Metal processing
Innovative equipment for metal processing
Construction Technology
Innovative construction technology for professionals
Working at LISSMAC
Innovation and diversity under one roof
LISSMAC – we are driven by ideas
We rely on experience and system competence. Against this background, LISSMAC Maschinenbau GmbH is comprised of four business divisions: Construction Technology, Metal Processing, Plant-Engineering and MT-Handling . Worldwide, more than 400 employees at five locations in Germany, France, the USA and the United Arab Emirates ensure the highest levels of customer satisfaction.
Four business areas
Corporate movie
News
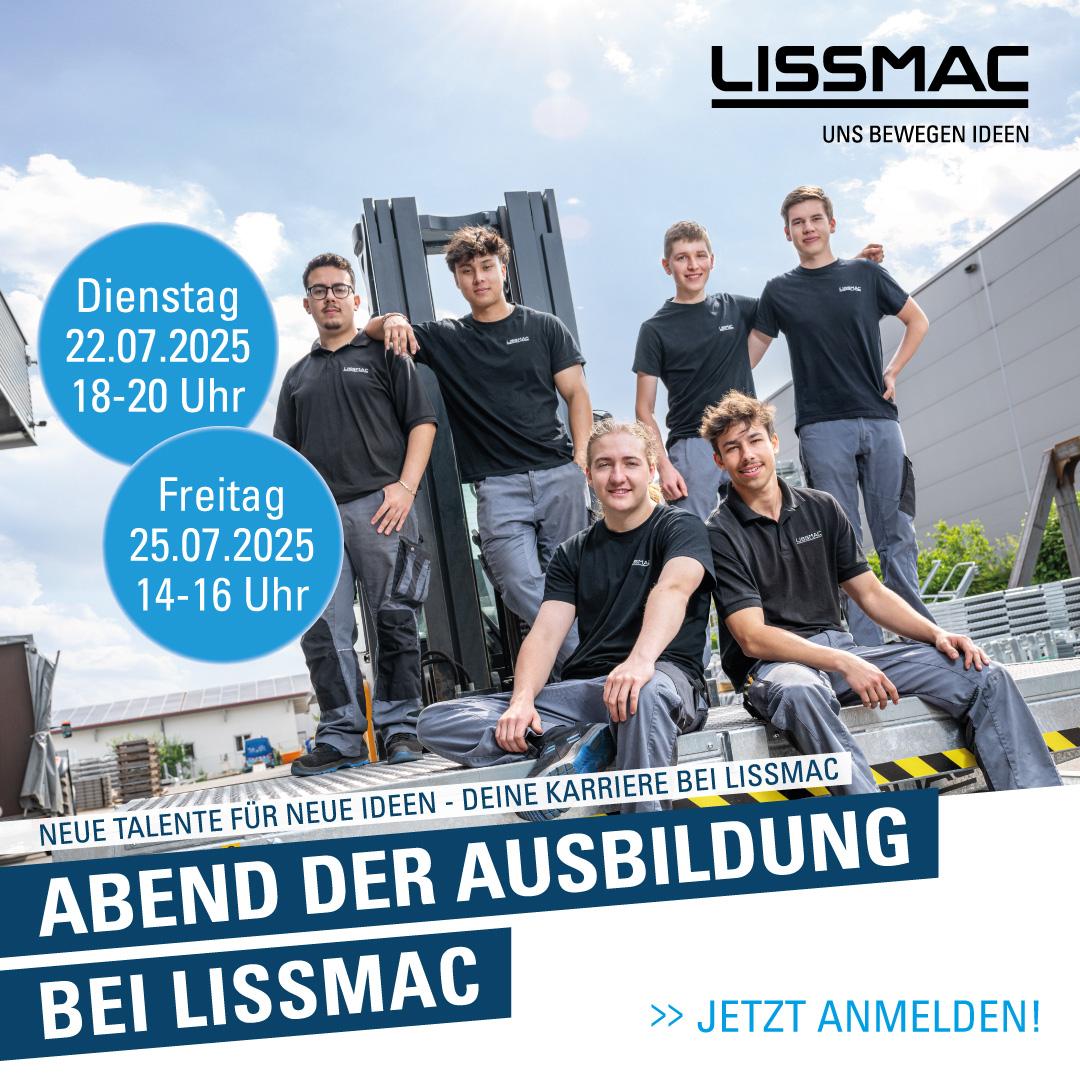
Training evening 2025
Become part of our team and visit us on the evening of training: Tuesday 22.07.2025 // 6-8 pmFriday 25.07.2025 // 2-4 pm Take a look behind the scenes Gain insights into the working environment Find out about our apprenticeships You can expect informative discussions with our trainees and training managers Parents are also very welcome Registration possible at short notice:to jobs@lissmac.com or by phone: 07564 307-202 or -228or PM via Instagram We are offering many exciting professions for the start of training in 2026.Here you can find information about the vacancies. We look forward to receiving numerous applications!
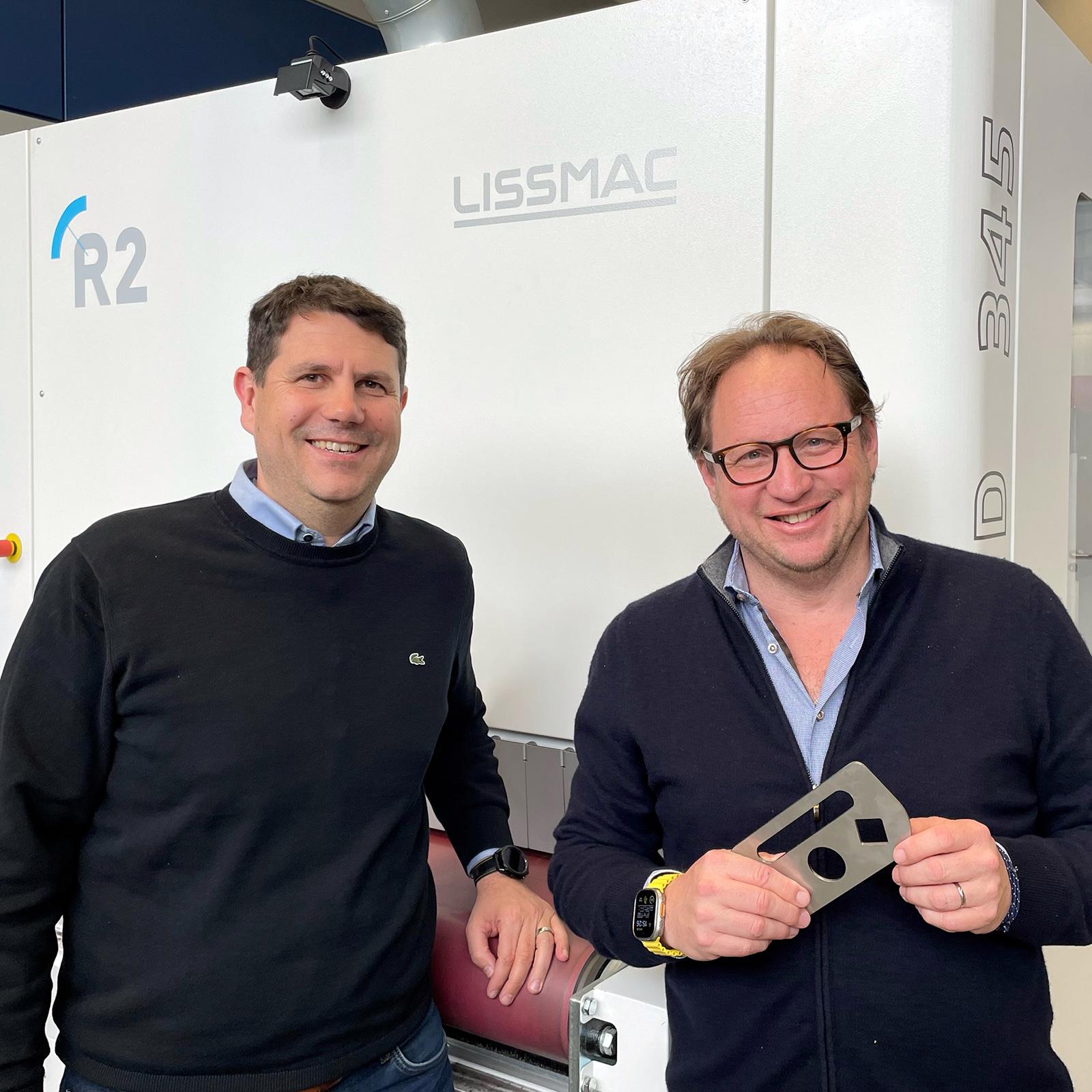
Upcoming change in management at LISSMAC
Upcoming change in management at LISSMAC Dear Ladies and Gentlemen, We would like to inform you about an important change in the management of LISSMAC Maschinenbau GmbH. Our long-standing employee and Managing Director Daniel Keller will be leaving the company on 13.04.2025. His successor, Mr. Thomas Hoffmeister, has already been in office since 01.02.2025 and will manage the company together with Dr. Hinrich Dohrmann. Daniel Keller:Last year, after careful consideration, I made the decision to reorient myself professionally after more than two and a half decades at LISSMAC and take up a position outside the company. This decision has not been easy for me, as LISSMAC has always been a matter close to my heart. I started my career at LISSMAC in 1998, which took me through various positions and departments, and I was appointed Managing Director at the beginning of 2022. In these more than two and a half decades, I have been able to contribute to the development of LISSMAC and help shape it in my various areas of responsibility. It was a very intense time that shaped my life and that I would never want to miss. We achieved a lot together. These successes are the result of joint efforts and the tireless commitment of all employees. I would like to thank all my colleagues, business partners and customers for their trusting cooperation and support. The experience and relationships that I was able to build up during my time at LISSMAC will continue to accompany me in the future. My name is Thomas Hoffmeister - I am the new Managing Director at LISSMAC Maschinenbau GmbH: At 53 years old, I bring not only experience but, above all, passion and an entrepreneurial spirit. Born in Germany and raised in Italy, Switzerland, and the USA, I learned early on that success stems from responsibility, consistency, and innovation – values that continue to drive me today. Coming from a family of entrepreneurs, I was taught from a young age the importance of entrepreneurial thinking, responsibility, and sustainable action. After studying Manufscturing Engineering at Boston University and earning an MBA from the London Business School, my career took me around the globe – from Thailand to Egypt to China. Positions at ABB and Dresdner Bank provided me with valuable insights before I founded my own company in 2016, which I have since sold. Now, I’m excited to drive LISSMAC forward with full energy together with an outstanding team. Our company is excellently positioned to not only meet the challenges of the future but to set new standards. With strong employees, a solid market position, and strategic investments in our site in Bad Wurzach, we have everything we need for enduring success. Let’s shape the future together!
