 90 employees manufacture a broad portfolio of sheet metal products. The demands on the processing results and the processing technologies have increased continuously in recent years. Before 2006, laser cuts were placed on pallets after cutting, stacked and then removed individually. These were then sanded manually and with simple technology. This was quite laborious and required a great deal of manual effort and sometimes multiple passes. Throughput times, logistics and costs were less than ideal. The first Lissmac system was purchased in 2006 to address the issue of edge rounding: an SBM S 1000 for processing sheet metal and laser parts. Since then, rounding the inside and outside contours on both sides in a single operation has significantly increased process efficiency and saved time. What was still missing at that time was structured, customized production logistics. Fiber laser was supplemented with powerful deburring technology When the next step of modernization and investment in new plant technology was to be taken in 2019, several criteria were on the agenda: By purchasing a laser from the company Trumpf with fiber technology, the decision-makers at Scheidt & Bachmann relied on the technological advantages of the process. The purchase of the new cutting technology therefore also directly required modern and powerful deburring technology. And with a view to protecting employees, ergonomic improvements for the workers were also to be achieved. So, before purchasing the new system, two system manufacturers were contacted and reference parts were sent for sample processing. In the end, the decision was made in favor of an SBML 1500 from Lissmac, which is used for deburring and edge rounding on both sides. “This system performs double-sided processing in a single grinding pass. And the quality is so good that a single pass is actually enough to achieve a high-quality grinding result,” says Jörg Würker, Head of Mechanical Production and Head of Sheet Metal Processing at Scheidt & Bachmann GmbH. Time-consuming rework is no longer necessary. And he mentions another important aspect: occupational safety for technicians, which of course applies in the US. “If there is a sharp-edged item on an assembly line, the technician can be injured. And that can quickly lead to a legal problem,” says Würker. The fact that the technical parameters were also handed over with all the test parts was also very helpful, especially in the start-up phase with the new system. “We definitely benefited from that,” says Würker. Dirk Schürstedt, Area Sales Manager for Metal Processing at Lissmac Maschinenbau GmbH, who has been looking after Scheidt & Bachmann since 2019, also remembers the initial contact and a pragmatic and constructive decision-making process. He adds: “All sample processing at Lissmac is always documented precisely and comprehensively and made available to the customer. This includes which machine was used for the processing, which tool, which speeds, which rotational speeds, and so on.” This enables the customer to achieve good processing results right from the start. Over time and based on production experience, the system is then usually fine-tuned so that it can be better and better aligned with the processes. The workers initially had to get used to handling the new system technology, so targeted operator training in the user interface was carried out. All in all, Jörg Würker and Dirk Schürstedt agree that the project was implemented quickly and constructively. Today, the system is used to process sheets with thicknesses from 0.8 to 10 mm. The size of the respective sheet metal blanks ranges from the size of a cell phone to the size of a table. In 2023, the system was also retrofitted with a wet extraction system to enable aluminum to be processed and to ensure material separation. Creation of optimized production logistics When the SBM L 1500 was purchased in 2019, it became clear that the production logistics needed to be optimized. When two fully automated Trumpf fiber laser cutting machines with a connected Stopa storage system were purchased in 2021, the issue came up again and should now be thought through to the end. “When the employee removes the part from the laser system, they should also place it directly on the grinding machine. The continuous material flow was important to us and should be implemented,” says Würker. This was also to avoid manual work and long throughput times. Accordingly, two more systems were purchased in 2022 that could be used to implement this seamless process. “We rely on stable and functional relationships. That is why we chose Lissmac technology again – this time for two systems with rotary brushing technology that allow us to deburr and also round edges in an adjustable quality and depth,” says the sheet metal processing manager. “We purchased two SMD 345 S-Edition universal grinding and deburring machines. Both systems work in single-sided operation this time. However, they can be used to create a defined surface finish such as classic brush sanding. This enables greater flexibility and saves purchasing costs,” adds Lissmac specialist Schürstedt. With flexibility in mind, these two systems were also equipped with a wet extraction system. Technology support is important One thing is certain: Scheidt & Bachmann is very satisfied with the processing results of the Lissmac systems. “Since the new systems have been in use, we have been reliably achieving excellent deburring results,” says Jörg Würker. In addition, the company receives targeted technology support and reliable service. For Dirk Schürstedt, it is important to be able to respond to the customer's individual production conditions and requirements with precisely tailored technology. “It's satisfying to be able to support the customer's needs over the years. As the machine manufacturer, we are also constantly developing the systems further. Customer feedback is important for this,” he says. Currently, a major focus is on the operability of the systems. These should be as simple and self-explanatory as possible to use in order to make the operator's work easier.
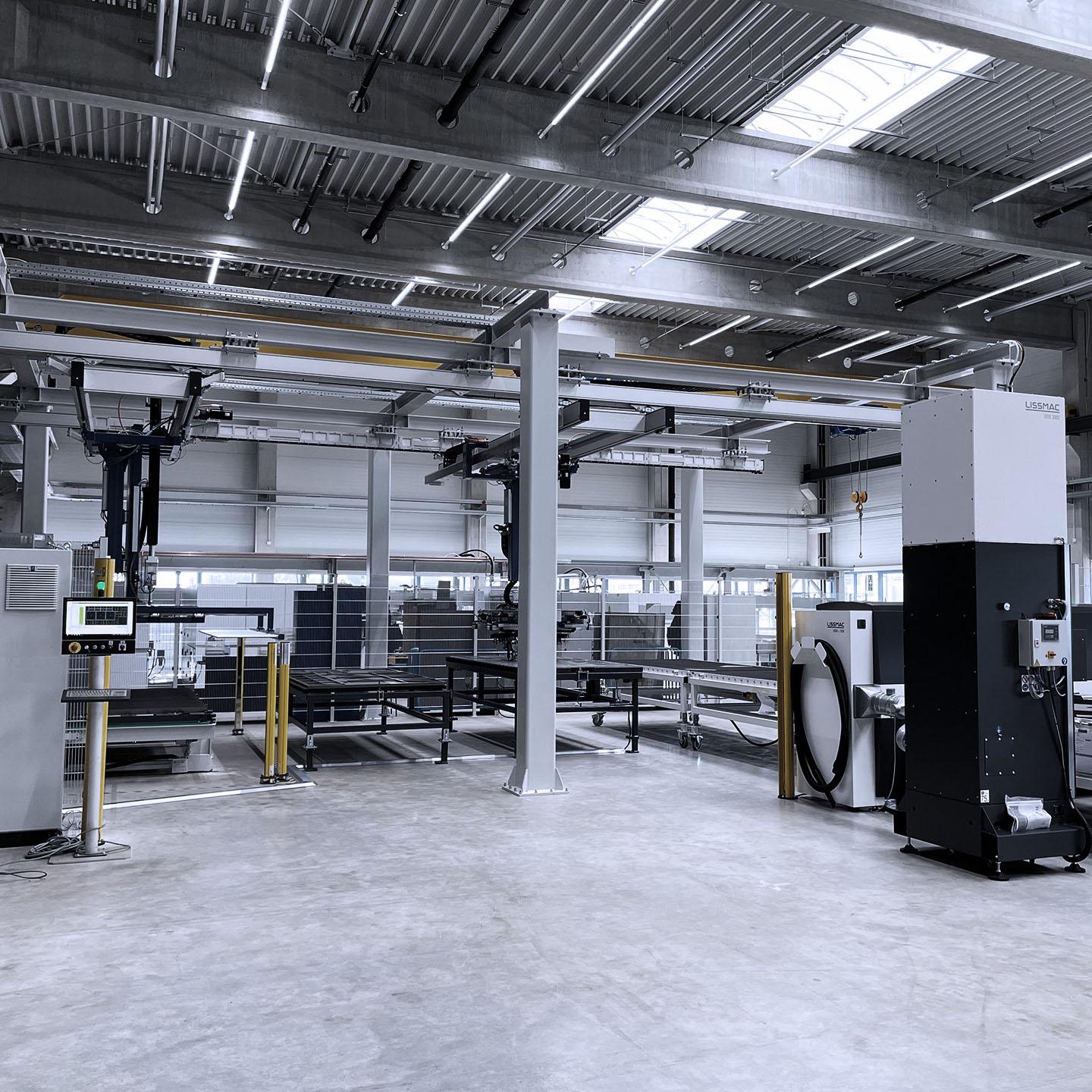
Lissmac automates grinding and deburring technology with partners
