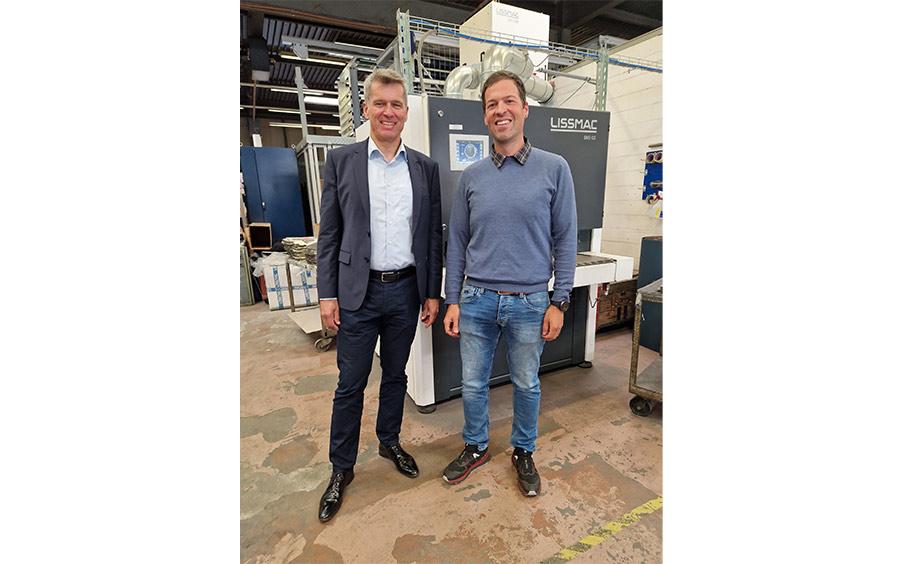
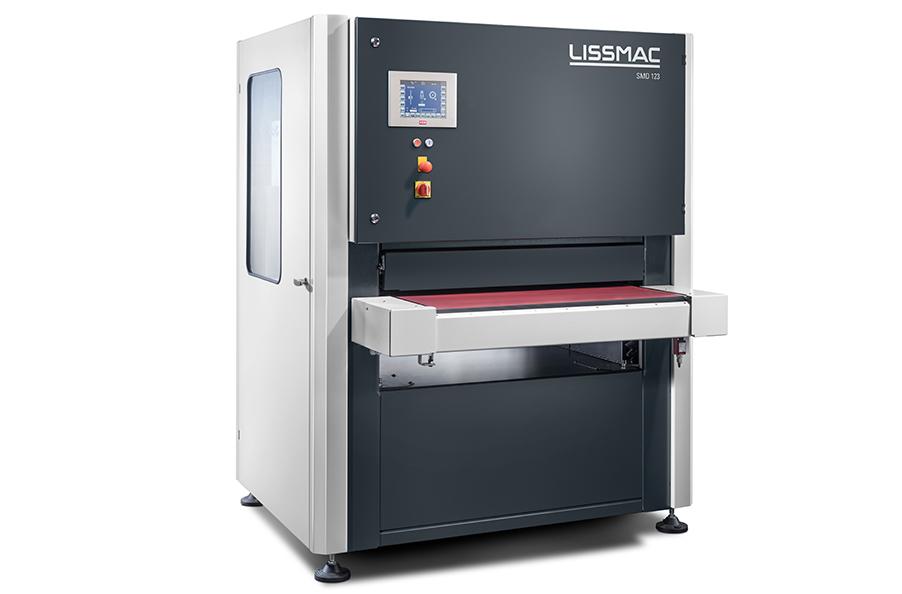
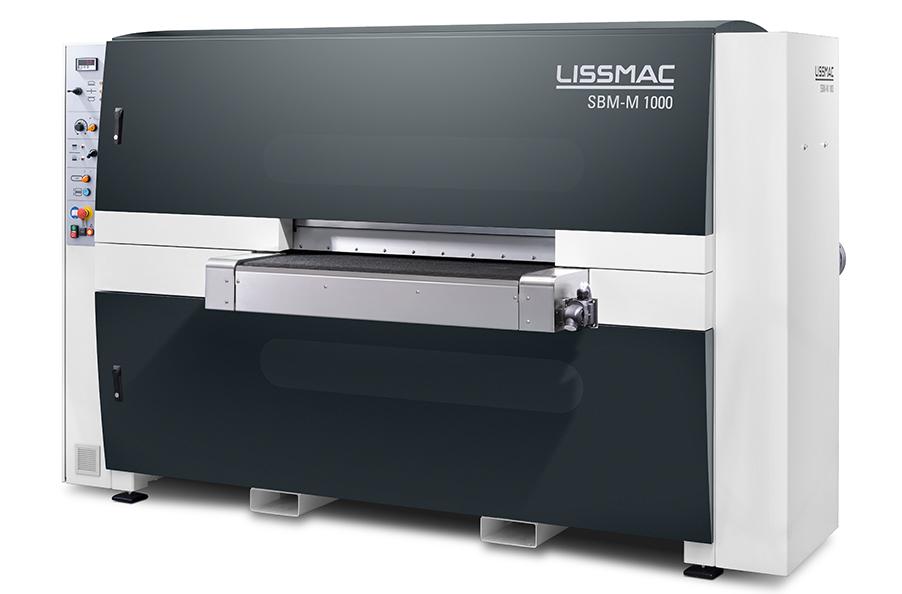
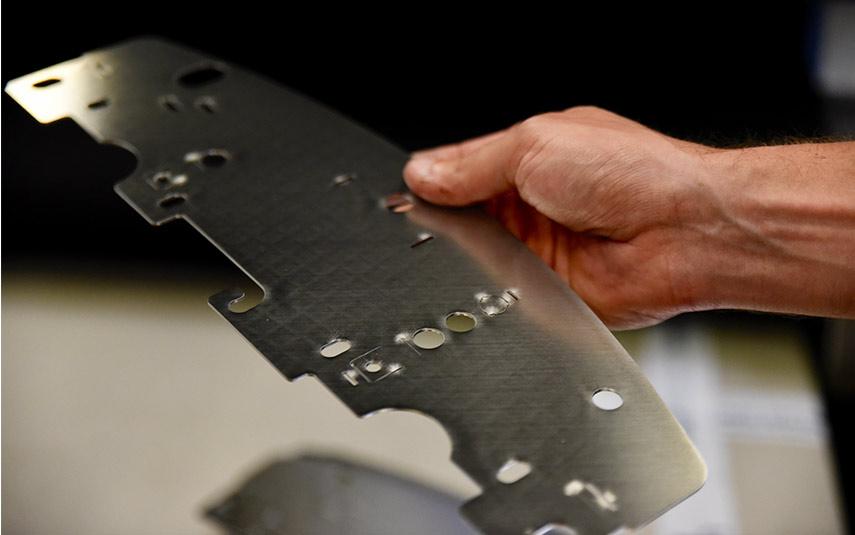
Process Reliability Thanks To Two New Sanding And Deburring Systems
October 19, 2023
A Swiss sheet metal processor invested in two grinding and deburring systems. They are used for the removal of secondary burrs and for an optimum surface finish. The focus of the replacement purchases was on flexibility, increased efficiency and reliable service.
Text: Annedore Bose-Munde
Ulrich Oppliger AG from Lyssach in Switzerland has been successful on the market for 54 years. The company's core competence is sheet metal processing - from bending, laser punching and cutting to welding, straightening and deburring. Prototypes, individual items or series are manufactured.
Marc Burkhalter has been with the company for nine years. He initially worked as operations manager for two years. He then took over the business from his father-in-law, the owner of the company, and has now been managing director for seven years. He knows how important the quality of the parts is. The company has now invested in two new Lissmac systems in order to reliably ensure this and to be able to produce more efficiently and reliably in the future.
The impetus for one of the investments was a customer part whose production a technical problem occurred again and again. For a company that develops and distributes surgical instruments, Oppliger has been manufacturing components for sterilisation trays for several years, which are later used in the pre-operating theatre to prepare the surgical instruments.
