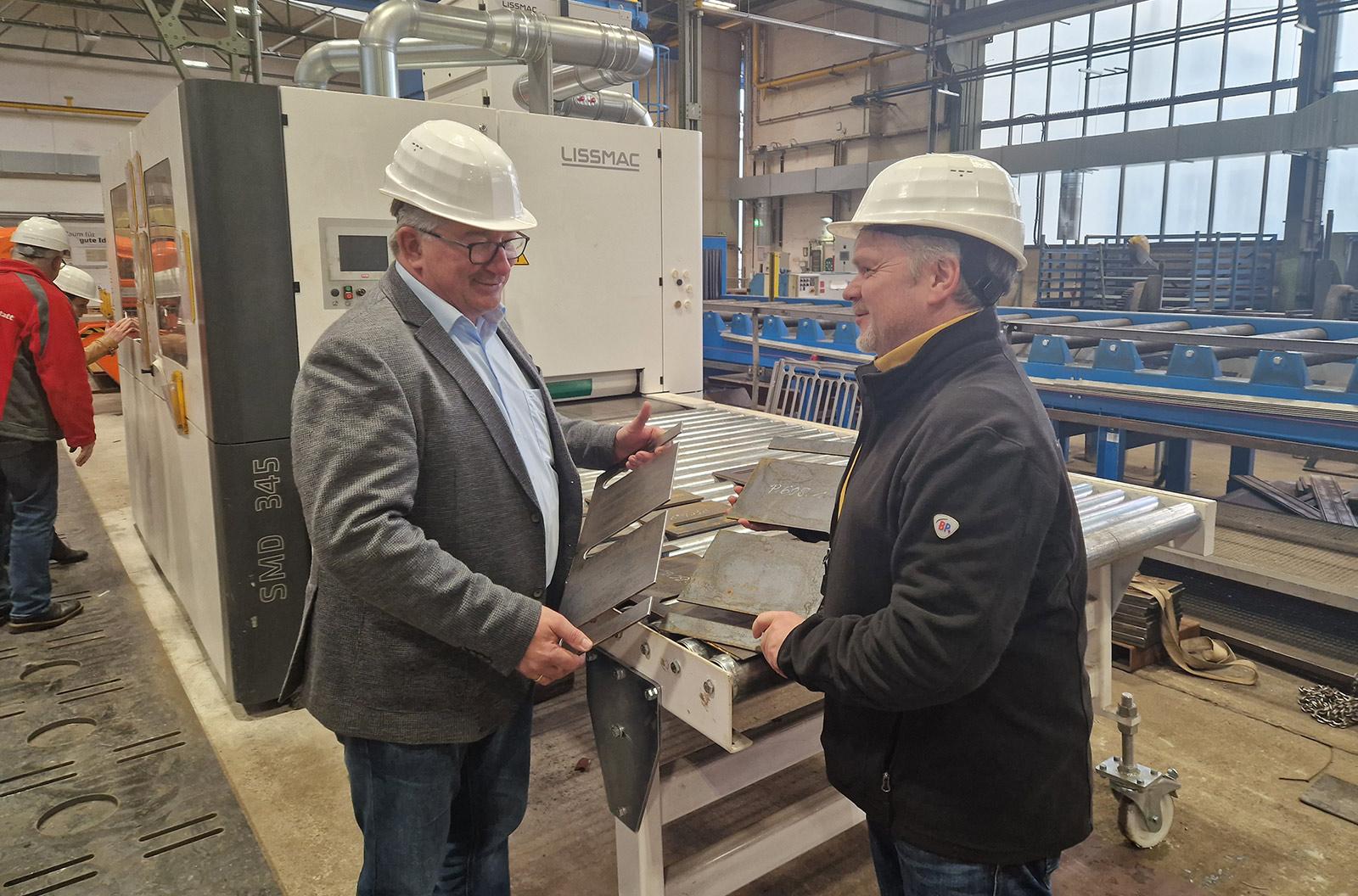
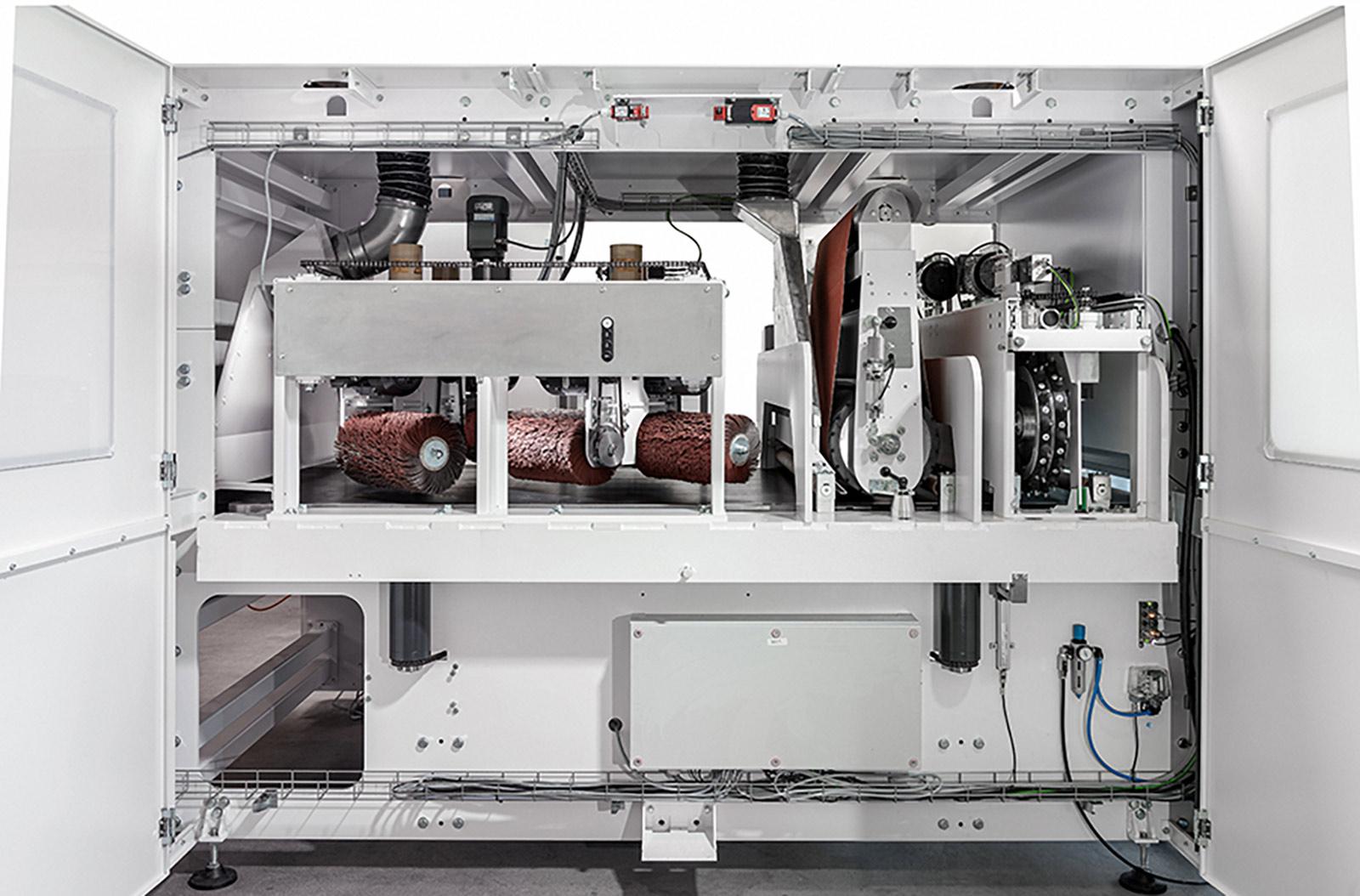
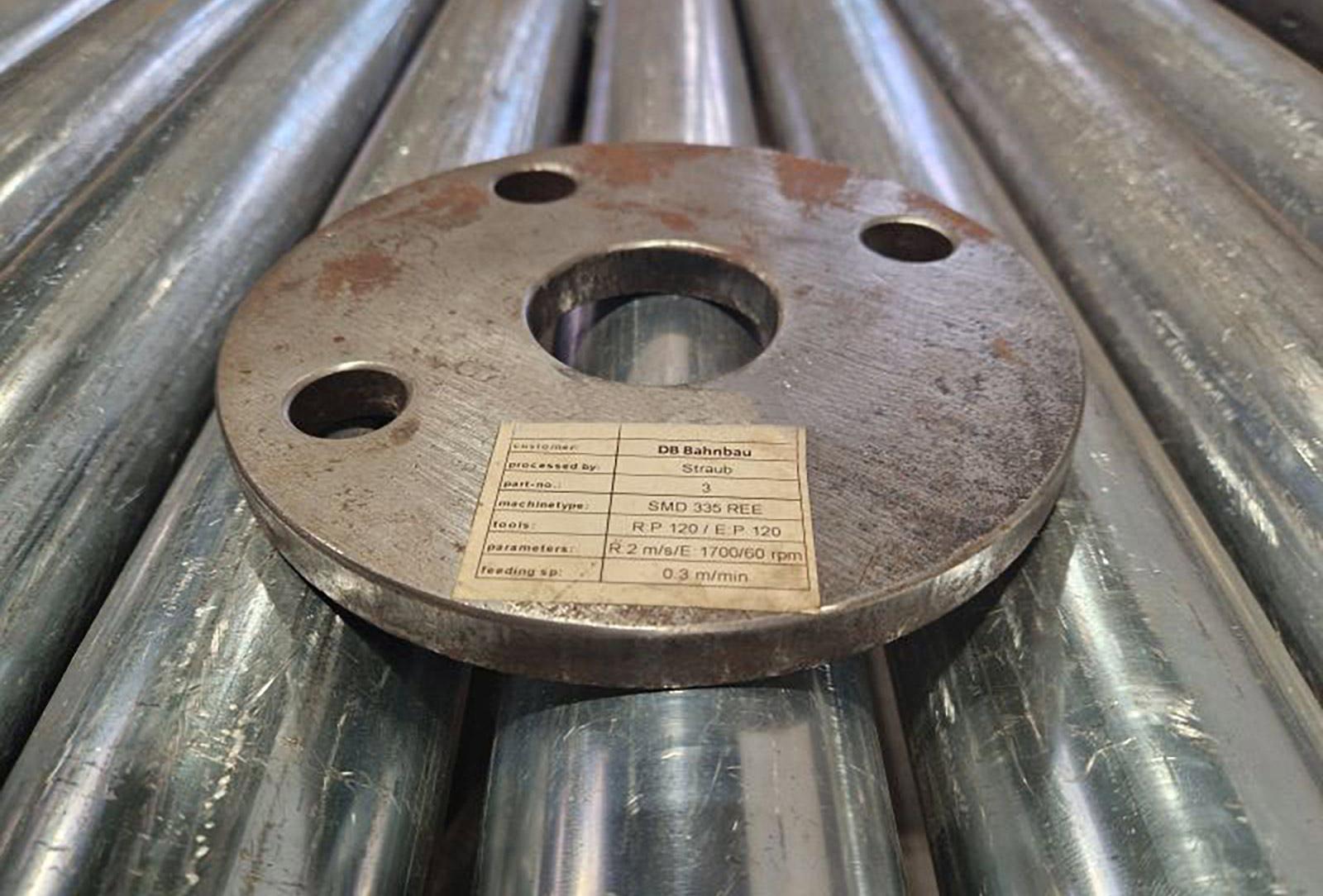
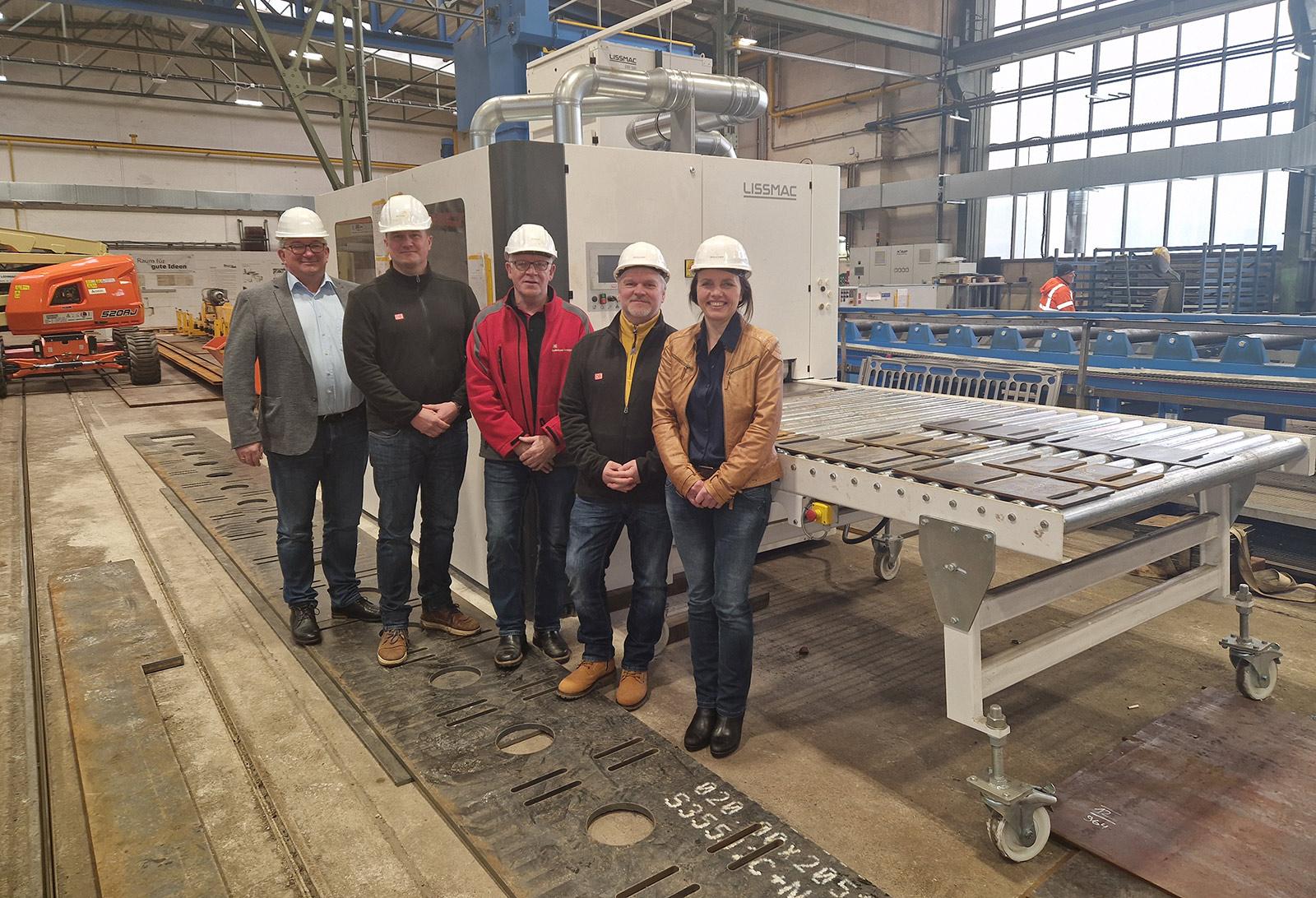
New Grinding And Deburring Machine For The Deutsche Bahn Bridge Workshop
September 20, 2021
The DB Bahnbau Group is the full-service provider for railway infrastructure. In the bridge workshop (Brückenwerkstatt) in Dresden, almost everything revolves around steel railway bridges. In order to be able to operate economically and in line with quality standards, the bridge workshop invested in new plant technology.
Text: Annedore Bose-Munde