Automated processes ensure efficiency in sheet metal processing. Take, for example, the automated ejection unit that Lissmac Maschinenbau GmbH is presenting at Euroblech. It is used to separate laser components that are attached to micro bars on the sheet metal panel. Four separately controllable gripper units equipped with a vacuum suction cup selectively remove the laser components from the scrap grid after the micro-bars have been separated by the ejection process. The components are then placed on a conveyor belt for the next process steps - deburring and edge rounding. The system does not require optical image processing as it is based on the geometry data of the cutting plan and automatically determines the required number of suction pads. It can be flexibly adapted for different sheet sizes and thicknesses. The possible component sizes in the current system version range from DIN A5 to Euro pallet format. Sheets with thicknesses from 1 mm to 8 mm and a maximum weight of 90 kg can be processed. Time-consuming manual clearing is no longer necessary. The process is decoupled from laser cutting thanks to a buffer space in the warehouse. The ejection unit can be retrofitted to existing cutting systems or high racks and can be used regardless of the manufacturer. The automation unit, which the Bad Wurzach-based machine manufacturer developed together with J. Schmalz GmbH, automates the loading of Lissmac grinding machines. The cell relies on robotics technology as well as AI software and 3D vision sensors from the automation technology manufacturer. The components are identified with the help of visual 3D component recognition from Schmalz in order to pick up unmixed components from a pallet. They are then placed on a conveyor belt using a matrix gripper. They can then be deburred in the next process step.The combination of loading robots with the vacuum grippers from Schmalz and the connection to the sanding system ensures more efficient production processes: Manual loading is reduced so that a deburring machine can be operated by a single person. The SBM-L Evo series will also be presented as a pre-series model for the first time at Euroblech. On show will be the SBM-L 1000 G1S2 Evo - a deburring machine for deburring and edge rounding on both sides of punched, laser-cut and fine plasma-cut sheets in a single work step. The new top model of Lissmac's double-sided deburring machines has been available as a series machine since April 2024 From the Lissmac product range of single-sided and double-sided grinding and deburring machines for thin and thick sheet metal processing, the SBM-L 1500 G1S2 for highly efficient double-sided deburring and edge rounding of punched, laser or HD plasma-cut parts and the SMD 35 REER (S-Edition) for uniform edge rounding on all edges up to a radius of 2 mm as well as for a non-directional finish and small parts and thin sheet metal processing will also be on show in Hanover. The SMD 123 RE will also be presented, which can be used for deburring and uniform edge rounding on all edges as well as for surface processing of workpieces made of steel, stainless steel and aluminum. Also on show will be the SBM- XS 300 G1E1 Alu Mix for deburring and even edge rounding of small parts in a single operation. Visitors are cordially invited to the Lissmac stand, Hall 14, Stand 14-K06, to find out more about proven technologies and the new features for Industry 4.0.
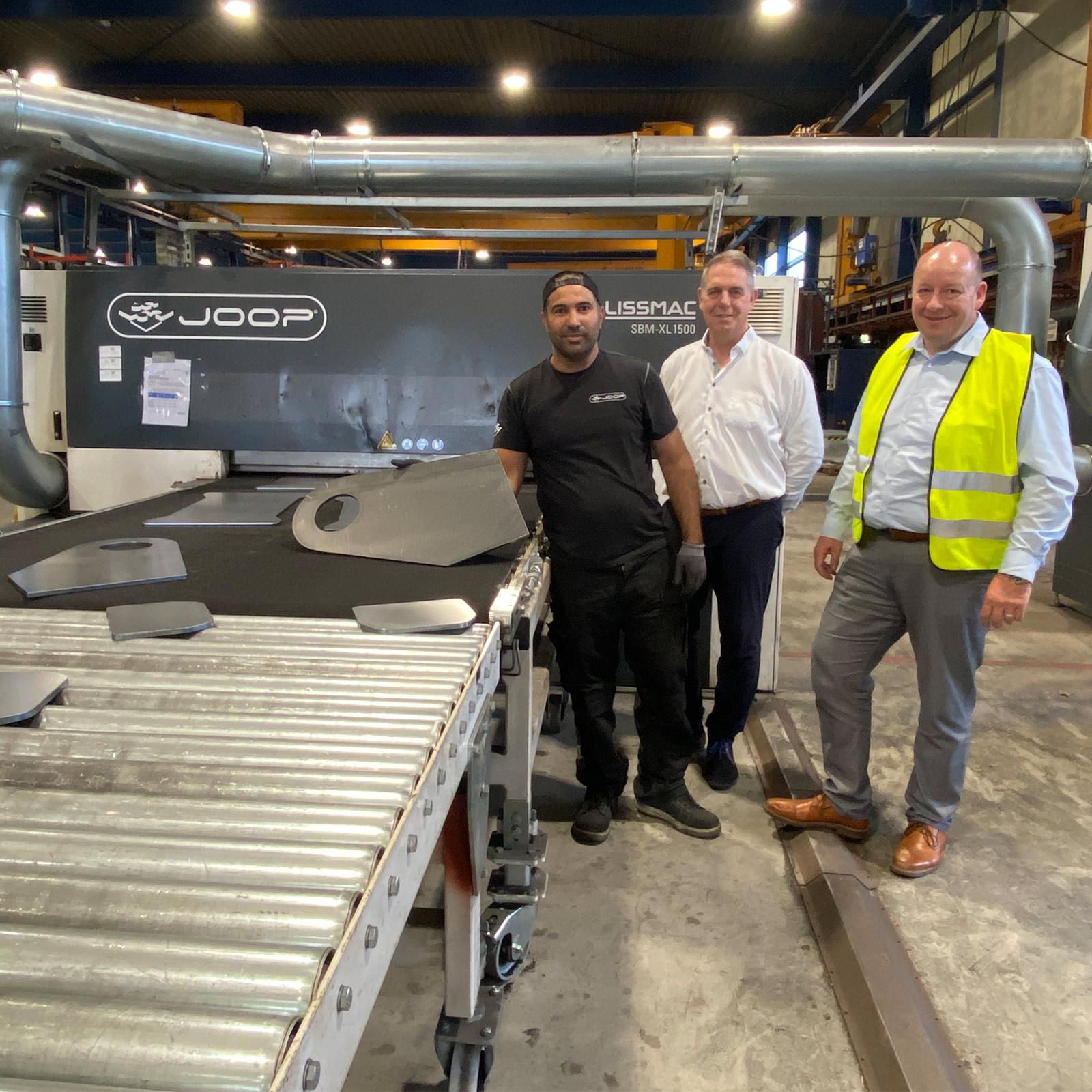
Il focus è interamente sull'automazione
It always takes visionaries and pioneers to establish something new on the market. A Dutch steel service centre is such a pioneer. Here, the processing of thick sheet metal is to be automated. Two new processing lines from Lissmac that have been purchased are an important building block for this solution.Text: Annedore Bose-MundeThe family-owned company Joop van Zanten has been a full service provider for plasma and oxy-fuel cutting of steel since 1966. The steel service centre in Veenendaal, Netherlands, now has over 40 employees and processes steel sheets ranging from 2mm to 300mm. It also offers drilling and tapping, folding, straightening, blasting and welding.Bart Kroesbergen has been plant manager at Joop van Zanten since 2018. He looks back: ‘Six years ago, there was still a lot of manual work at Joop van Zanten. But something had to change, especially in terms of competitiveness, the shortage of skilled workers and the future direction of the company.’ Two questions were on the table from the outset: ‘Can we automate to make work more attractive and more efficient? And above all, can we save costs?’ The steel processor's product range was already very broad in 2018. Therefore, another point was very important: flexibility.‘The company should be set up for the next 20 years. Increasingly, component manufacturing is being carried out for end producers. To this end, many technologies have been brought in-house, such as welding, machining and edging. We are trying to implement the processes in such a way that they are as automated as possible. This should ensure predictability for new products and product reproducibility, as well as consistent quality and, of course, competitiveness in Europe,’ says Managing Director Kroesbergen, defining the path and goal.Since 2018, the family-owned company, together with an external director, has implemented a new strategy for the company. At the same time, the next generation of the family are also being prepared for a management position. Together with Bart Kroesbergen, who has an extensive background in business administration, their combined experience, knowledge and shared desire for change has already achieved a great deal. Joop van Zanten is already one of the most modern steel processing companies in the Netherlands, characterised by its high level of automation and digitalisation, and consistently driving forward the topic of Industry 4.0.Investment in two efficient, identical systems Joop van Zanten's customer base has changed in recent years. Initially, the company mainly operated as a mass steel cutting company. It was about kilograms and heavy steel. The customers came, for example, from the bridge or shipbuilding industry. But the company wanted to and needed to become more flexible and expand its range of services – including with regard to material thicknesses. Now, the range of processed material thicknesses is in the range of 2mm to 300mm. Currently, the smallest product is a few