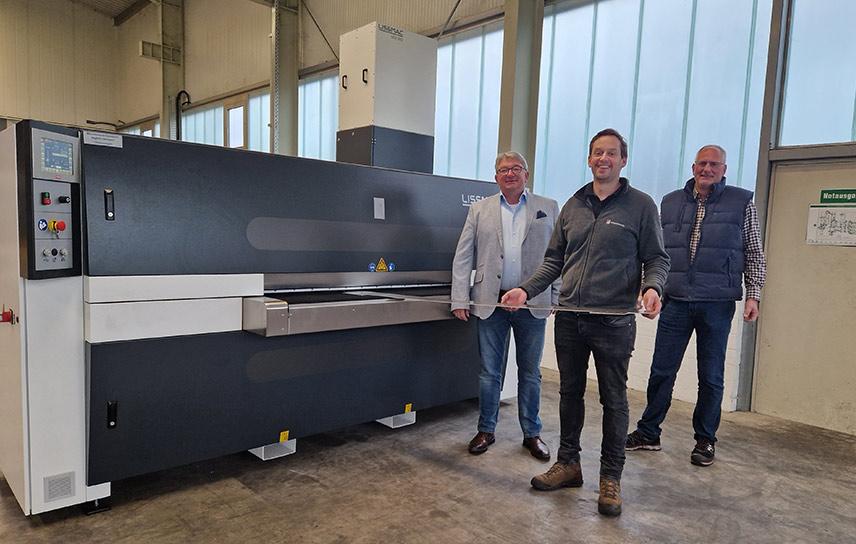
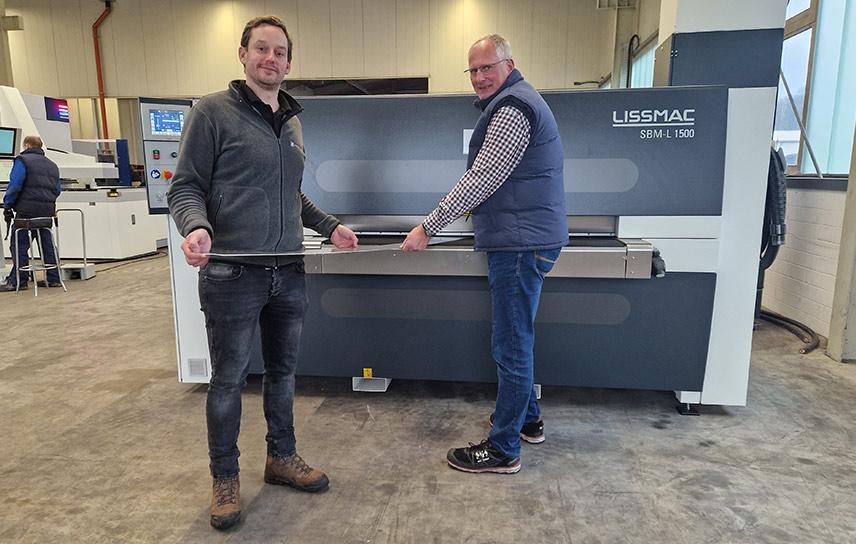
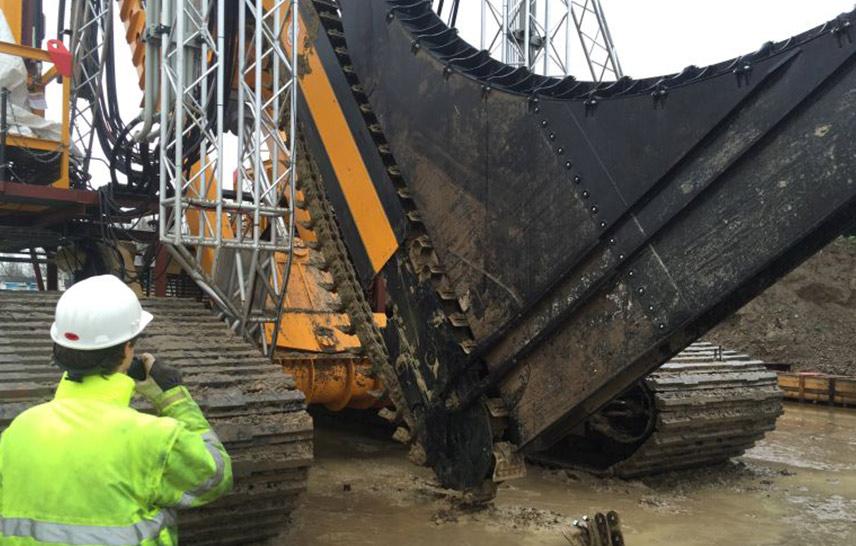
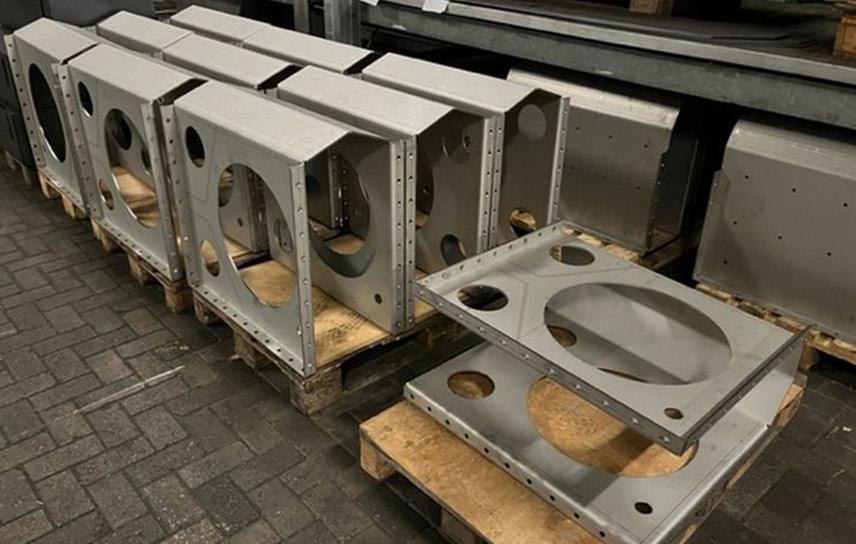
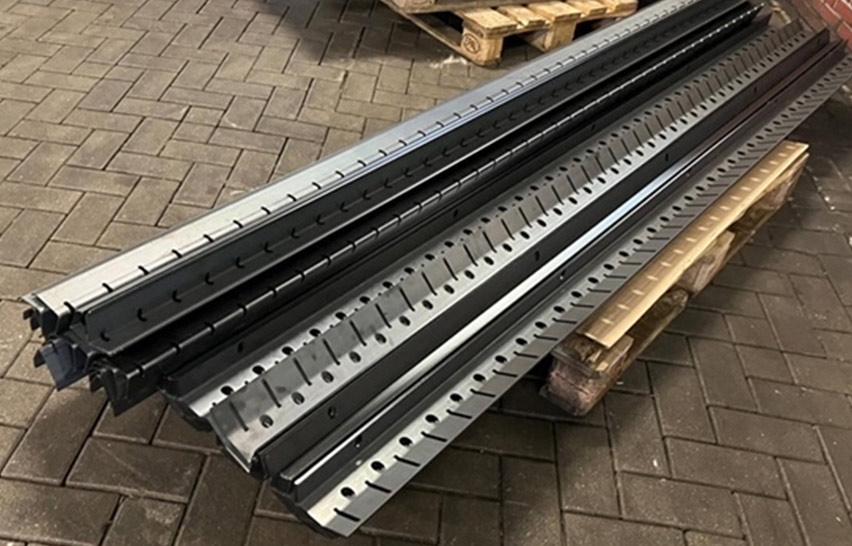

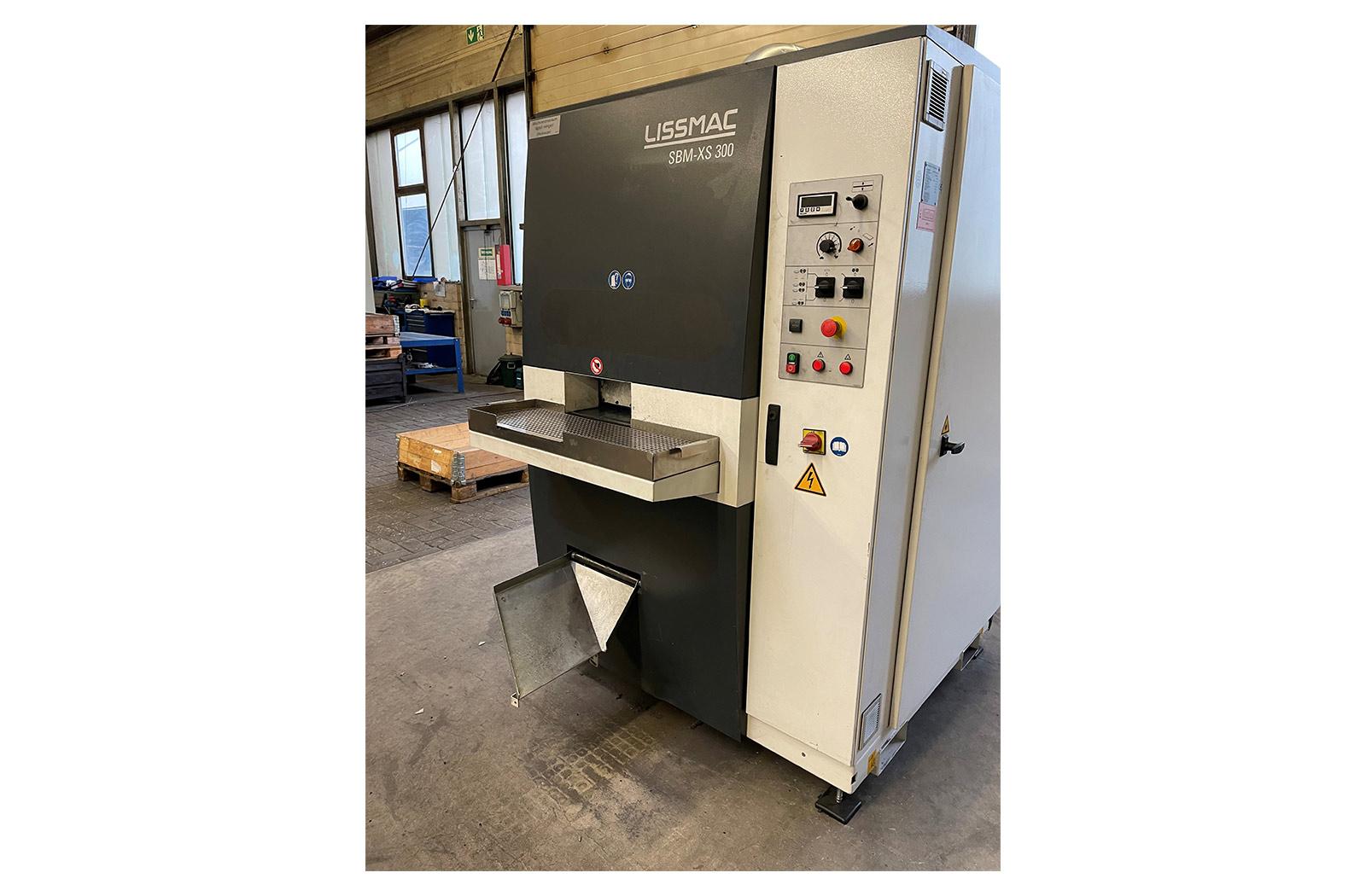
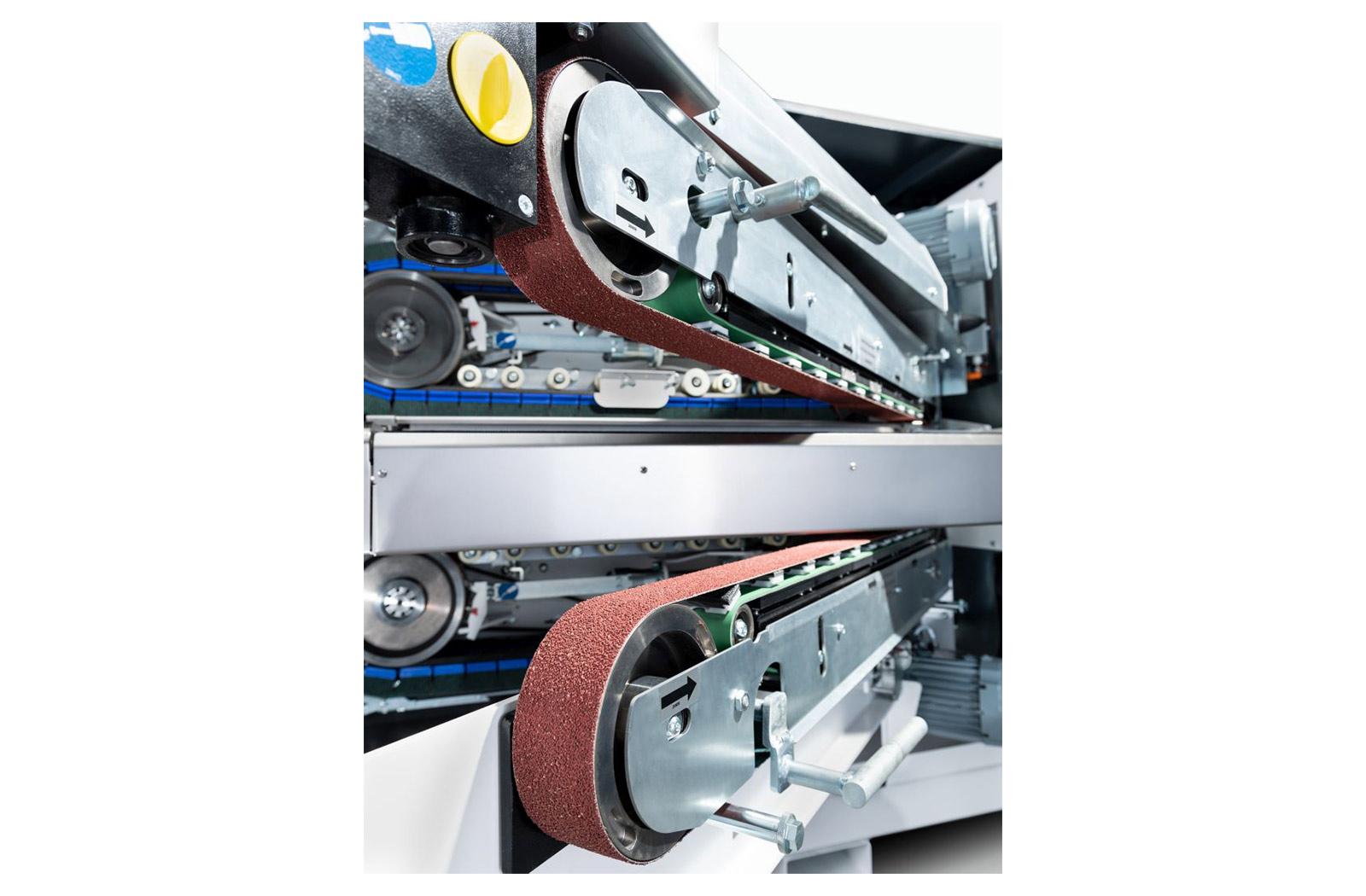
Resource Efficiency, Low Power Consumption And New Business Fields
April 12, 2023
Quality and functionality are also important and are arguments for investing in machinery and equipment. But the reliability of the machine builder, speed, flexibility and uncomplicated hands-on cooperation are often just as decisive for a new acquisition. When purchasing new grinding and deburring technology, a company from the Ammerland region relies on precisely these classic SME values.