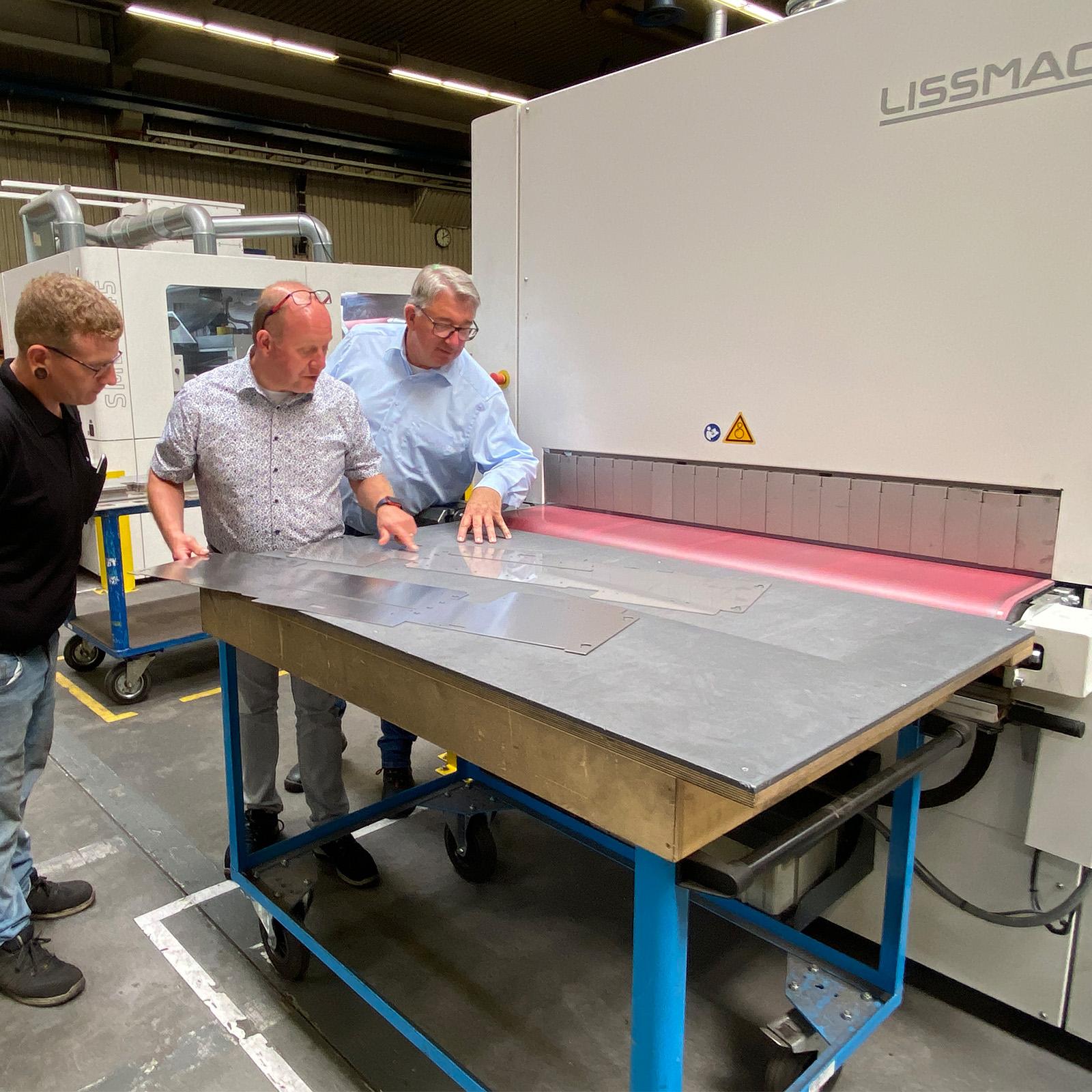
Burr-free sheet metal parts for pay stations and signaling technology components
Burr-free sheet metal parts for pay stations and signaling technology components Fiber lasers in particular require a powerful downstream deburring technique due to the burrs that occur during cutting. A global company from North Rhine-Westphalia has invested in this technology multiple times and, in doing so, has developed optimized production logistics and a continuous material flow. Text: Annedore Bose-Munde The production know-how that goes into the things we encounter every day is often not apparent at first glance, for example in parking or signaling solutions. The family-owned company Scheidt & Bachmann, based in North Rhine-Westphalia, manufactures pay stations and terminals worldwide, for example for parking garages or buses, as well as signaling technology components and barrier systems, for example for Deutsche Bahn. Founded in 1872, the company has grown from a machine manufacturer to a global system provider with a total of around 3,500 employees worldwide. Scheidt & Bachmann's prefabrication is based in Mönchengladbach, with assembly lines in Slovakia and the USA. 90 percent of Scheidt & Bachmann's production is stainless steel parts, as well as some aluminum and steel parts. In the sheet metal processing area in Mönchengladbach, 90 employees manufacture a broad portfolio of sheet metal products. The demands on the processing results and the processing technologies have increased continuously in recent years. Before 2006, laser cuts were placed on pallets after cutting, stacked and then removed individually. These were then sanded manually and with simple technology. This was quite laborious and required a great deal of manual effort and sometimes multiple passes. Throughput times, logistics and costs were less than ideal. The first Lissmac system was purchased in 2006 to address the issue of edge rounding: an SBM S 1000 for processing sheet metal and laser parts. Since then, rounding the inside and outside contours on both sides in a single operation has significantly increased process efficiency and saved time. What was still missing at that time was structured, customized production logistics. Fiber laser was supplemented with powerful deburring technology When the next step of modernization and investment in new plant technology was to be taken in 2019, several criteria were on the agenda: By purchasing a laser from the company Trumpf with fiber technology, the decision-makers at Scheidt & Bachmann relied on the technological advantages of the process. The purchase of the new cutting technology therefore also directly required modern and powerful deburring technology. And with a view to protecting employees, ergonomic improvements for the workers were also to be achieved. So, before purchasing the new system, two system manufacturers were contacted and reference parts were sent for sample processing. In the end, the decision was made in favor of an SBML 1500 from Lissmac, which is used for deburring and edge rounding on both sides. “This system performs double-sided processing in a single grinding pass. And the quality is so good that a single pass is actually enough to achieve a high-quality grinding result,” says Jörg Würker, Head of Mechanical Production and Head of Sheet Metal Processing at Scheidt & Bachmann GmbH. Time-consuming rework is no longer necessary. And he mentions another important aspect: occupational safety for technicians, which of course applies in the US. “If there is a sharp-edged item on an assembly line, the technician can be injured. And that can quickly lead to a legal problem,” says Würker. The fact that the technical parameters were also handed over with all the test parts was also very helpful, especially in the start-up phase with the new system. “We definitely benefited from that,” says Würker. Dirk Schürstedt, Area Sales Manager for Metal Processing at Lissmac Maschinenbau GmbH, who has been looking after Scheidt & Bachmann since 2019, also remembers the initial contact and a pragmatic and constructive decision-making process. He adds: “All sample processing at Lissmac is always documented precisely and comprehensively and made available to the customer. This includes which machine was used for the processing, which tool, which speeds, which rotational speeds, and so on.” This enables the customer to achieve good processing results right from the start. Over time and based on production experience, the system is then usually fine-tuned so that it can be better and better aligned with the processes. The workers initially had to get used to handling the new system technology, so targeted operator training in the user interface was carried out. All in all, Jörg Würker and Dirk Schürstedt agree that the project was implemented quickly and constructively. Today, the system is used to process sheets with thicknesses from 0.8 to 10 mm. The size of the respective sheet metal blanks ranges from the size of a cell phone to the size of a table. In 2023, the system was also retrofitted with a wet extraction system to enable aluminum to be processed and to ensure material separation. Creation of optimized production logistics When the SBM L 1500 was purchased in 2019, it became clear that the production logistics needed to be optimized. When two fully automated Trumpf fiber laser cutting machines with a connected Stopa storage system were purchased in 2021, the issue came up again and should now