centimetres in size, while the largest is almost 14 metres. A total of 90,000 different parts were produced in 2023. Today, customers are mostly from industry, mechanical engineering and the transport sector. The focus of production is on supplying customers with a complete end product that has been efficiently manufactured. The processes are to be automated to such an extent that a high level of economic efficiency is achieved. To achieve these goals, the Dutch company invested in two identical Lissmac systems, each consisting of an SBM-M 1500 D2 slag removal machine, an SBM-XL 1500 G2S2 grinding and deburring machine (passage width of both systems is 1,500 mm), as well as extraction and conveyor technology. The first system was purchased in 2019, the second in 2021. ‘We visited several manufacturers, spoke with system representatives and also looked around at the major trade fairs,’ says Plant Manager Kroesbergen, looking back. But one point ultimately convinced the decision-makers at Joop van Zanten: the two-sided processing that the Lissmac systems make possible. ‘We sometimes run products that are 20 metres long through the systems. The Lissmac technology makes this possible in just a single process step, which makes our work much easier,’ says Kroesbergen. The otherwise necessary handling and the associated complex logistics in the halls are no longer required. Extensive tests were carried out before the decision was made in favour of the Lissmac Maschinenbau GmbH system. This was also necessary due to the high variety of parts. The practical tests were carried out with the products and materials in mind. Fine adjustments were made and the system went into operation in 2019. ‘We decided that all the parts we manufacture would pass through the Lissmac system. Of course, the surface quality and feel are now better. But every single part also looks really good,’ says Bart Kroesbergen. Based on the technical requirements alone, this would only be necessary for about 50 percent of all parts. But in the meantime, the deburred and rounded parts have also become a quality feature for Joop van Zanten that customers appreciate. And then there is the plant manager's always forward-looking view of fully automated processes. ‘If you have a second processing stream in a process that is not to be automated, it is more difficult to automate it completely.’ The second system, located in a different production area, was purchased in 2021. The production volume had increased significantly, and certain production ranges needed to be processed efficiently for logistical reasons. However, this identical system was also purchased with a view to the planned significant expansion of the automation. The goal is automation in the thick sheet metal sector One of the two Lissmac lines will already be used in automated production. Steel sheets up to 40mm thick will be processed here. The second system will be used to process sheets up to 100mm thick. Automation is planned here as well. ‘The requirement that the systems be prepared for future automation was specified by Joop van Zanten at the start of the project for the first system,’ recalls Robert Dimmler, Sales Director Metal Processing at Lissmac. This is also a very important point in terms of ensuring smooth interface communication between different applications and systems. A system consisting of a slag removal machine, a grinding and deburring machine, and extraction and conveyor technology is one of the machine manufacturer's standard applications. ‘But Joop van Zanten's vision of the automation that was considered from the outset was truly visionary. Automation in the thick sheet metal sector was still uncommon at that time,’ says Dimmler. ’Automation is usually known from the thin sheet metal sector. This was now to be transformed into the thick sheet metal sector, where completely different workpiece dimensions and part weights are common. Being involved in finding a solution here is an exciting part and definitely also a challenge.’ ‘Our dream was to use a fully automated factory for thick sheet metal processing within ten years. The question was not ‘will we be able to implement this?’ but rather ‘how will we be able to implement this in concrete terms?’ says Bart Kroesbergen. To this end, experience from other industries was also incorporated into the considerations, for example from concrete construction, where very high unit weights are also involved. This optimistic thinking outside the box also convinced machine builder Lissmac. ‘A system manufacturer also continues to develop based on customer requirements. And when you have a visionary customer like Joop van Zanten, it also triggers us,’ adds Robert Dimmler. When it comes to new implementation ideas, it's simply part of the process to think outside the box. The challenge lies in the weight and variety of the parts The weight, variety and complexity of the structures require new approaches to implementation with regard to automation. The mechanical removal of parts using robotics is therefore not yet fully implemented. Here, Joop van Zanten is working together with Messer Cutting Systems GmbH, Beuting Metalltechnik GmbH & Co. KG and Lissmac on a suitable solution. The goal that the partners involved are working on is a solution that will cover the company's range of thick sheet metal core parts. The systems are to run automatically next year.The fact that all systems in operation at the Dutch steel service centre are connected to a software platform and OPC UA interfaces is another important point for seamless automation. Machine manufacturer Lissmac has also defined the OPC UA standard (standard for secure, cross-vendor networking for industrial systems) as the standard for its own products. One example shows how important this topic is: a customer of Joop van Zanten manufactures the frame of a system that produces chips. The steel plates required for this, which are manufactured by the steel service centre, must not be touched by hand so that finger grease does not get onto the systems. Without automation, this would be inconceivable. One thing is certain: the project partners are working together on a truly visionary task. However, solving this task involves very pragmatic issues: technical implementation, constant communication, and continuous learning and support from each other.