Text: Annedore Bose-Munde
The expertise of Wiechmann Ketten- and Kettenräderbau GmbH from Edewecht lies in two areas. On the one hand, this is chain production. Wear parts for trenchers and other applications are manufactured here, for example milling chains, sprockets or digging tools. In the second competence area - of sheet metal processing - everything revolves around laser cutting, forming as well as deburring, edge rounding and grinding.
The company was founded in 1963 by the current senior, Otto Wiechmann, and began with the production of wear parts for cable trenchers, later adding chain production and in 1999 sheet metal production. Today Wiechmann employs 55 people. About half of them work in sheet metal production. Here, production is carried out for a wide range of industries, such as the food and packaging industries. About 10 per cent of the parts are manufactured for the company's own products in chain production. These are mostly parts that have to be touched by hand.
Quality, reproducible results and efficiency
For Andre Wiechmann, the company's managing director, safety is an important issue. "We wanted to move away from hand deburring. The risk of injury should be minimised. In addition, the quality requirements of our customers have continued to increase in recent years. In addition, the power consumption of the plants should be reduced and the efficiency increased," he looks back at the starting point of the considerations.
These criteria are also important to Hinrich Böhlje, who joined Wiechmann in 2015. Looking back, the sheet metal production manager says: "At the time, we had the Lissmac SBM-M 1000 S2, which we bought in 2006, and two other machines for rounding edges. The other two plants consumed a lot of electricity. Moreover, these did not have the option of machining the parts on both sides. So there was always a need for reworking or a second operation. And with the Lissmac system at the time, it was only possible to process sheets with a width of a thousand. But we also cut parts up to two metres wide."
So the decision was made to invest in new plant technology. The focus of the project was to increase efficiency through double-sided machining, to cover a wider range of parts and, of course, to reduce power consumption.