The punched parts that are further processed at the customer's premises are given a new look at Oppliger by subsequent sanding for a harmonised surface finish. And this is exactly where the problem arose: a secondary burr. In addition, the customer ordered ever larger quantities.
Service is an important decision criterion
The secondary burr often had to be ground away by hand. The old system was also frequently overloaded. The limit was reached in 2018. "The repeated dissatisfaction with the quality of the components and the time-consuming manual reworking of the components satisfied neither the customer nor us. After all, a precise surface finish and clean further processing are essential for medical technology products. We had to act," Marc Burkhalter looks back. A reliable solution was therefore required.
The quality requirements were defined together with the customer before the new acquisition. And Oppliger also analysed the extent to which the investment would pay off in the long term.
The specific application for the plant technology to be purchased was given and so the key data for the new machine was quickly finalised: It had to be a compact system because the space available in the hall was limited. And Marc Burkhalter mentions another decision point: "It was important for me to have a contact person for the sanding area. I also wanted to work with our long-standing service partner Wolfgang Kohler on this point. Communication works here, the service works and fast spare parts procurement is guaranteed." WKS GmbH - Wolfgang Kohler Service GmbH, based in Bad-Zurzach in Switzerland - is a service and sales company specialising in straightening and deburring machines. The portfolio also includes Lissmac systems.