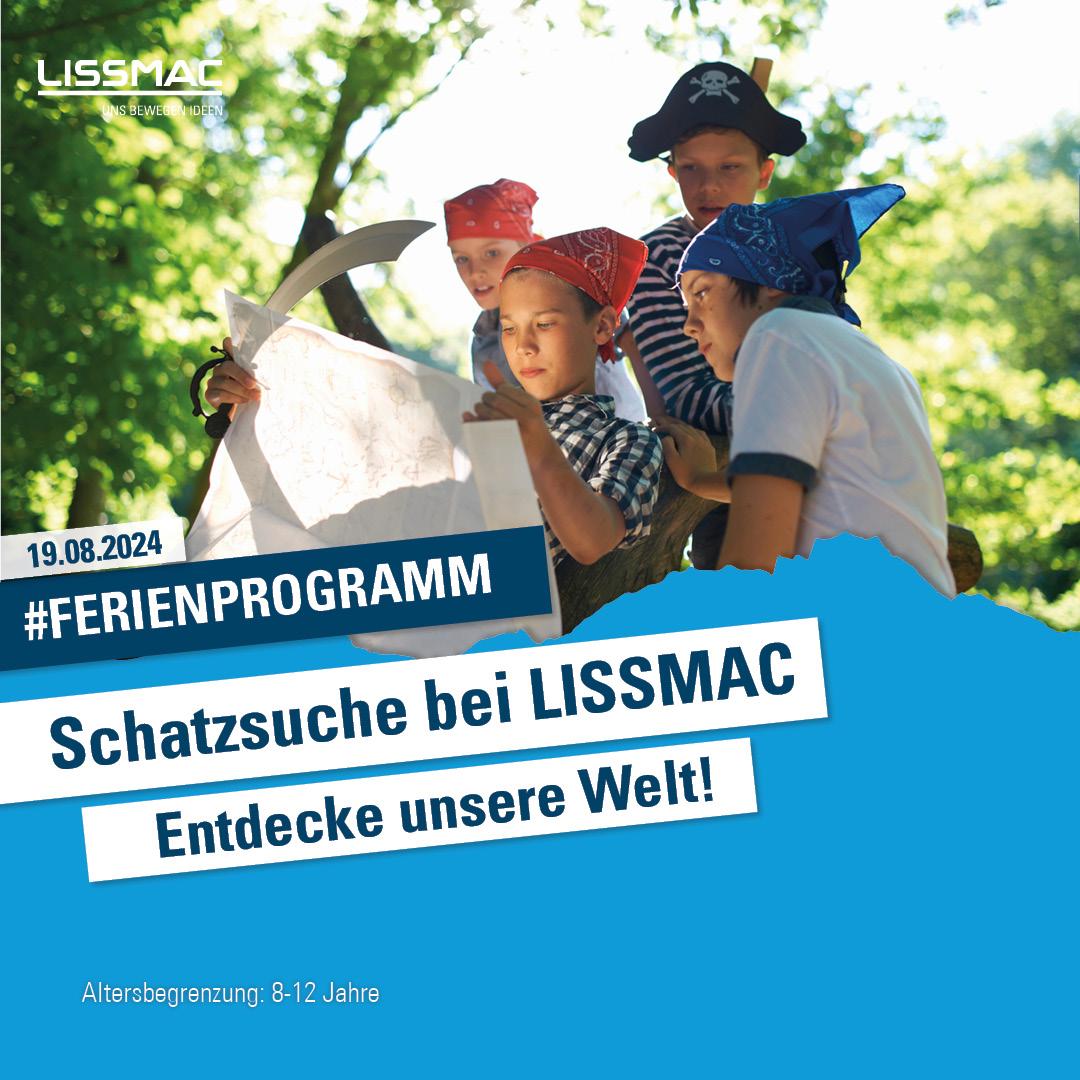
Hast Du Lust Dich auf die Suche nach dem Schatz bei LISSMAC zu machen?
Termin: 19.08.2024 Max. 15 Teilnehmer Altersbegrenzung: 8-12 Jahre Bei der Schatzsuche wirst Du LISSMAC und die Produkte, sowie den Ablauf vom Blech bis zur Maschine kennenlernen. Zudem erwarten Dich spannende Projekte, die unsere Azubis gebaut haben. Eines dieser Projekte war ein Tischkicker. Am Ende unserer Schatzsuche erwarten Dich tolle Geschenke und Informationen zum Schnupperpraktikum, Ausbildungsstellen,…. Für Essen und Trinken ist ausreichend gesorgt! Alle Informationen & die Möglichkeit zur Anmeldung hier Anmeldung möglich per Telefon, E-Mail oder Einwurf der Anmeldekarte bei der Stadt Bad Wurzach. Zum Programmheft (LISSMAC S.29)
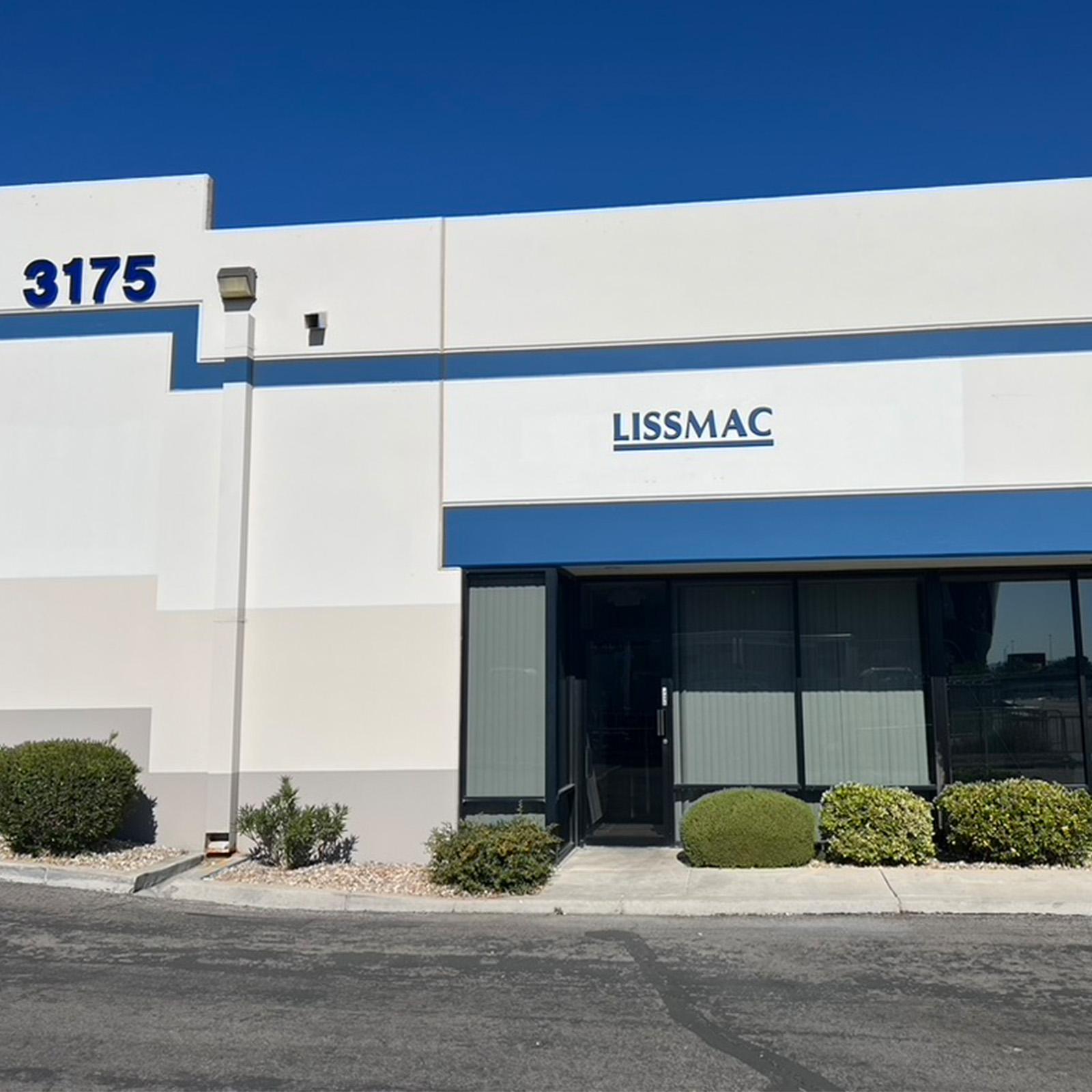
LISSMAC Corporation apre una nuova filiale a Las Vegas
Il 1° gennaio 2024, LISSMAC Corporation ha ufficialmente aperto una nuova filiale a Las Vegas, Nevada. Inizialmente, l'ufficio di Las Vegas servirà come sede di vendita e assistenza per la costa meridionale e occidentale degli Stati Uniti. "Il nuovo ufficio di Las Vegas è un passo importante per espandere le nostre attività di vendita e assistenza nel sud-ovest", afferma Ingo Heiland, vicepresidente di LISSMAC Corporation. "Las Vegas è un'importante sede fieristica per noi, con World of Concrete, un'importante fiera annuale per il calcestruzzo e la muratura, nonché la ricorrente fiera di settore FABTECH. Inoltre, il Nevada è convenientemente situato nel sud-ovest e ha un forte settore manifatturiero e delle costruzioni". LISSMAC Corporation è stata fondata nel 2007 a Mechanicville, nello Stato di New York, e da allora serve il mercato statunitense con soluzioni innovative e affidabili nelle divisioni Construction Technology e Metal Processing. Con 25 dipendenti, uno showroom per le dimostrazioni dal vivo, un team di assistenza e un proprio magazzino di