be thought through to the end. “When the employee removes the part from the laser system, they should also place it directly on the grinding machine. The continuous material flow was important to us and should be implemented,” says Würker. This was also to avoid manual work and long throughput times. Accordingly, two more systems were purchased in 2022 that could be used to implement this seamless process. “We rely on stable and functional relationships. That is why we chose Lissmac technology again – this time for two systems with rotary brushing technology that allow us to deburr and also round edges in an adjustable quality and depth,” says the sheet metal processing manager. “We purchased two SMD 345 S-Edition universal grinding and deburring machines. Both systems work in single-sided operation this time. However, they can be used to create a defined surface finish such as classic brush sanding. This enables greater flexibility and saves purchasing costs,” adds Lissmac specialist Schürstedt. With flexibility in mind, these two systems were also equipped with a wet extraction system. Technology support is important One thing is certain: Scheidt & Bachmann is very satisfied with the processing results of the Lissmac systems. “Since the new systems have been in use, we have been reliably achieving excellent deburring results,” says Jörg Würker. In addition, the company receives targeted technology support and reliable service. For Dirk Schürstedt, it is important to be able to respond to the customer's individual production conditions and requirements with precisely tailored technology. “It's satisfying to be able to support the customer's needs over the years. As the machine manufacturer, we are also constantly developing the systems further. Customer feedback is important for this,” he says. Currently, a major focus is on the operability of the systems. These should be as simple and self-explanatory as possible to use in order to make the operator's work easier.
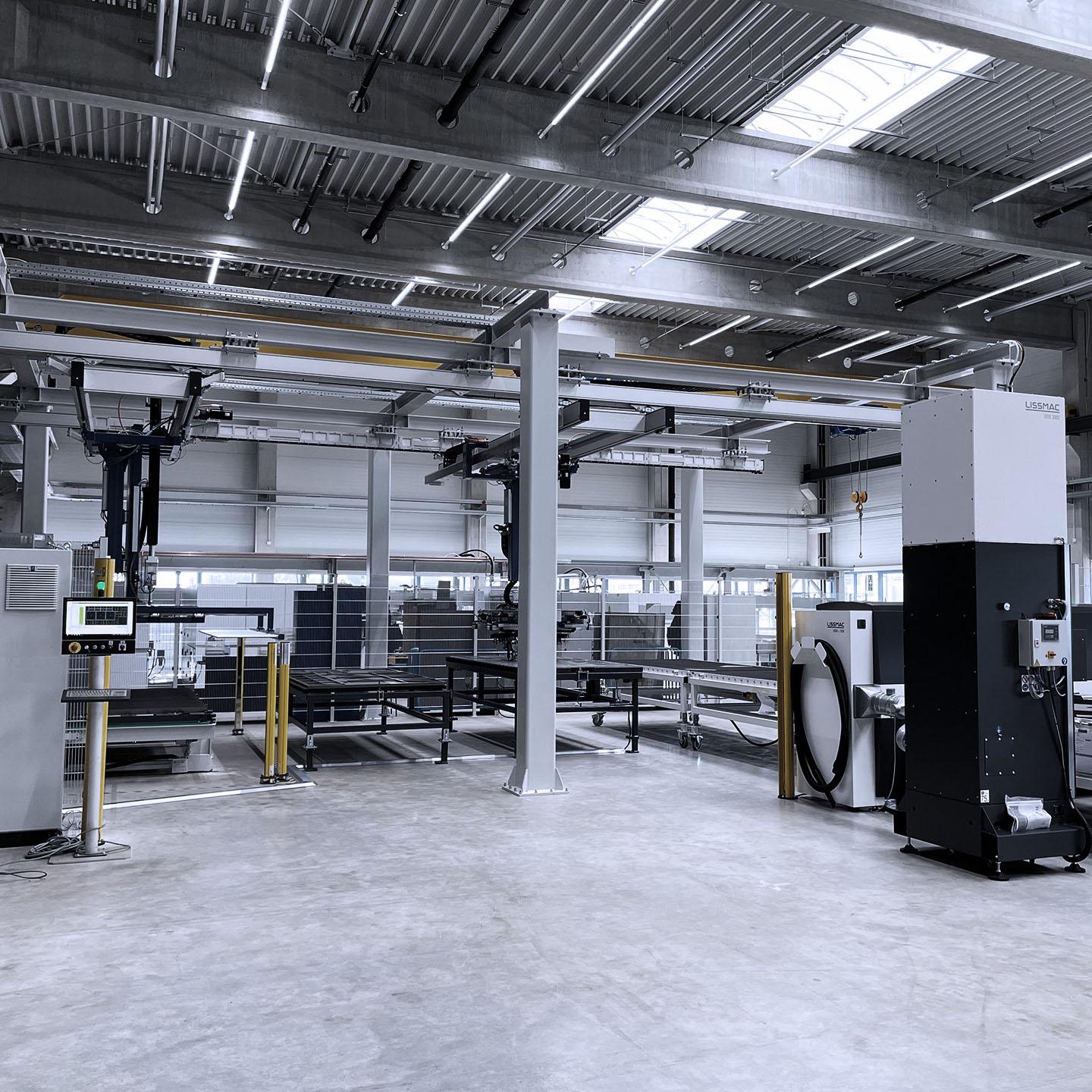
Lissmac automates grinding and deburring technology with partners
Automated processes ensure efficiency in sheet metal processing. Take, for example, the automated ejection unit that Lissmac Maschinenbau GmbH is presenting at Euroblech. It is used to separate laser components that are attached to micro bars on the sheet metal panel. Four separately controllable gripper units equipped with a vacuum suction cup selectively remove the laser components from the scrap grid after the micro-bars have been separated by the ejection process. The components are then placed on a conveyor belt for the next process steps - deburring and edge rounding. The system does not require optical image processing as it is based on the geometry data of the cutting plan and automatically determines the required number of suction pads. It can be flexibly adapted for different sheet sizes and thicknesses. The possible component sizes in the current system version range from DIN A5 to Euro pallet format. Sheets with thicknesses from 1 mm to 8 mm and a maximum weight of 90 kg can be processed. Time-consuming manual clearing is no longer necessary. The process is decoupled from laser cutting thanks to a buffer space in the warehouse. The ejection unit can be retrofitted to existing cutting systems or high racks and can be used regardless of the manufacturer. The automation unit, which the Bad Wurzach-based machine manufacturer developed together with J. Schmalz GmbH, automates the loading of Lissmac grinding machines. The cell relies on robotics technology as well as AI software and 3D vision sensors from the automation technology manufacturer. The components are identified with the help of visual 3D component recognition from Schmalz in order to pick up unmixed components from a pallet. They are then placed on a conveyor belt using a matrix gripper. They can then be deburred in the next process step.The combination of loading robots with the vacuum grippers from Schmalz and the connection to the sanding system ensures more efficient production processes: Manual loading is reduced so that a deburring machine can be operated by a single person. The SBM-L Evo series will also be presented as a pre-series model for the first time at Euroblech. On show will be the SBM-L 1000 G1S2 Evo - a deburring machine for deburring and edge rounding on both sides of punched, laser-cut and fine plasma-cut sheets in a single work step. The new top model of Lissmac's double-sided deburring machines has been available as a series machine since April 2024 From the Lissmac product range of single-sided and double-sided grinding and deburring machines for thin and thick sheet metal processing, the SBM-L 1500 G1S2 for highly efficient double-sided deburring and edge rounding of punched, laser or HD plasma-cut parts and the SMD 35 REER (S-Edition) for uniform edge rounding on all edges up to a radius of 2 mm as well as for a non-directional finish and small parts and thin sheet metal processing will also be on show in Hanover. The SMD 123 RE will also be presented, which can be used for deburring and uniform edge rounding on all edges as well as for surface processing of workpieces made of steel, stainless steel and aluminum. Also on show will be the SBM- XS 300 G1E1 Alu Mix for deburring and even edge rounding of small parts in a single operation. Visitors are cordially invited to the Lissmac stand, Hall 14, Stand 14-K06, to find out more about proven technologies and the new features for Industry 4.0.
