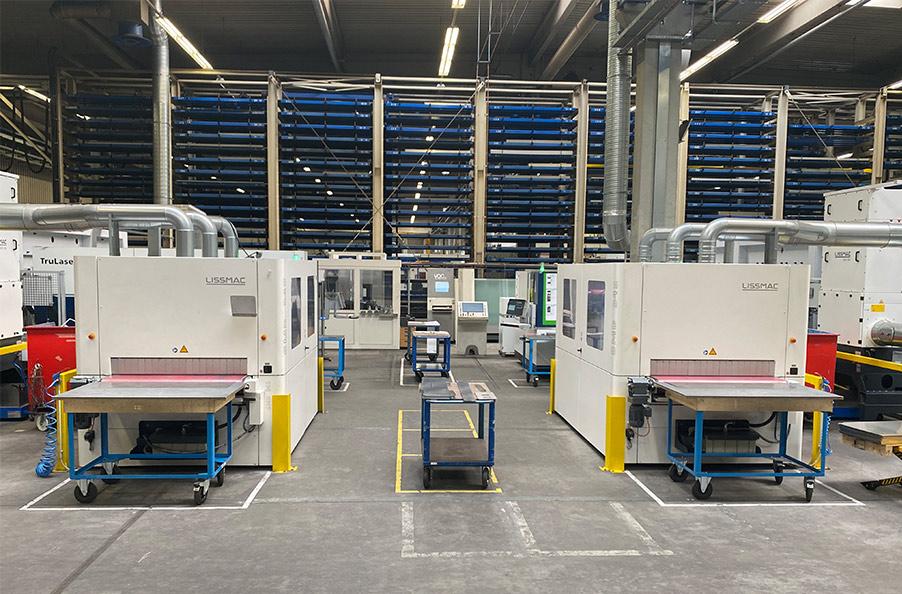
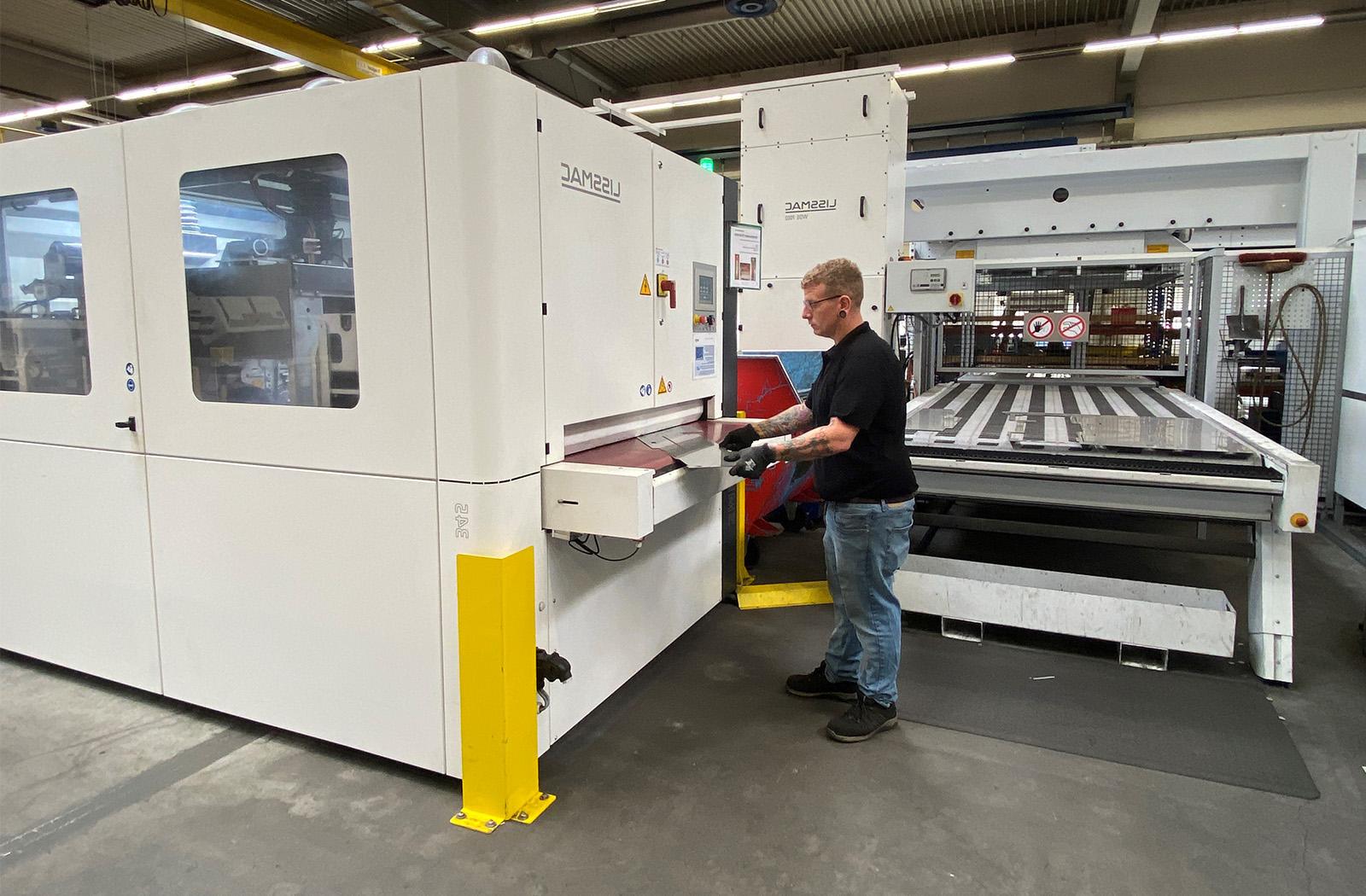
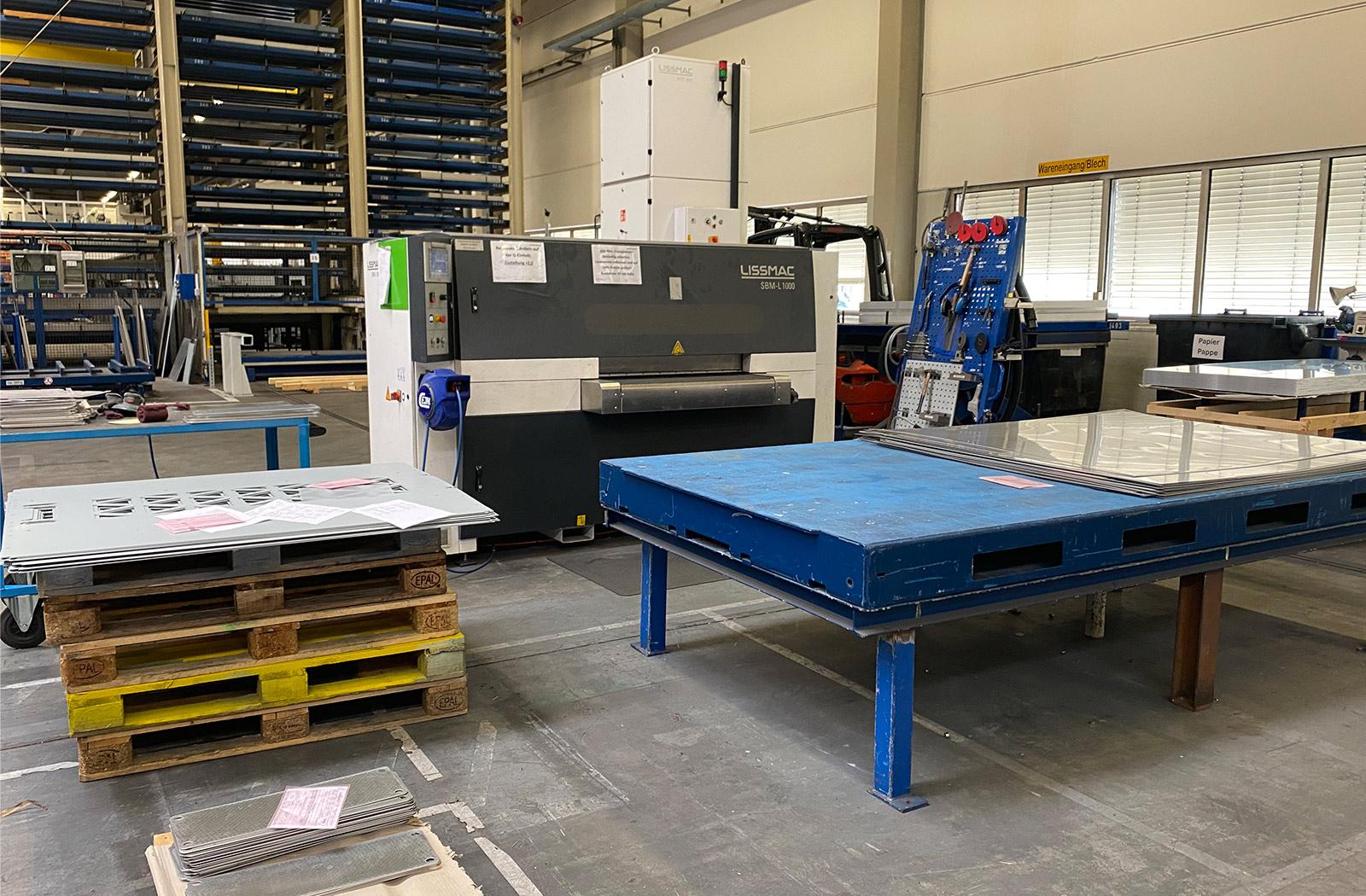
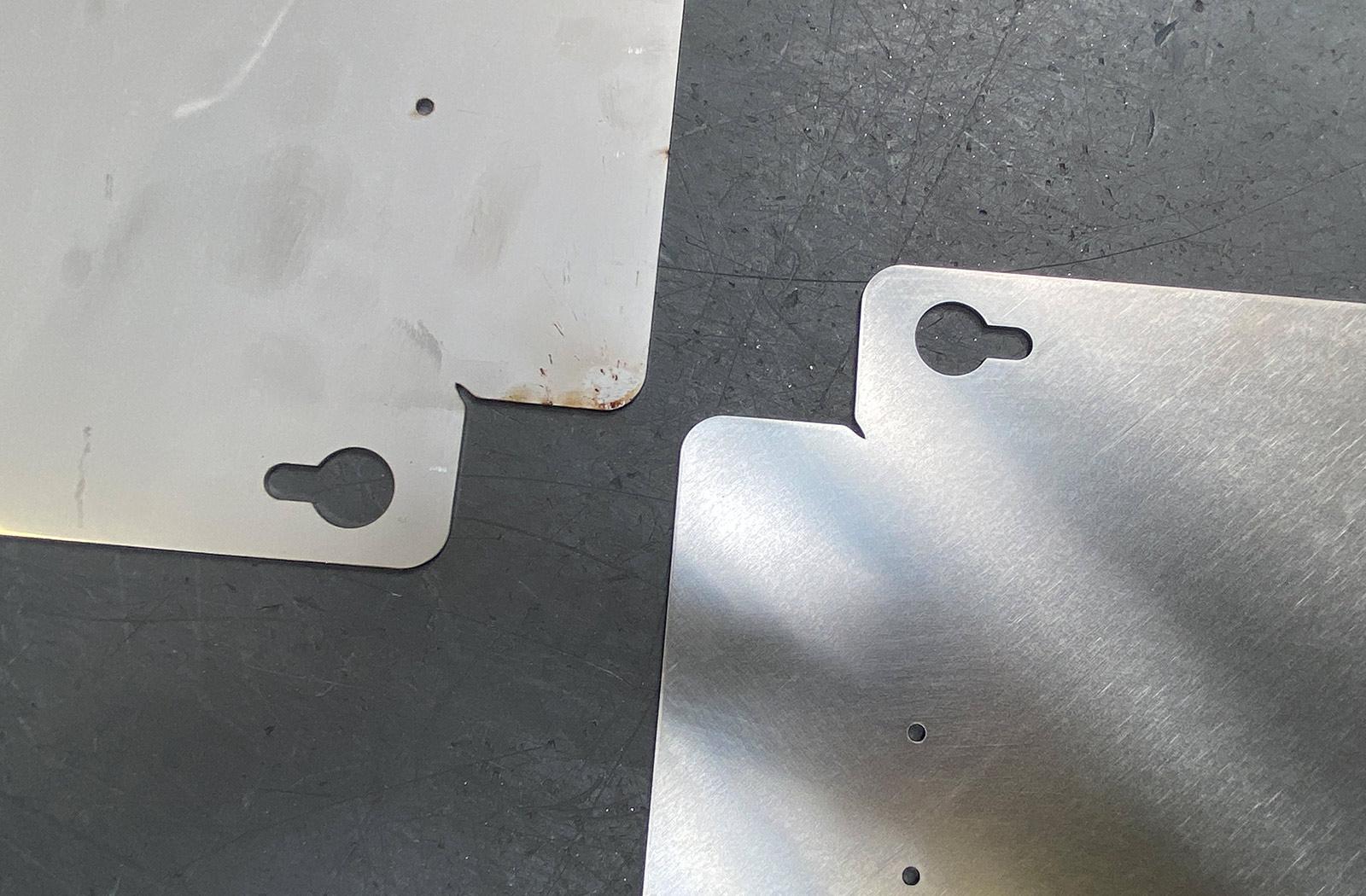
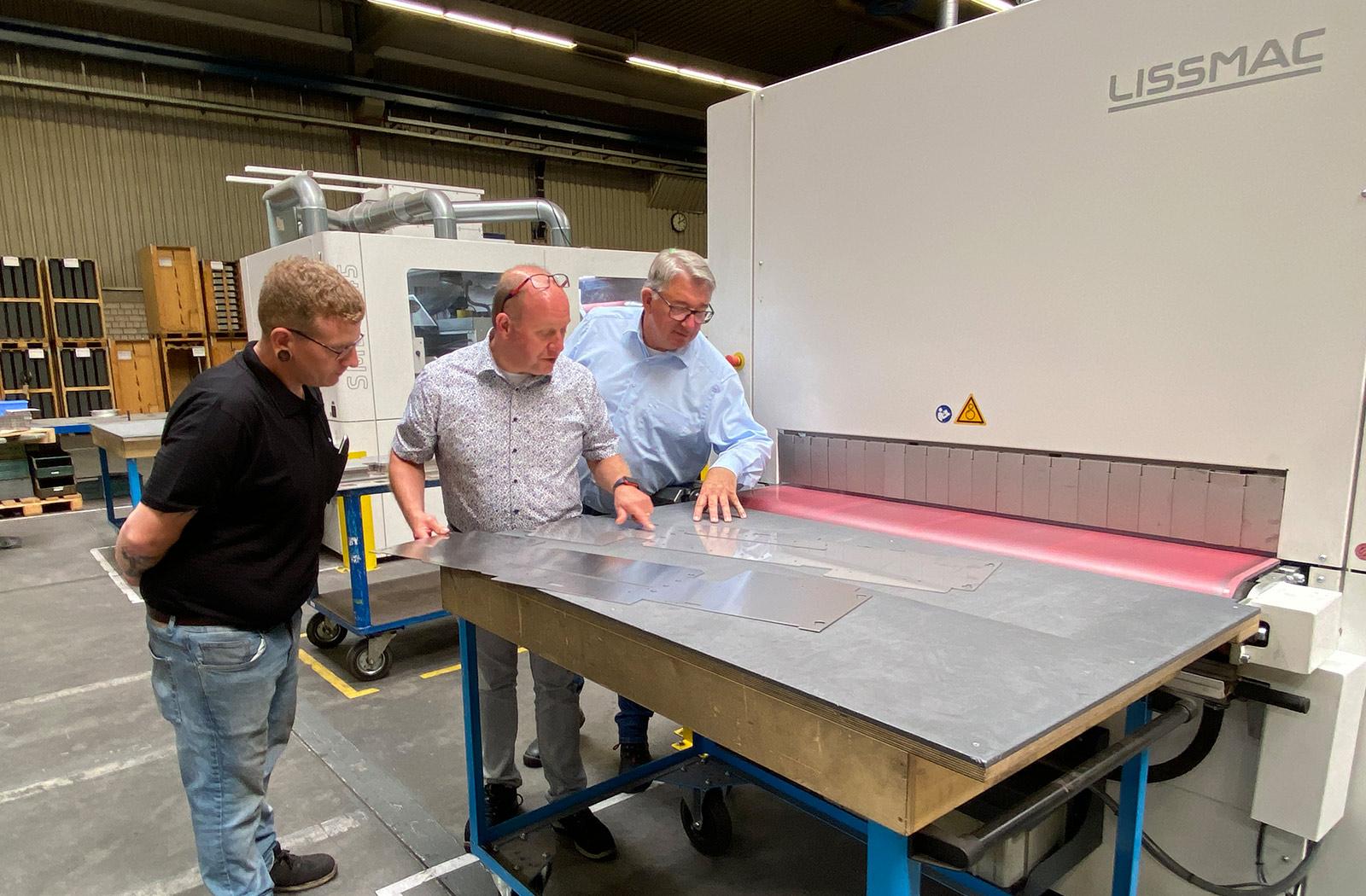
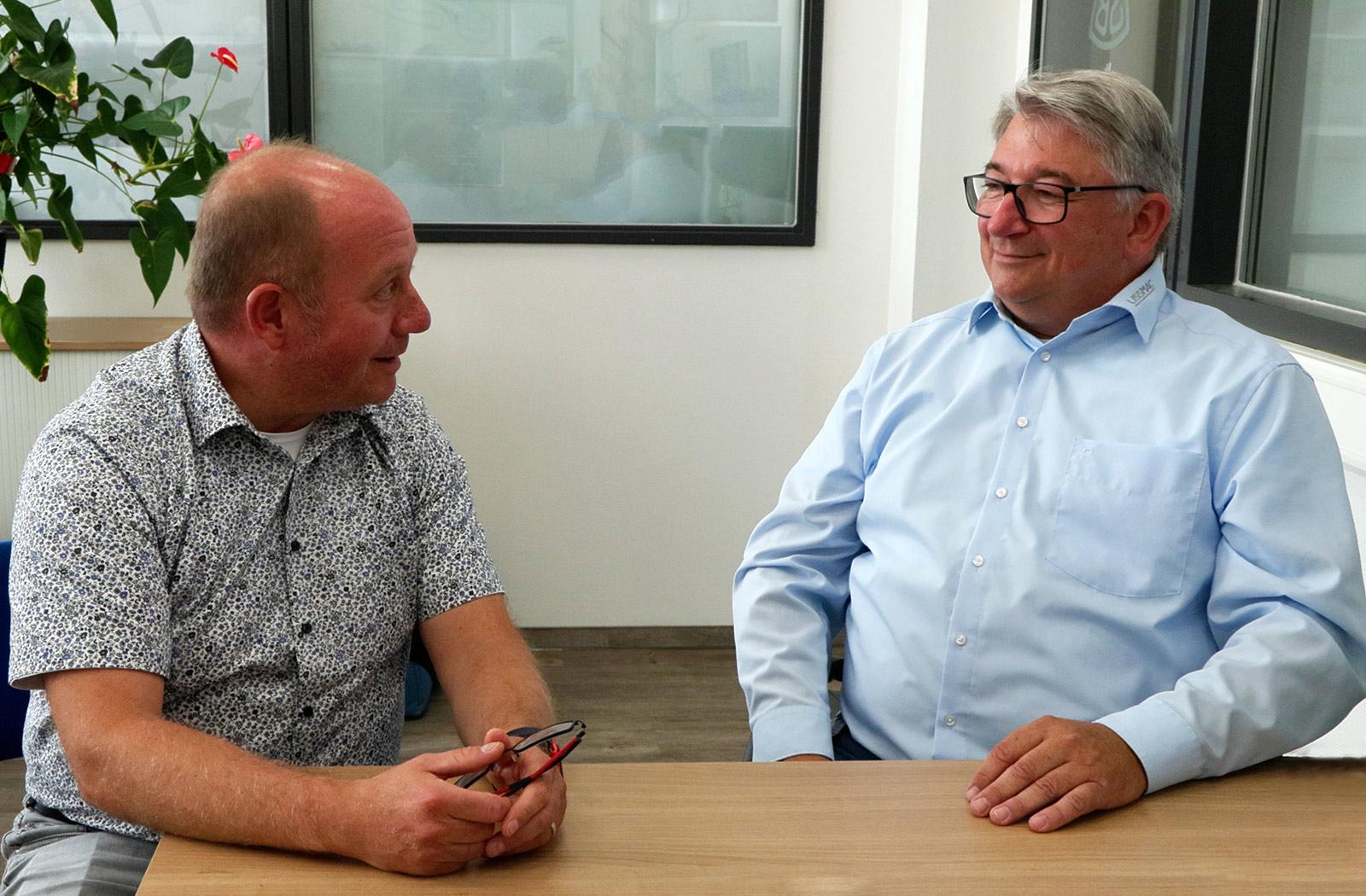
Burr-free sheet metal parts for pay stations and signaling technology components
Noviembre 25, 2024
Burr-free sheet metal parts for pay stations and signaling technology components