ricambi e merci, la sede di Mechanicville è perfettamente attrezzata per supportare i clienti dalla consulenza applicativa al post-vendita. "Nel corso del prossimo anno amplieremo l'ufficio di Las Vegas e assumeremo altri dipendenti per raggiungere lo stesso livello di assistenza ai clienti di New York", spiega Ingo Heiland. "L'obiettivo è quello di effettuare dimostrazioni dei prodotti della divisione Metal Processing sia presso i clienti di riferimento di lunga data nelle vicinanze che, a medio termine, presso la nostra sede. Inoltre, numerosi progetti edilizi regionali ci permetteranno di dimostrare i nostri prodotti per l'ingegneria civile", aggiunge Norbert Zell, Branch Manager di Las Vegas. Il nuovo ufficio si trova a cinque miglia dall'aeroporto e di fronte allo stadio Allegiant, sede del Super Bowl LVIII nel febbraio 2024.Dal 1° gennaio 2024, LISSMAC Corporation avrà una filiale satellite che servirà il sud-ovest e la costa occidentale degli Stati Uniti dalla nuova sede: LISSMAC Corporation Satellite Branch 3175 W Ali Baba Ln Suite 806 Las Vegas, NV 89118 USA
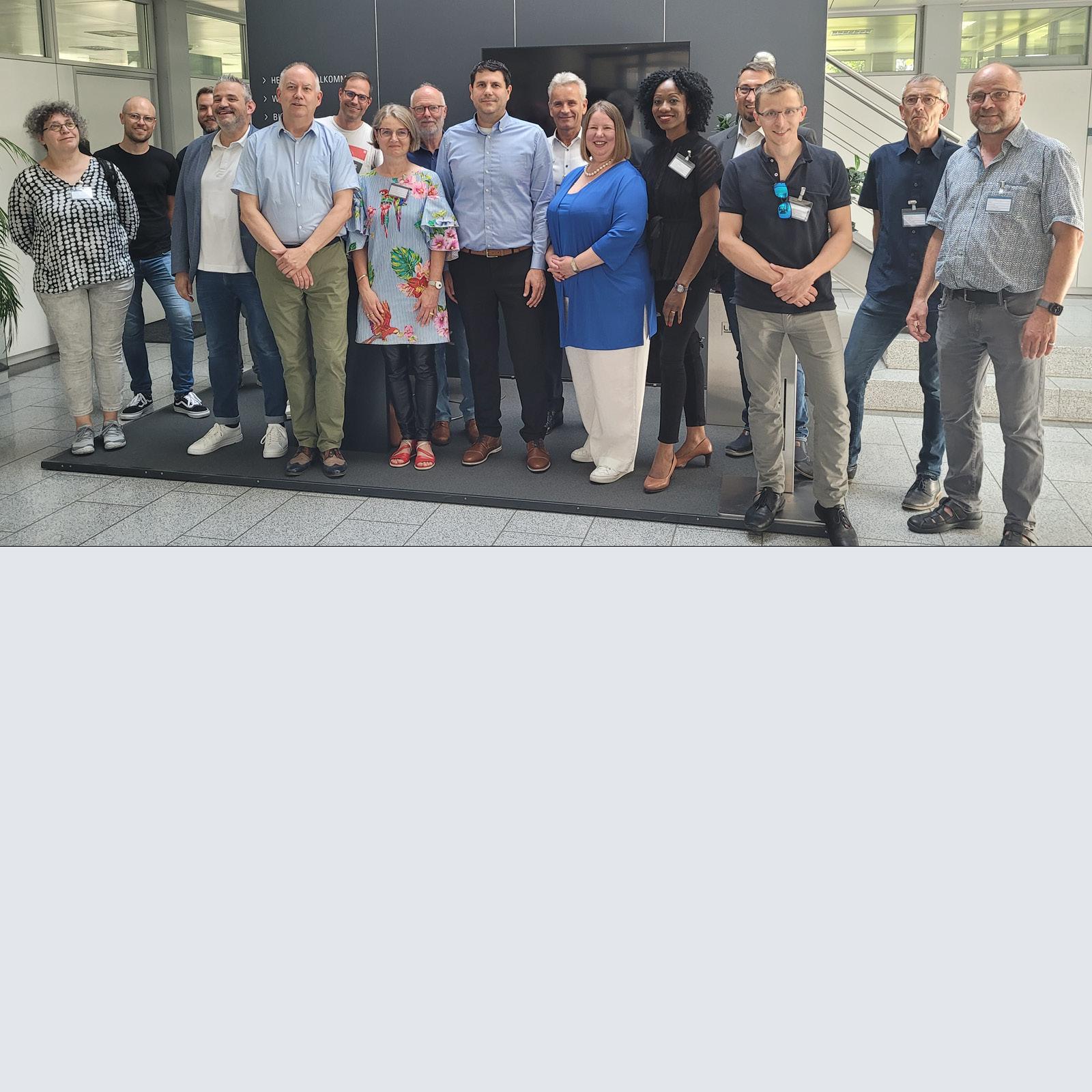
Factory tour HGV Bad Wurzach
On 26.06.2024, we hosted a group of visitors from the Bad Wurzach Trade and Commerce Association. The HGV is an association of traders in Bad Wurzach. The interested guests, mainly managing directors of companies in Wurzach, took the opportunity to visit our company. After the reception and welcome by the management, the guests were divided into two groups and guided through the production halls by Daniel Keller and Hinrich Dohrmann. The visitors were also shown the new hall and explained the digitization and automation of our work processes, but the current difficult economic environment was also discussed, but always with an optimistic view to the future. After the one-hour tour, there was an opportunity for questions and informal discussions over a snack.