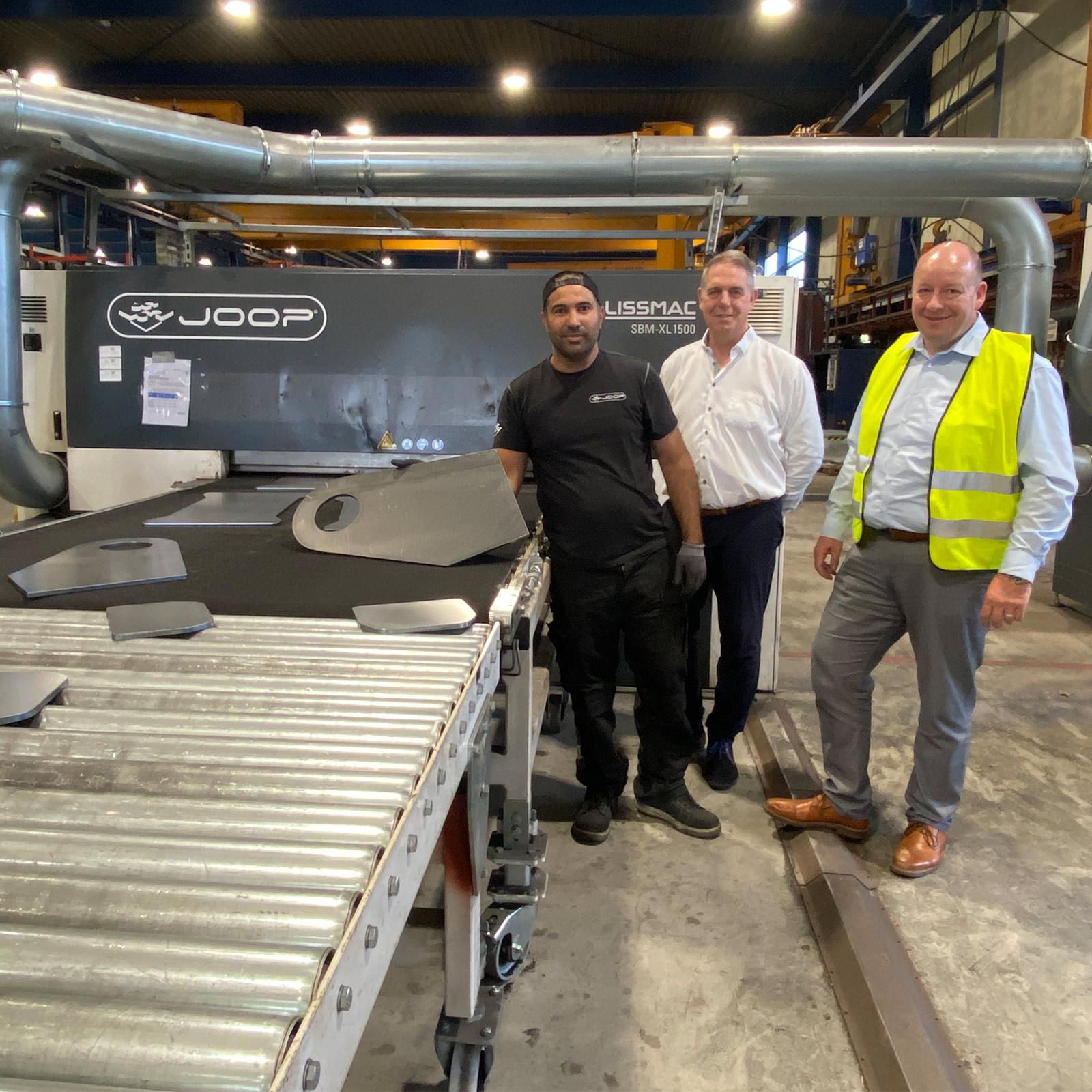
The focus is squarely on automation
It always takes visionaries and pioneers to establish something new on the market. A Dutch steel service centre is such a pioneer. Here, the processing of thick sheet metal is to be automated. Two new processing lines from Lissmac that have been purchased are an important building block for this solution.Text: Annedore Bose-MundeThe family-owned company Joop van Zanten has been a full service provider for plasma and oxy-fuel cutting of steel since 1966. The steel service centre in Veenendaal, Netherlands, now has over 40 employees and processes steel sheets ranging from 2mm to 300mm. It also offers drilling and tapping, folding, straightening, blasting and welding.Bart Kroesbergen has been plant manager at Joop van Zanten since 2018. He looks back: ‘Six years ago, there was still a lot of manual work at Joop van Zanten. But something had to change, especially in terms of competitiveness, the shortage of skilled workers and the future direction of the company.’ Two questions were on the table from the outset: ‘Can we automate to make work more attractive and more efficient? And above all, can we save costs?’ The steel processor's product range was already very broad in 2018. Therefore, another point was very important: flexibility.‘The company should be set up for the next 20 years. Increasingly, component manufacturing is being carried out for end producers. To this end, many technologies have been brought in-house, such as welding, machining and edging. We are trying to implement the processes in such a way that they are as automated as possible. This should ensure predictability for new products and product reproducibility, as well as consistent quality and, of course, competitiveness in Europe,’ says Managing Director Kroesbergen, defining the path and goal.Since 2018, the family-owned company, together with an external director, has implemented a new strategy for the company. At the same time, the next generation of the family are also being prepared for a management position. Together with Bart Kroesbergen, who has an extensive background in business administration, their combined experience, knowledge and shared desire for change has already achieved a great deal. Joop van Zanten is already one of the most modern steel processing companies in the Netherlands, characterised by its high level of automation and digitalisation, and consistently driving forward the topic of Industry 4.0.Investment in two efficient, identical systems Joop van Zanten's customer base has changed in recent years. Initially, the company mainly operated as a mass steel cutting company. It was about kilograms and heavy steel. The customers came, for example, from the bridge or shipbuilding industry. But the company wanted to and needed to become more flexible and expand its range of services – including with regard to material thicknesses. Now, the range of processed material thicknesses is in the range of 2mm to 300mm. Currently, the smallest product is a few centimetres in size, while the largest is almost 14 metres. A total of 90,000 different parts were produced in 2023. Today, customers are mostly from industry, mechanical engineering and the transport sector. The focus of production is on supplying customers with a complete end product that has been efficiently manufactured. The processes are to be automated to such an extent that a high level of economic efficiency is achieved. To achieve these goals, the Dutch company invested in two identical Lissmac systems, each consisting of an SBM-M 1500 D2 slag removal machine, an SBM-XL 1500 G2S2 grinding and deburring machine (passage width of both systems is 1,500 mm), as well as extraction and conveyor technology. The first system was purchased in 2019, the second in 2021. ‘We visited several manufacturers, spoke with system representatives and also looked around at the major trade fairs,’ says Plant Manager Kroesbergen, looking back. But one point ultimately convinced the decision-makers at Joop van Zanten: the two-sided processing that the Lissmac systems make possible. ‘We sometimes run products that are 20 metres long through the systems. The Lissmac technology makes this possible in just a single process step, which makes our work much easier,’ says Kroesbergen. The otherwise necessary handling and the associated complex logistics in the halls are no longer required. Extensive tests were carried out before the decision was made in favour of the Lissmac Maschinenbau GmbH system. This was also necessary due to the high variety of parts. The practical tests were carried out with the products and materials in mind. Fine adjustments were made and the system went into operation in 2019. ‘We decided that all the parts we manufacture would pass through the Lissmac system. Of course, the surface quality and feel are now better. But every single part also looks really good,’ says Bart Kroesbergen. Based on the technical requirements alone, this would only be necessary for about 50 percent of all parts. But in the meantime, the deburred and rounded parts have also become a quality feature for Joop van Zanten that customers appreciate. And then there is the plant manager's always forward-looking view of fully automated processes. ‘If you have a second processing stream in a process that is not to be automated, it is more difficult to automate it completely.’ The second system, located in a different production area, was purchased in 2021. The production volume had increased significantly, and certain production ranges needed to be processed efficiently for logistical reasons. However, this identical system was also purchased with a view to the planned significant expansion of the automation. The goal is automation in the thick sheet metal sector One of the two Lissmac lines will already be used in automated production. Steel sheets up to 40mm thick will be processed here. The second system will be used to process sheets up to 100mm thick. Automation is planned here as well. ‘The requirement that the systems be prepared for future automation was specified by Joop van Zanten at the start of the project for the first system,’ recalls Robert Dimmler, Sales Director Metal Processing at Lissmac. This is also a very important point in terms of ensuring smooth interface communication between different applications and systems. A system consisting of a slag removal machine, a grinding and deburring machine, and extraction and conveyor technology is one of the machine manufacturer's standard applications. ‘But Joop van Zanten's vision of the automation that was considered from the outset was truly visionary. Automation in the thick sheet metal sector was still uncommon at that time,’ says Dimmler. ’Automation is usually known from the thin sheet metal sector. This was now to be transformed into the thick sheet metal sector, where completely different workpiece dimensions and part weights are common. Being involved in finding a solution here is an exciting part and definitely also a challenge.’ ‘Our dream was to use a fully automated factory for thick sheet metal processing within ten years. The question was not ‘will we be able to implement this?’ but rather ‘how will we be able to implement this in concrete terms?’ says Bart Kroesbergen. To this end, experience from other industries was also incorporated into the considerations, for example from concrete construction, where very high unit weights are also involved. This optimistic thinking outside the box also convinced machine builder Lissmac. ‘A system manufacturer also continues to develop based on customer requirements. And when you have a visionary customer like Joop van Zanten, it also triggers us,’ adds Robert Dimmler. When it comes to new implementation ideas, it's simply part of the process to think outside the box. The challenge lies in the weight and variety of the parts The weight, variety and complexity of the structures require new approaches to implementation with regard to automation. The mechanical removal of parts using robotics is therefore not yet fully implemented. Here, Joop van Zanten is working together with Messer Cutting Systems GmbH, Beuting Metalltechnik GmbH & Co. KG and Lissmac on a suitable solution. The goal that the partners involved are working on is a solution that will cover the company's range of thick sheet metal core parts. The systems are to run automatically next year.The fact that all systems in operation at the Dutch steel service centre are connected to a software platform and OPC UA interfaces is another important point for seamless automation. Machine manufacturer Lissmac has also defined the OPC UA standard (standard for secure, cross-vendor networking for industrial systems) as the standard for its own products. One example shows how important this topic is: a customer of Joop van Zanten manufactures the frame of a system that produces chips. The steel plates required for this, which are manufactured by the steel service centre, must not be touched by hand so that finger grease does not get onto the systems. Without automation, this would be inconceivable. One thing is certain: the project partners are working together on a truly visionary task. However, solving this task involves very pragmatic issues: technical implementation, constant communication, and continuous learning and support from each other.
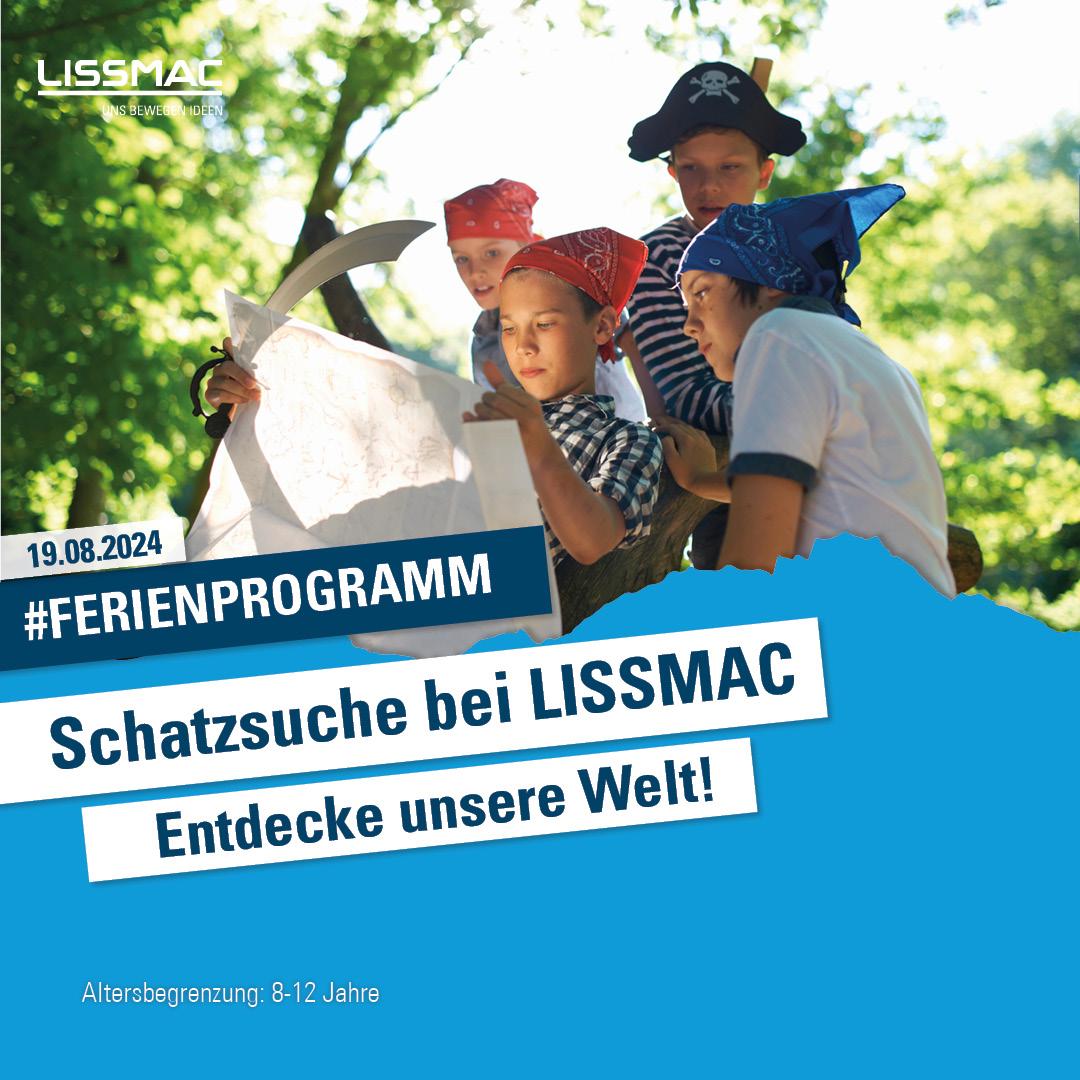
Hast Du Lust Dich auf die Suche nach dem Schatz bei LISSMAC zu machen?