Managing directors Andre Wiechmann and Hinrich Böhlje were already convinced of the reliable technology of the Bad Wurzach-based company. In 2017, an SBM-XS 300 was purchased for machining small parts - designed with a vacuum belt for parts made of stainless steel and aluminium. And so the machine manufacturer from Upper Swabia was also on the selection list when it came to new investments. In addition, production manager Böhlje knew other Lissmac plants from a previous job.
Quick decision and adapted project planning process
In the spring of 2018, Andre Wiechmann, who took over responsibility for the company from his father in 1996, made a decision after visiting a trade fair. He contacted Lissmac and the project planning procedure could start. "We have sent a large number of parts to Lissmac in Bad Wurzach for trials. And we were also there ourselves. In general, we are very close to the customer with all our products and that's what we wanted to be with the new machines," he explains. The process and the coordinated project planning for the plant took about a year. As a result, two SMB-L 1500 G1S2 sanding and deburring machines were purchased, each with an infeed and outfeed belt. This means that parts up to four metres long can also be machined on both sides. With the acquisition of the two SMB-L 1500 machines, the SMB-L 1000 was then sold and the other two grinding machines were also disposed of.
"The decision in favour of Lissmac technology was made relatively quickly," says production manager Böhlje. "On the one hand, the positive experience with a comparable plant was already there. On the other hand, there were not so many manufacturers offering double-sided machining. Last but not least, the systems are highly flexible. So if Wiechmann's products change, the units can be changed quickly and easily".
The option of adding a second machining unit now saves 50 percent machining time. In addition, only one extraction unit is required for both systems.
In addition, the SMB-L 1500 has an upstream unit with sandpaper. In addition to enabling double-sided processing, this also helps to ensure efficient workflow.
For managing director Wiechmann, it is also important to separate the materials and thus ensure that they are processed according to type in production. For example, one of the new grinding and deburring machines is used only for stainless steel and the other for mild steel.
"With machine deburring, we can now ensure efficiency in machining and guarantee reproducible machining results. These are also important sales arguments in sheet metal production," he says.
Aluminium Machining And Explosion Protection
The two SMB-L 1500s were delivered in June 2019. The second SBM-XS 300 was ordered directly with the delivery. Hinrich Böhlje tells the story behind this second small parts machine: "We were asked to produce rounded-edge aluminium sheet parts for a customer. So far, these have been lasered. However, these parts are very difficult to handle. Therefore, they had to be rounded. So we needed a machine for aluminium rounding very quickly."
Dirk Schürstedt, Area Sales Manager Metal Processing at Lissmac Maschinenbau GmbH, continues: "Yes, that was really a challenge for us. It took six weeks from the idea to purchase a new plant to delivery. Everything was very focused. Even a coordination problem regarding the necessary conveyor rollers was solved in three hours. That was impressive for everyone involved."
And with a view to aluminium machining, a third identical SMB-L 1500 for aluminium machining was also purchased in September 2022. "We have to consider explosion protection when machining aluminium. Extraction was important for the dusts produced. The purchase of a separate extraction system and the resulting conversion of an existing system seemed too costly to us. And so we decided to purchase another machine, to house it in a separate room and thus to take into account all safety aspects as well as to ensure efficient process flows," Andre Wiechmann explains the decision.
All three SMB-L units have essentially the same equipment and the same user interface. An additional loop adjustment module was an important feature for Wiechmann when equipping the systems. If the sanding pattern changes due to the running time, the machine automatically adjusts itself. This way, the quality can be reliably set once. This also means that customers can order the sanding quality or the sanding pattern individually.
The Right All-Round Package
Investing in new technology has paid off for Wiechmann: The grinding processes run much more efficiently and larger parts can be machined. With rounded parts, the paint also holds better, foils on the sheet metal do not have to be removed and engravings are easier to see. Another very important point: The new machines require significantly less electricity.
Many of Wiechmann's customers appreciate the machine edge rounding and gladly accept the service. And the new plant technology has opened up yet another business field. "We have customers who produce sheet metal parts themselves and bring them to us for edge rounding," says Wiechmann.
And one point is particularly important for the managing director of the Ammerland-based company: working at eye level. "There are no complicated and lengthy processes when working with Lissmac. We don't have to pull a ticket when we need a quick answer to our question in everyday business. We can always rely on the good service and the good mechanical engineering. One thing is certain: We are simply taken seriously as a customer."