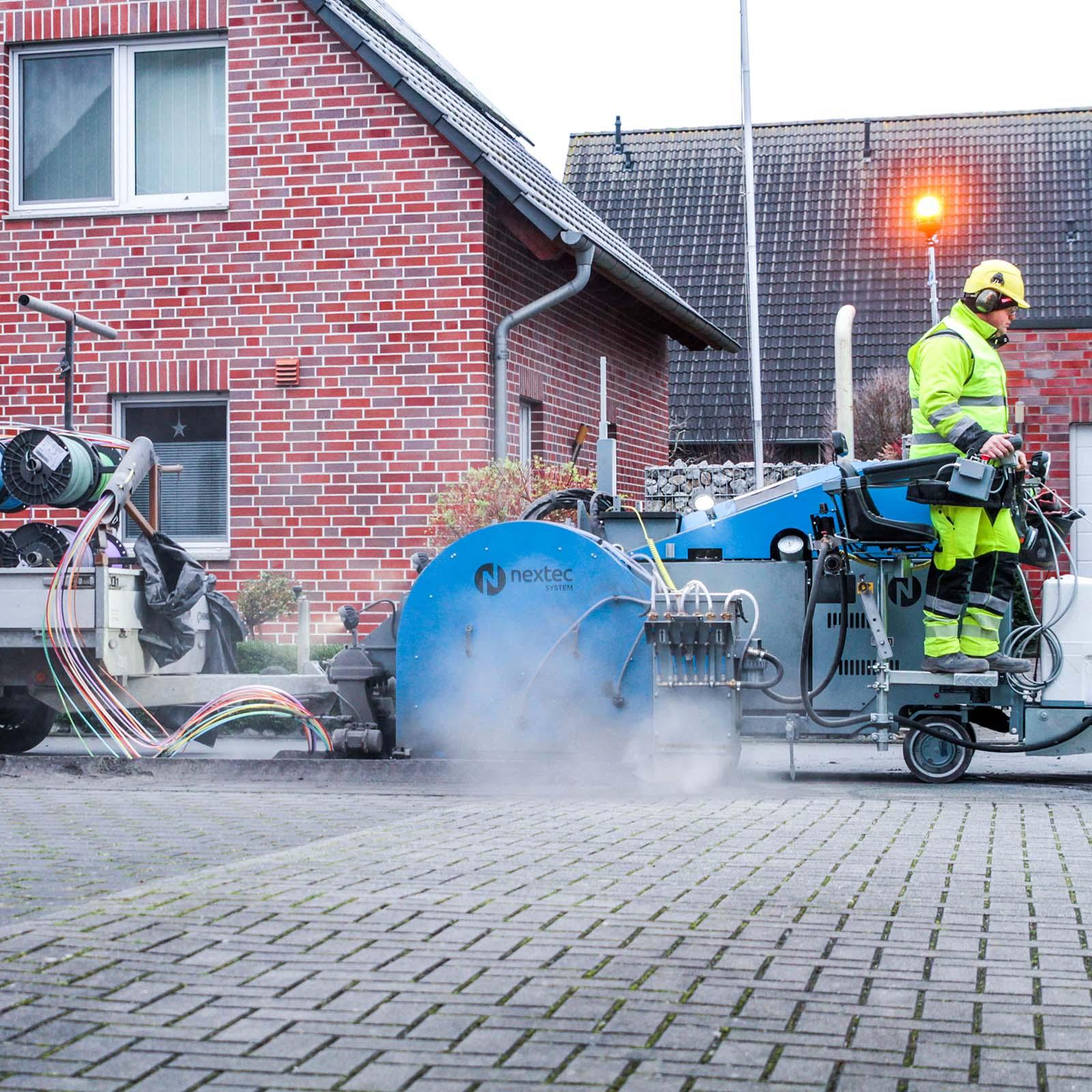
DIN 18220: A MILESTONE FOR FIBER OPTIC EXPANSION
DIN 18220 COMES INTO FORCEOn 28.07.2023, "DIN 18220:2023-08. Trenching, milling and ploughing methods for laying empty conduit infrastructures and fiber optic cables for telecommunications networks" was adopted. The document was ceremoniously handed over at an event on the gigabit strategy of the Federal Ministry for Digital and Transport (BMDV). According to Section 126 of the German Telecommunications Act (TKG), it is to be applied uniformly by all parties involved as a recognized technical rule from the time of publication. DIN 18220 is intended to contribute to the cost-effective acceleration and, above all, high-quality implementation of fiber optic expansion. It defines clear conditions for use and implementation and sets the legal framework for achieving a milestone in broadband and fiber optic expansion. DIN 18220 increases investment security for all parties involved, especially for telecommunications companies. To date, there have been neither standardized framework conditions nor uniform principles for the application of the trenching method. Up to now, most municipalities have mainly chosen the open construction method as the laying method for fiber optic expansion, as the minimum overlap had to be at least 60 cm before the standard. Since 2012, the TKG has permitted the use of shallow laying (trenching, shallow laying methods), which also includes non-standardized methods such as trenching. However, the process has so far had difficulty establishing itself on the market. This is primarily due to legal uncertainties for all parties involved. These are inevitably associated with the lack of binding technical specifications, in the form of a binding standard, for the use of such alternative laying methods. The difficulty lay in particular in differences between road construction authorities, contractors and telecommunications companies regarding the specific execution and implementation. As a result, there were delays in the expansion of the fiber optic infrastructure. THIS CHANGES WITH THE NEW DIN 18220Up to now, most local authorities have mainly chosen the open construction method as the laying method for fiber optic expansion, as the minimum cover had to be at least 60 cm before the standard was introduced. DIN 18220 now regulates laying methods for reduced construction depths, including diamond trenching from LISSMAC (38 cm laying depth)."With DIN 18220, fiber optic installation will not only be easier in the future, but also of higher quality, faster, more cost-effective and more resource-efficient. DIN 18220 creates the necessary legal certainty and investment security for all parties involved," said BMDV State Secretary Stefan Schnorr, describing the importance of the new standard. WHAT DIN 18220 MEANS FOR LISSMACLISSMAC has been active in diamond trenching for around 10 years. Due to our experience in the field of joint cutting, we are a long-standing member of the VDMA (German Engineering Federation) and were involved in the creation of the standard as a member of the standardization committee. We are very pleased about the recognition of the alternative laying methods for fiber optic expansion, including LISSMAC diamond trenching, as the standard creates clarity for the construction industry, all municipalities, communities and telecommunications companies. Find out more about diamond trenching following DIN 18220 with LISSMAC. Read further background information to DIN 18220 (german). Watch the full video "Glasfaser ohne Einblasen" together with Telekom (with english subtitles).