Termin: 19.08.2024 Max. 15 Teilnehmer Altersbegrenzung: 8-12 Jahre Bei der Schatzsuche wirst Du LISSMAC und die Produkte, sowie den Ablauf vom Blech bis zur Maschine kennenlernen. Zudem erwarten Dich spannende Projekte, die unsere Azubis gebaut haben. Eines dieser Projekte war ein Tischkicker. Am Ende unserer Schatzsuche erwarten Dich tolle Geschenke und Informationen zum Schnupperpraktikum, Ausbildungsstellen,…. Für Essen und Trinken ist ausreichend gesorgt! Alle Informationen & die Möglichkeit zur Anmeldung hier Anmeldung möglich per Telefon, E-Mail oder Einwurf der Anmeldekarte bei der Stadt Bad Wurzach. Zum Programmheft (LISSMAC S.29)
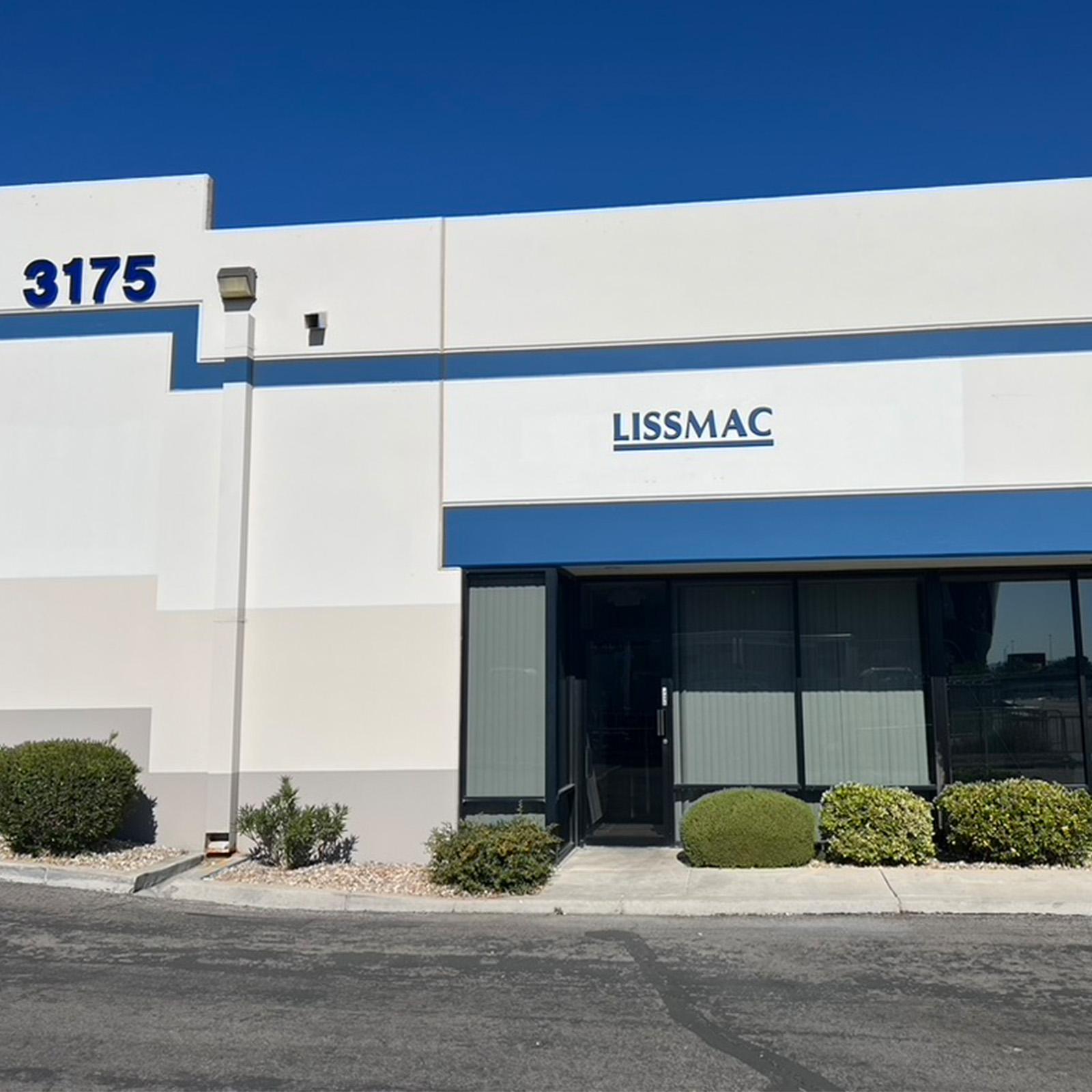
LISSMAC Corporation opens new branch office in Las Vegas, NV
On January 1, 2024, LISSMAC Corporation officially opened a satellite branch in Las Vegas, Nevada. Initially, the Las Vegas office will serve as a sales and service location for the South and West Coast of the USA. "The new office in Las Vegas is an important step for us to expand our sales and service activities in the Southwest," says Ingo Heiland, Vice President of LISSMAC Corporation. "Las Vegas is an important trade show location for us with World of Concrete, an important annual trade show for concrete and masonry, as well as the recurring industry exhibition FABTECH. Furthermore, Nevada is conveniently located in the Southwest and has a strong manufacturing and construction sector itself." LISSMAC Corporation was founded in 2007 in Mechanicville, New York State and has been serving the US market with innovative and reliable solutions in the Construction Technology and Metal Processing divisions ever since. With 25 employees, a showroom for live demonstrations, a service team and its own spare parts and goods warehouse, the Mechanicville site is ideally equipped to support customers from application consulting to after sales. "We will be expanding the Las Vegas office in the coming year and hiring additional employees to achieve the same level of customer service as in upstate New York," explains Ingo Heiland. "The aim is to carry out product demonstrations in the Metal Processing division both at long-standing reference customers in the vicinity and, in the medium term, at our own site. In addition, numerous regional construction projects will allow us to demonstrate our civil engineering products," adds Norbert Zell, Branch Manager in Las Vegas. The new office is located five miles from the airport and across the street from Allegiant stadium, the venue for Super Bowl LVIII in February 2024. As of January 1, 2024, LISSMAC Corporation has a satellite branch serving the Southwest and West Coast of the USA from the new location: LISSMAC Corporation Satellite Branch 3175 W Ali Baba Ln Suite 806 Las Vegas, NV 89118 USA
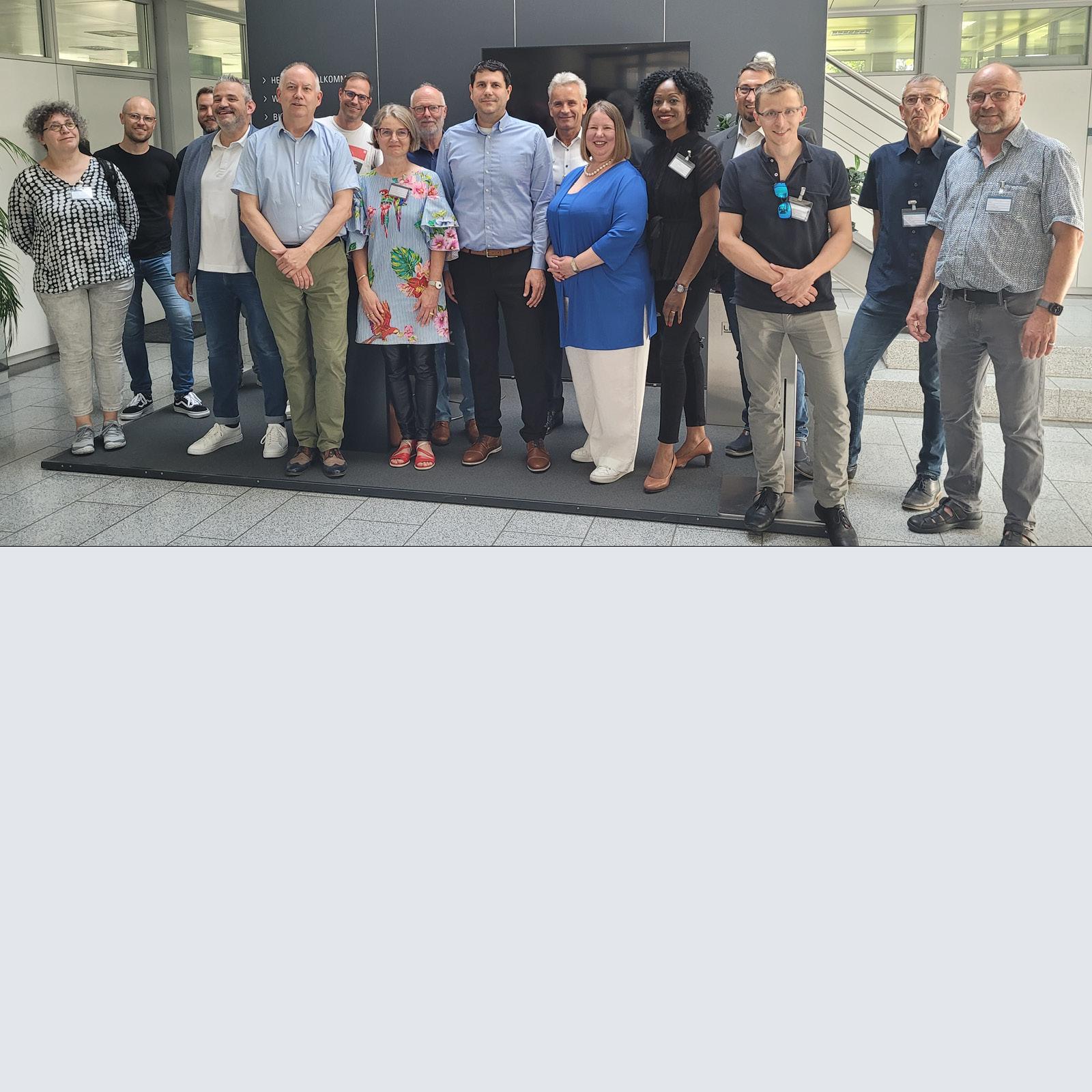
Factory tour HGV Bad Wurzach
On 26.06.2024, we hosted a group of visitors from the Bad Wurzach Trade and Commerce Association. The HGV is an association of traders in Bad Wurzach. The interested guests, mainly managing directors of companies in Wurzach, took the opportunity to visit our company. After the reception and welcome by the management, the guests were divided into two groups and guided through the production halls by Daniel Keller and Hinrich Dohrmann. The visitors were also shown the new hall and explained the digitization and automation of our work processes, but the current difficult economic environment was also discussed, but always with an optimistic view to the future. After the one-hour tour, there was an opportunity for questions and informal discussions over a snack.