Universal Entry-Level Machine For Burr Removal
The decision-making process was swift. The range of parts and the spatial conditions were set. And so, in 2020, the Swiss sheet metal processor opted for an SBM-M 1000 S2 dry sanding system from Lissmac. The grinding and deburring machine is a universal entry-level machine for removing cutting burrs from laser and punched parts. The sheet metal parts are also given an optimised surface finish.
Bertrand Laroche is Area Sales Manager Metal Processing at Lissmac Maschinenbau GmbH. He accompanied the process. "The SBM-M 1000 S2 is a functional machine in terms of design and operation. The system was just right for the application at Oppliger," he says. Due to the two counter-rotating belts and the double-sided processing, no return of the parts is required. In addition, less floor space is required.
The machine type was therefore quickly decided. Following a visit to the Lissmac demonstration centre in Bad Wurzach, only the system design and the extraction system were adjusted and the abrasive grain was specified. The grinding and deburring machine was then purchased and installed in 2020.
"Our customer is satisfied. Since the new system has been in use, there have been no more problems with the secondary burr. The surface quality has also improved somewhat thanks to the fine abrasive grain," says Marc Burkhalter happily.
Initially, the new plant was used exclusively to produce parts for the manufacturer of medical instruments. In the meantime, it is also used for other applications, especially for parts that need to be machined on both sides. These are mainly industrial parts made of thin stainless steel sheet.
The SBM-M 1000 S2 focuses on removing sharp edges from thin stainless steel parts at low cost and with low energy consumption -. "This was Lissmac's first application with the Lyssach-based company. It's great that we have been able to place this system concept, which has been tried and tested on the market for a long time, here," says a delighted Bertrand Laroche, Area Sales Manager.
Powergrip Belt Ensures Efficiency And Flexibility
A year later, another replacement was due. The previous system was unreliable, had a high risk of failure and spare parts were difficult to obtain. In addition, smaller parts also had to be deburred. Oppliger took a look around the usual trade fairs. And with the knowledge that Lissmac also manufactures systems in this segment, the Swiss company approached the Bad Wurzach-based machine manufacturer in a targeted manner.
The key data for the new system was finalised: Processing of the widest possible range of stainless steel parts, i.e. a high degree of flexibility. And once again, it had to be as small as possible. In addition to the set functionalities, the price-performance ratio should be right and the delivery times should be acceptable. In addition, Wolfgang Kohler Service GmbH was to act as a partner again.
Marc Burkhalter decided in favour of the SMD 123 RE deburring machine. Here too, the technical highlight of the system is the Powergrip belt, on which the parts rest during processing and are held in place by the high adhesive force and without magnets or vacuum.
"We are the only ones in the industry to work with a conveyor belt like this. That means: More consultation is required with the customer than with other, familiar technologies," says Bertrand Laroche. However, the Powergrip belt is not only flexible, but also very energy-efficient. A vacuum, Laroche continues, is loud, for example, requires a lot of energy and is not suitable for all part geometries.
Marc Burkhalter is convinced by the technology, which has been running reliably since installation. The new system will be used to produce smaller parts for a wide range of industrial sectors as well as parts for which the visual appearance plays a role and a good surface finish is important.
Efficiency and stability for the future
Oppliger, one of the first laser operators in Switzerland, manufactures for industrial customers in a wide range of sectors. A good 600 tonnes of sheet steel are currently processed, of which around 50 per cent is steel and 50 per cent stainless steel.
Looking to the future, Managing Director Burkhalter says: "It would be good to maintain the current status. We rely on healthy growth, customised machinery, automation and the expertise to serve a wide range of customers. Lean processes are also important: Efficiency is to be increased in all areas, both in the office and in production."
Area Sales Manager Laroche is also looking ahead: "We want to support our customers with more efficient abrasives in the future. Lissmac is working on this together with abrasive manufacturers. This is intended to improve and optimise the performance of the machine, i.e. to increase quality and performance. And with a view to suitable system technology, the topics of remote maintenance and digitalisation are also increasingly being implemented."
Kontakt:
Ulrich Oppliger AG
Marc Burkhalter
Industriestrasse 2
3421 Lyssach, Schweiz
www.uoppligerag.ch
***
Lissmac Maschinenbau GmbH
Bertrand Laroche
Lanzstraße 4
88410 Bad Wurzach
www.lissmac.com
Textautor:
Annedore Bose-Munde
Freelance specialised journalist for Technology and business, Erfurt
www.bose-munde.de