The Brückenwerkstatt Dresden specialises in the design, manufacture and assembly of steel and bridge construction. The portfolio includes everything from the planning and manufacture to the installation of bridges, steel structures, construction aids and railway embankment culverts.
Against the background of increasing quality requirements, the topics of rounding and edge breaking have become increasingly important in recent years. At a sharp edge, the corrosion protection system breaks down first and. the longevity of the engineering structures must be ensured. Manual editing cannot reliably guarantee reliable and repeatable quality.
Roland Möbius is responsible for cutting and says at the Brückenwerkstatt Dresden: "In 2018, a new DB Netz guideline came out that is based on EN DIN 10/90 -, a European standard that is generally valid for static load-bearing components. The internal standard regulates the preparation and further processing of welded products, e.g. the degree of purity of the sheet metal and how the edges are to be rounded. Here it is required that all edges with radius 2 mm should be rounded."
Reliable edge rounding with radius 2
This was the specific point where action had to be taken. Up to this point, deburring and edge rounding was mainly done manually. A technical solution had to be found. There was also the issue of employee health, as the strenuous and repetitive nature of the work was compounded by the dust generated by grinding. "We knew that we wanted and needed to change something. So we gradually started looking at filleting machines. We clearly defined our requirements for the new machine and looked at what machines were available on the market," says Uwe Träber. He is the workshop manager and thus responsible for the execution of production and the machine processes.