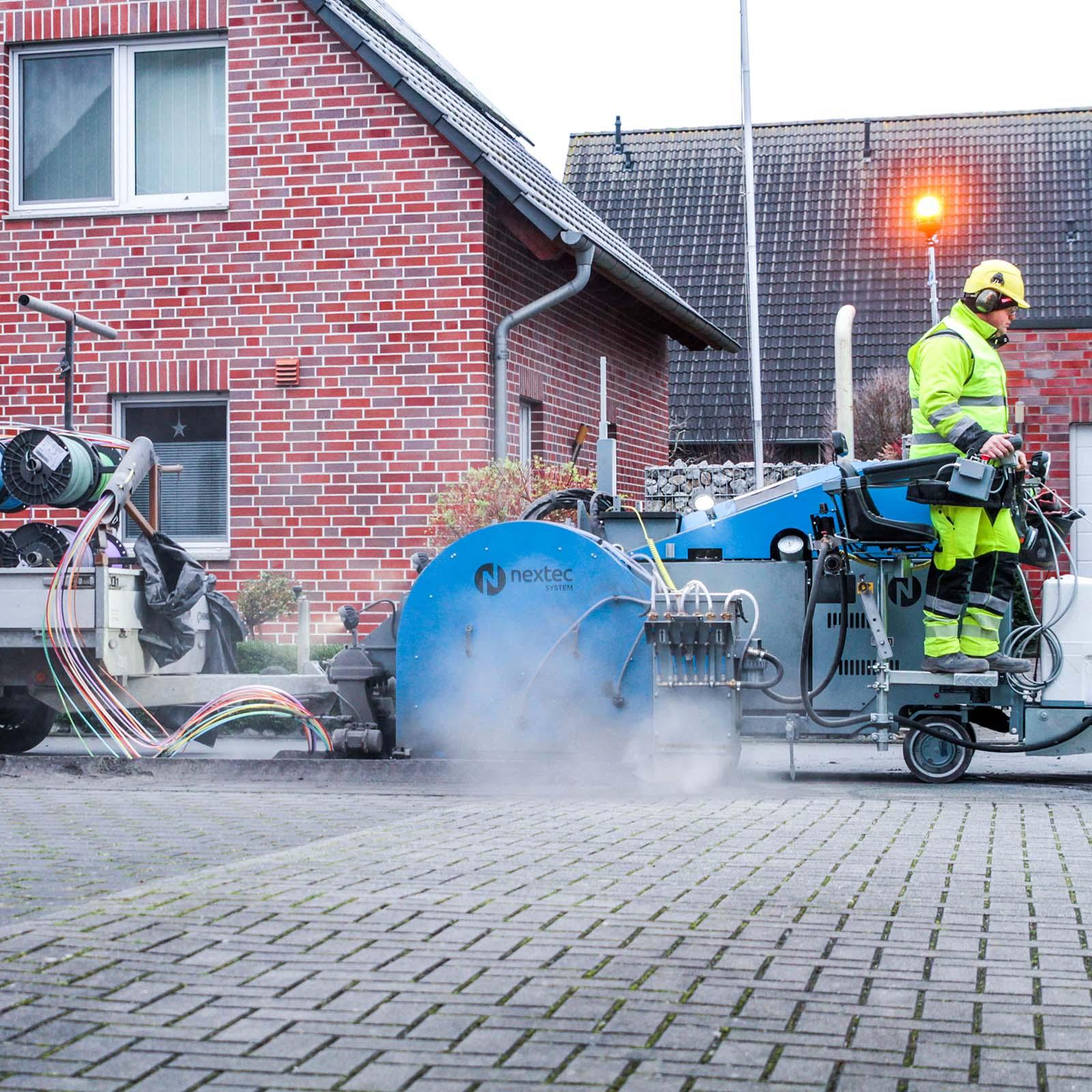
DIN 18220: A MILESTONE FOR FIBER OPTIC EXPANSION
DIN 18220 COMES INTO FORCEOn 28.07.2023, "DIN 18220:2023-08. Trenching, milling and ploughing methods for laying empty conduit infrastructures and fiber optic cables for telecommunications networks" was adopted. The document was ceremoniously handed over at an event on the gigabit strategy of the Federal Ministry for Digital and Transport (BMDV). According to Section 126 of the German Telecommunications Act (TKG), it is to be applied uniformly by all parties involved as a recognized technical rule from the time of publication. DIN 18220 is intended to contribute to the cost-effective acceleration and, above all, high-quality implementation of fiber optic expansion. It defines clear conditions for use and implementation and sets the legal framework for achieving a milestone in broadband and fiber optic expansion. DIN 18220 increases investment security for all parties involved, especially for telecommunications companies. To date, there have been neither standardized framework conditions nor uniform principles for the application of the trenching method. Up to now, most municipalities have mainly chosen the open construction method as the laying method for fiber optic expansion, as the minimum overlap had to be at least 60 cm before the standard. Since 2012, the TKG has permitted the use of shallow laying (trenching, shallow laying methods), which also includes non-standardized methods such as trenching. However, the process has so far had difficulty establishing itself on the market. This is primarily due to legal uncertainties for all parties involved. These are inevitably associated with the lack of binding technical specifications, in the form of a binding standard, for the use of such alternative laying methods. The difficulty lay in particular in differences between road construction authorities, contractors and telecommunications companies regarding the specific execution and implementation. As a result, there were delays in the expansion of the fiber optic infrastructure. THIS CHANGES WITH THE NEW DIN 18220Up to now, most local authorities have mainly chosen the open construction method as the laying method for fiber optic expansion, as the minimum cover had to be at least 60 cm before the standard was introduced. DIN 18220 now regulates laying methods for reduced construction depths, including diamond trenching from LISSMAC (38 cm laying depth)."With DIN 18220, fiber optic installation will not only be easier in the future, but also of higher quality, faster, more cost-effective and more resource-efficient. DIN 18220 creates the necessary legal certainty and investment security for all parties involved," said BMDV State Secretary Stefan Schnorr, describing the importance of the new standard. WHAT DIN 18220 MEANS FOR LISSMACLISSMAC has been active in diamond trenching for around 10 years. Due to our experience in the field of joint cutting, we are a long-standing member of the VDMA (German Engineering Federation) and were involved in the creation of the standard as a member of the standardization committee. We are very pleased about the recognition of the alternative laying methods for fiber optic expansion, including LISSMAC diamond trenching, as the standard creates clarity for the construction industry, all municipalities, communities and telecommunications companies. Find out more about diamond trenching following DIN 18220 with LISSMAC. Read further background information to DIN 18220 (german). Watch the full video "Glasfaser ohne Einblasen" together with Telekom (with english subtitles).