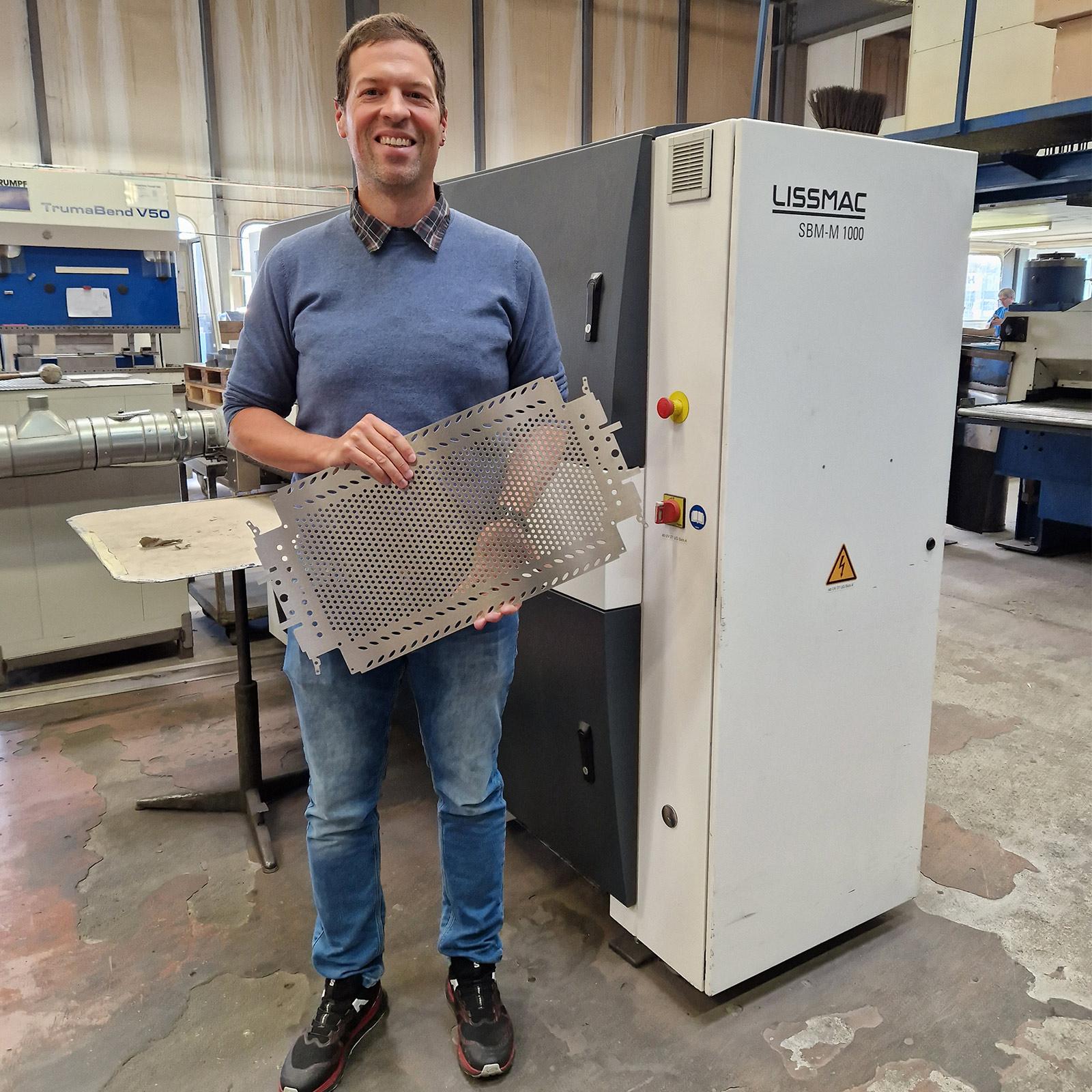
Sicurezza di processo grazie a due nuovi sistemi di levigatura e sbavatura
Un'azienda svizzera attiva nel settore della lavorazione della lamiera ha investito in due impianti di levigatura e sbavatura. Vengono utilizzati per la rimozione di bave secondarie e per ottimizzare la finitura superficiale. L’acquisto dei due impianti sostitutivi aveva come obiettivo la flessibilità, una maggiore efficienza e affidabilità del servizio.Testo: Annedore Bose-MundeL’azienda Ulrich Oppliger AG di Lyssach, Svizzera, opera con successo nel mercato da 54 anni. L'azienda è attiva principalmente nell’ambito della lavorazione della lamiera, - a partire dalla piegatura, punzonatura e taglio laser fino alla saldatura, raddrizzatura e sbavatura. Vengono prodotti prototipi, singoli articoli o serie. Marc Burkhalter lavora nell’azienda da nove anni. È stato prima direttore dell’azienda per due anni. In seguito ha rilevato l'attività dal suocero, proprietario dell'azienda, e ora è amministratore delegato da sette anni. Sa quanto sia importante la qualità dei pezzi. L'azienda ha ora investito in due nuovi impianti Lissmac per garantire la qualità in modo affidabile e per essere in grado di produrre in modo più efficiente in futuro. Lo stimolo per uno degli investimenti è stato un componente per un cliente la cui produzione presentava continui problemi tecnici. Per un'azienda che sviluppa e vende strumenti chirurgici, Oppliger produce da diversi anni componenti per vassoi di sterilizzazione, che vengono poi utilizzati nella sala preoperatoria per preparare gli strumenti chirurgici della sala operatoria. I pezzi punzonati, che vengono ulteriormente lavorati dal cliente, ricevono una finitura superficiale personalizzata presso l’azienda Oppliger mediante successiva levigatura. E proprio qui sorgeva il problema: la bava secondaria. Inoltre, il cliente ordinava quantità sempre maggiori.L’assistenza è un criterio decisionale importanteLa bava secondaria doveva spesso essere eliminata a mano. Il vecchio impianto era inoltre spesso sovraccarico. Il limite è stato raggiunto nel 2018. “La ripetuta insoddisfazione per la qualità dei componenti e la lunga rielaborazione manuale dei componenti non soddisfacevano né il cliente né noi. Dopo tutto, una finitura superficiale precisa e un'ulteriore lavorazione puntuale sono essenziali per i prodotti di tecnologia medica. Dovevamo agire”, afferma Marc Burkhalter ripensando al passato. Era quindi necessaria una soluzione affidabile. I requisiti di qualità sono stati definiti insieme al cliente prima della nuova acquisizione. In azienda è stato inoltre analizzato il grado di redditività dell’investimento nel lungo periodo.È stata indicata l'applicazione specifica per la tecnologia dell'impianto da acquistare e quindi sono stati rapidamente messi a punto i dati chiave per la nuova macchina: doveva essere un sistema compatto, perché lo spazio disponibile nel capannone era limitato. Marc Burkhalter cita poi un ulteriore punto importante ai fini della decisione: “Per me era importante avere un interlocutore per l’area della levigatura. Anche su questo punto volevo collaborare con il nostro partner di assistenza di lunga data, Wolfgang Kohler. Con lui la comunicazione è fluida, il servizio funziona ed è garantito un rapido approvvigionamento dei pezzi di ricambio.” La WKS GmbH – Wolfgang Kohler Service GmbH con sede a Bad-Zurzach in Svizzera – è una società di vendita e servizi specializzata in macchine per la raddrizzatura e la sbavatura. La gamma comprende anche i sistemi Lissmac.Macchina universale di livello base per l'eliminazione delle baveIl processo decisionale si è svolto rapidamente. Sono state definite la gamma di pezzi e le condizioni relative allo spazio. Così, nel 2020 l'azienda svizzera di lavorazione della lamiera ha deciso di adottare l’impianto di levigatura a secco SBM-M 1000 S2 della Lissmac. La macchina per la levigatura e la sbavatura è una macchina di livello base universale per la rimozione di bave da taglio in parti tagliate al laser e punzonate. Le parti in lamiera ricevono inoltre una finitura superficiale ottimale. Bertrand Laroche è Area Sales Manager Metal Processing presso Lissmac Maschinenbau GmbH. Ha seguito questo processo. "La SBM-M 1000 S2 è una macchina funzionale in termini di design e funzionamento. Il sistema si adattava perfettamente all'applicazione presso la Oppliger", afferma. Grazie ai due nastri contro-rotanti e alla lavorazione su due lati, i pezzi non devono essere restituiti. Inoltre, è necessario uno spazio minore. Il tipo di macchina è stato quindi deciso rapidamente. Dopo una visita al centro dimostrativo di Lissmac a Bad Wurzach, sono stati adattati