After a great deal of research, the bridge workshop sent samples to a number of equipment suppliers, where the appropriate tests were carried out. And finally, they also consulted a business partner - Mende Industrieprodukte e.K. from Wolkenstein in the Erzgebirge district of Saxony. The company advises on abrasives, deburring and polishing agents, stainless steel and surface technology, aluminium, copper and brass processing, and then supplies the components, -as it did for the bridge workshop in Dresden. Kerstin Kunze, owner of Mende Industrieprodukte, looks after the abrasives here. So she also knew the topic of edge rounding 2 mm, which came up again in 2018. Kunze also works very closely with Lissmac Maschinenbau GmbH in Bad Wurzach and has thus also been able to establish contact with the bridge workshop.
Discussions on the requirements for the parts will take place in 2019 and the first parts will be machined in 2020. How should the processing be done? Should it be machined on both sides or on one side? Is the result of the rounding good? Which of the Lissmac systems can best meet the requirements? Kerstin Kunze and Dirk Schürstedt shed light on all these questions with a view to the sample parts of the bridge workshop. "We then made a recommendation for an SMD 3 P edition. The universal grinding and deburring machine was specially designed for thick sheet metal processing and delivers very high performance in edge rounding up to a 2 mm radius due to maximum tool contact with the components. In addition, the upstream mechanical removal of slag from plasma and oxyfuel cut parts is effective and reduces tooling costs," says Schürstedt. He is Area Sales Manager Metal Processing at Lissmac.
And Schürstedt also mentions a challenge that had to be overcome in the whole decision-making process: "The trials took place as the pandemic peaked. Due to Corona restrictions at the time, personal visits were not possible. We presented, discussed and clarified a lot online. The actual part machining, however, took place on site at Lissmac. The parts were then shipped for that."
Results of the sample edits were evaluated
All sample processing results were evaluated by the in-house quality assurance department. The DB Bahnbau Group, and thus also the Brückenwerkstatt Dresden, ultimately opted for the recommended SMD 3 P edition, i.e. for the machine that best covers the requirements portfolio. The plant was delivered in December 2021 and commissioned in January 2022.
Andreas Naumann has been head of the Brückenwerkstatt Dresden since January 2022 and is responsible for the Brückenwerkstatt as a whole. He is satisfied with the decision to use Lissmac technology. "The overall concept, both technically and commercially, fits. In addition, Lissmac is a reliable partner, also with regard to service," he says.
One thing is certain: What the Lissmac machine does today was previously done manually-, with a lot of manpower and material. The aim was to automate processes to make them faster and more economical. In addition, the high cost of personnel was to be reduced and the quality to be mapped was to be comprehensible. All this has been achieved.
Roland Möbius, in whose area of responsibility the machine is located, says: "Our employees confirm that the use of the new grinding and deburring machine makes their work much easier: in terms of dirt, in terms of reduced noise and also in terms of processes that now run more efficiently". Andreas Naumann underlines this: "It's faster, the quality is very good and comprehensible. In addition, preliminary processes such as edge rounding have always been a bottleneck for us. So the increased output also helps us to organise the whole process better. To further optimise the process, a student trainee is currently investigating the individual system and process parameters.
Traditional Company Is Well Positioned
Questions in the start-up phase could be clarified quickly. "The sheets that are processed vary in terms of height or curvature, for example. Here it is important that we have gained experience and were able to get information from Dirk Schürstedt and Kerstin Kunze," says Uwe Träber.
It is mainly steel parts that are machined in a wide range of dimensions, starting with parts of approximately 100 mm x 100 mm up to dimensions in the range of 2 to 3 metres. These are both individual parts and small to medium quantities. "Our utilisation rate is very good. Our employees are satisfied. The spectrum on which we work is dependent on the task at hand. We act in a completely flexible and variable way. These are almost always individual parts. Their shape and dimensions are unique. Whether web parts for girders or bulkheads- from the door handle to the entire bridge, we can process everything," Naumann gives an overview.
DB Bahnbau Gruppe GmbH, to which the Dresden Bridge Workshop belongs, is a subsidiary of Deutsche Bahn - the Dresden site is a department of the Special Construction Division. The DB Bahnbau Group employs around 3,600 people in Germany; there are more than 100 in the Dresden bridge workshop.