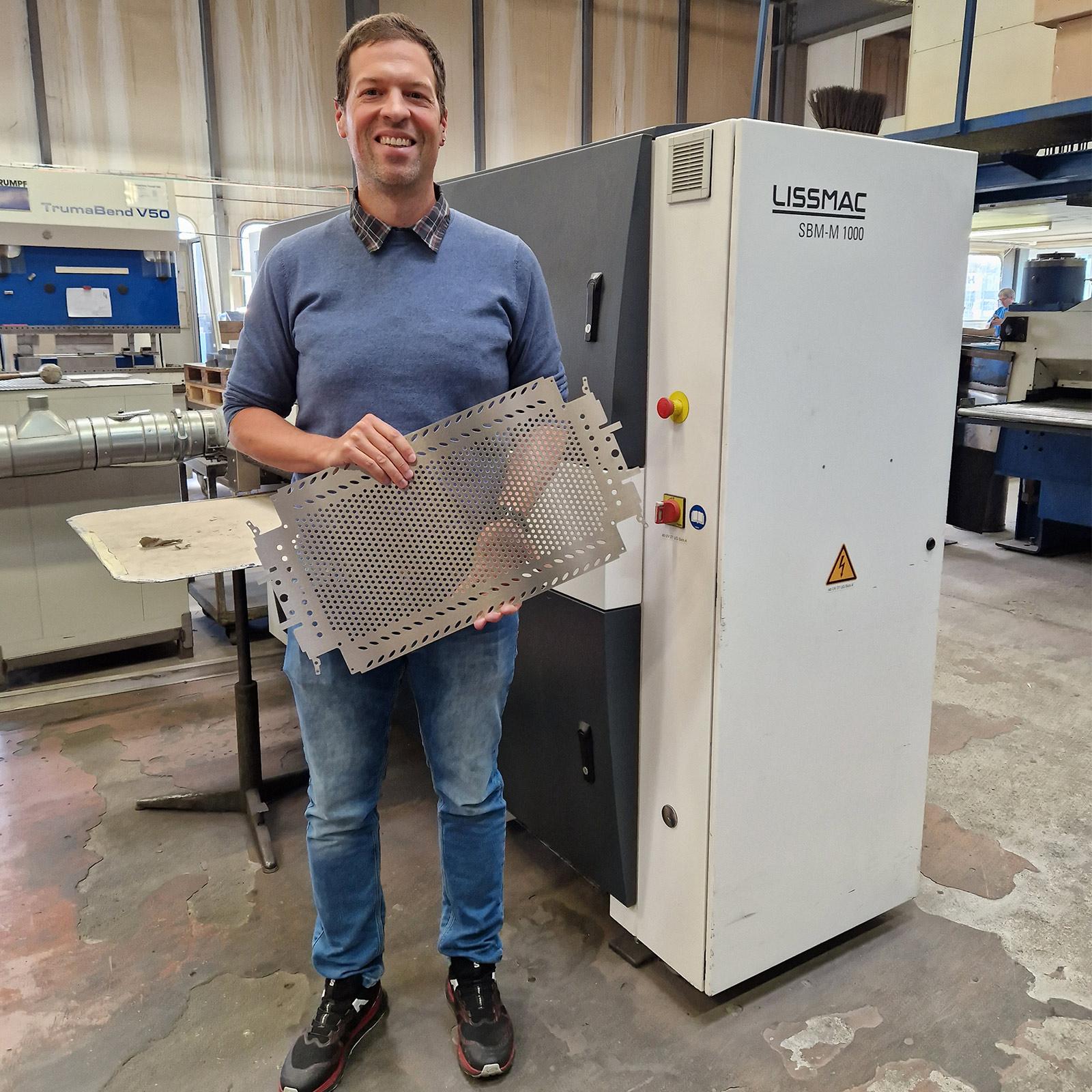
Process Reliability Thanks To Two New Sanding And Deburring Systems
A Swiss sheet metal processor invested in two grinding and deburring systems. They are used for the removal of secondary burrs and for an optimum surface finish. The focus of the replacement purchases was on flexibility, increased efficiency and reliable service. Text: Annedore Bose-Munde Ulrich Oppliger AG from Lyssach in Switzerland has been successful on the market for 54 years. The company's core competence is sheet metal processing - from bending, laser punching and cutting to welding, straightening and deburring. Prototypes, individual items or series are manufactured. Marc Burkhalter has been with the company for nine years. He initially worked as operations manager for two years. He then took over the business from his father-in-law, the owner of the company, and has now been managing director for seven years. He knows how important the quality of the parts is. The company has now invested in two new Lissmac systems in order to reliably ensure this and to be able to produce more efficiently and reliably in the future. The impetus for one of the investments was a customer part whose production a technical problem occurred again and again. For a company that develops and distributes surgical instruments, Oppliger has been manufacturing components for sterilisation trays for several years, which are later used in the pre-operating theatre to prepare the surgical instruments. The punched parts that are further processed at the customer's premises are given a new look at Oppliger by subsequent sanding for a harmonised surface finish. And this is exactly where the problem arose: a secondary burr. In addition, the customer ordered ever larger quantities.Service is an important decision criterion The secondary burr often had to be ground away by hand. The old system was also frequently overloaded. The limit was reached in 2018. "The repeated dissatisfaction with the quality of the components and the time-consuming manual reworking of the components satisfied neither the customer nor us. After all, a precise surface finish and clean further processing are essential for medical technology products. We had to act," Marc Burkhalter looks back. A reliable solution was therefore required. The quality requirements were defined together with the customer before the new acquisition. And Oppliger also analysed the extent to which the investment would pay off in the long term. The specific application for the plant technology to be purchased was given and so the key data for the new machine was quickly finalised: It had to be a compact system because the space available in the hall was limited. And Marc Burkhalter mentions another decision point: "It was important for me to have a contact person for the sanding area. I also wanted to work with our long-standing service partner Wolfgang Kohler on this point. Communication works here, the service works and fast spare parts procurement is guaranteed." WKS GmbH - Wolfgang Kohler Service GmbH, based in Bad-Zurzach in Switzerland - is a service and sales company specialising in straightening and deburring machines. The portfolio also includes Lissmac systems. Universal Entry-Level Machine For Burr Removal The decision-making process was swift. The range of parts and the spatial conditions were set. And so, in 2020, the Swiss sheet metal processor opted for an SBM-M 1000 S2 dry sanding system from Lissmac. The grinding and deburring machine is a universal entry-level machine for removing cutting burrs from laser and punched parts. The sheet metal parts are also given an optimised surface finish. Bertrand Laroche is Area Sales Manager Metal Processing at Lissmac Maschinenbau GmbH. He accompanied the process. "The SBM-M 1000 S2 is a functional machine in terms of design and operation. The system was just right for the application at Oppliger," he says. Due to the two counter-rotating belts and the double-sided processing, no return of the parts is required. In addition, less floor space is required. The machine type was therefore quickly decided. Following a visit to the Lissmac demonstration centre in Bad Wurzach, only the system design and the extraction system were adjusted and the abrasive grain was specified. The grinding and deburring machine was then purchased and installed in 2020. "Our customer is satisfied. Since the new system has been in use, there have been no more problems with the secondary burr. The surface quality has also improved somewhat thanks to the fine abrasive grain," says Marc Burkhalter happily. Initially, the new plant was used exclusively to produce parts for the manufacturer of medical instruments. In the meantime, it is also used for other applications, especially for parts that need to be machined on both sides. These are mainly industrial parts made of thin stainless steel sheet. The SBM-M 1000 S2 focuses on removing sharp edges from thin stainless steel parts at low cost and with low energy consumption -. "This was Lissmac's first application with the Lyssach-based company. It's great that we have been able to place this system concept, which has been tried and tested on the market for a long time, here," says a delighted Bertrand Laroche, Area Sales Manager. Powergrip Belt Ensures Efficiency And Flexibility A year later, another replacement was due. The previous system was unreliable, had a high risk of failure and spare parts were difficult to obtain. In addition, smaller parts also had to be deburred. Oppliger took a look around the usual trade fairs. And with the knowledge that Lissmac also manufactures systems in this segment, the Swiss company approached the Bad Wurzach-based machine manufacturer in a targeted manner. The key data for the new system was finalised: Processing of the widest possible range of stainless steel parts, i.e. a high degree of flexibility. And once again, it had to be as small as possible. In addition to the set functionalities, the price-performance ratio should be right and the delivery times should be acceptable. In addition, Wolfgang Kohler Service GmbH was to act as a partner again. Marc Burkhalter decided in favour of the SMD 123 RE deburring machine. Here too, the technical highlight of the system is the Powergrip belt, on which the parts rest during processing and are held in place by the high adhesive force and without magnets or vacuum. "We are the only ones in the industry to work with a conveyor belt like this. That means: More consultation is required with the customer than with other, familiar technologies," says Bertrand Laroche. However, the Powergrip belt is not only flexible, but also very energy-efficient. A vacuum, Laroche continues, is loud, for example, requires a lot of energy and is not suitable for all part geometries. Marc Burkhalter is convinced by the technology, which has been running reliably since installation. The new system will be used to produce smaller parts for a wide range of industrial sectors as well as parts for which the visual appearance plays a role and a good surface finish is important. Efficiency and stability for the futureOppliger, one of the first laser operators in Switzerland, manufactures for industrial customers in a wide range of sectors. A good 600 tonnes of sheet steel are currently processed, of which around 50 per cent is steel and 50 per cent stainless steel. Looking to the future, Managing Director Burkhalter says: "It would be good to maintain the current status. We rely on healthy growth, customised machinery, automation and the expertise to serve a wide range of customers. Lean processes are also important: Efficiency is to be increased in all areas, both in the office and in production." Area Sales Manager Laroche is also looking ahead: "We want to support our customers with more efficient abrasives in the future. Lissmac is working on this together with abrasive manufacturers. This is intended to improve and optimise the performance of the machine, i.e. to increase quality and performance. And with a view to suitable system technology, the topics of remote maintenance and digitalisation are also increasingly being implemented." Kontakt:Ulrich Oppliger AGMarc BurkhalterIndustriestrasse 23421 Lyssach, Schweizwww.uoppligerag.ch *** Lissmac Maschinenbau GmbHBertrand LarocheLanzstraße 488410 Bad Wurzachwww.lissmac.com Textautor:Annedore Bose-MundeFreelance specialised journalist for Technology and business, Erfurt www.bose-munde.de