solo il design dell'impianto e il sistema di aspirazione ed è stata specificata la grana abrasiva. La macchina per la levigatura e la sbavatura è stata quindi acquistata e installata nel 2020. “I nostri clienti sono soddisfatti. Da quando è in uso il nuovo sistema, non ci sono più stati problemi con la bava secondaria. Anche la qualità della superficie è leggermente migliorata grazie alla grana abrasiva fine”, afferma soddisfatto Marc Burkhalter. Inizialmente, il nuovo sistema è stato utilizzato esclusivamente per produrre pezzi per un produttore di strumenti medici. Viene utilizzato anche per altre applicazioni, soprattutto per i pezzi che devono essere lavorati su entrambi i lati. Si tratta principalmente di pezzi industriali realizzati con sottili lastre di acciaio inossidabile. L'SBM-M 1000 S2 esegue principalmente la rimozione di spigoli vivi da parti sottili in acciaio inossidabile, e tutto ciò a basso costo - e con un basso consumo energetico. “Questa è stata la prima applicazione di Lissmac presso l'azienda di Lyssach. È bello essere stati in grado di collocare qui questo concetto di impianto, che è stato provato e testato sul mercato per molto tempo”, afferma il direttore commerciale di zona Bertrand Laroche.Il nastro Powergrip garantisce efficienza e flessibilità Un anno dopo, si è resa necessaria un'altra sostituzione. Il sistema precedente era inaffidabile, presentava un elevato rischio di guasti e il reperimento dei pezzi di ricambio era difficile. Inoltre, i pezzi più piccoli dovevano essere sbavati a nastro. Oppliger si è guardato in giro alle consuete fiere di settore. Sapendo che anche Lissmac produce sistemi in questo segmento, l'azienda svizzera si è rivolta proprio al costruttore di macchine di Bad Wurzach. I dati chiave del nuovo impianto erano chiari: lavorazione della più ampia gamma possibile di pezzi in acciaio inossidabile, ovvero un alto grado di flessibilità. E ancora una volta, il sistema doveva essere più compatto possibile. Oltre ad avere le funzionalità richieste, il rapporto qualità-prezzo doveva essere adeguato e i tempi di consegna accettabili. Inoltre, la Wolfgang Kohler Service GmbH doveva ancora una volta fungere da partner. La scelta di Marc Burkhalter è ricaduta sulla sbavatrice SMD 123 RE. Anche in questo caso, l’elemento tecnico di rilievo dell’impianto è il nastro Powergrip sul quale vengono deposti i pezzi durante la lavorazione, trattenuti dall’elevata forza adesiva, senza magneti o vuoto. “Siamo gli unici del settore a lavorare con un nastro trasportatore di questo genere. In altre parole: rispetto ad altre tecnologie conosciute, è necessario un maggiore sforzo di consulenza nei confronti del cliente”, afferma Bertrand Laroche. Tuttavia, il nastro Powergrip non è solo flessibile, bensì anche molto efficiente sotto il profilo dell’energia. Il sistema a vuoto, ad esempio, continua Laroche, è rumoroso, richiede molta energia e non è adatto a tutte le geometrie dei pezzi. Marc Burkhalter è soddisfatto della parte tecnica, che, una volta installata, funziona in modo affidabile. Nel nuovo impianto vengono prodotti pezzi più piccoli per un'ampia gamma di settori industriali, nonché pezzi per i quali l'aspetto visivo gioca un ruolo importante ed è fondamentale una buona finitura superficiale. Efficienza e stabilità per il futuroOppliger, una tra le prime aziende nella lavorazione al laser in Svizzera, produce pezzi per clienti industriali dei settori più diversi. Attualmente vengono lavorate ben 600 tonnellate di lamiera, di cui circa il 50% in acciaio e il 50% in acciaio inossidabile. Pensando al futuro, l’amministratore delegato Burkhalter afferma: “Sarebbe bene mantenere i livelli attuali. Contiamo su una crescita sana, su macchinari personalizzati, sull'automazione e sull'esperienza per servire un'ampia gamma di clienti. Sono importanti anche processi snelli: l’efficienza deve essere aumentata in tutti i settori, sia in ufficio che nella produzione”. Anche il direttore commerciale di zona Laroche guarda avanti: “In futuro vorremmo supportare i nostri clienti con mezzi abrasivi più efficienti. Su questo, Lissmac collaborerà con i produttori del settore. In questo modo la prestazione della macchina dovrà essere migliorata e ottimizzata, aumentando quindi la qualità e la resa. E nell'ottica di una tecnologia di sistema adeguata, anche i temi della manutenzione a distanza e della digitalizzazione vengono sempre più implementati”. Contatto: Ulrich Oppliger AGMarc BurkhalterIndustriestrasse 23421 Lyssach, Schweizwww.uoppligerag.ch *** Lissmac Maschinenbau GmbHBertrand LarocheLanzstraße 488410 Bad Wurzachwww.lissmac.com Autore dei testi:Annedore Bose-Mundetecnología y empresa en Erfurt www.bose-munde.de