Fiber lasers in particular require a powerful downstream deburring technique due to the burrs that occur during cutting. A global company from North Rhine-Westphalia has invested in this technology multiple times and, in doing so, has developed optimized production logistics and a continuous material flow.
Text: Annedore Bose-Munde
The production know-how that goes into the things we encounter every day is often not apparent at first glance, for example in parking or signaling solutions. The family-owned company Scheidt & Bachmann, based in North Rhine-Westphalia, manufactures pay stations and terminals worldwide, for example for parking garages or buses, as well as signaling technology components and barrier systems, for example for Deutsche Bahn. Founded in 1872, the company has grown from a machine manufacturer to a global system provider with a total of around 3,500 employees worldwide. Scheidt & Bachmann's prefabrication is based in Mönchengladbach, with assembly lines in Slovakia and the USA. 90 percent of Scheidt & Bachmann's production is stainless steel parts, as well as some aluminum and steel parts.
In the sheet metal processing area in Mönchengladbach, 90 employees manufacture a broad portfolio of sheet metal products. The demands on the processing results and the processing technologies have increased continuously in recent years. Before 2006, laser cuts were placed on pallets after cutting, stacked and then removed individually. These were then sanded manually and with simple technology. This was quite laborious and required a great deal of manual effort and sometimes multiple passes. Throughput times, logistics and costs were less than ideal.
The first Lissmac system was purchased in 2006 to address the issue of edge rounding: an SBM S 1000 for processing sheet metal and laser parts. Since then, rounding the inside and outside contours on both sides in a single operation has significantly increased process efficiency and saved time. What was still missing at that time was structured, customized production logistics.
Fiber laser was supplemented with powerful deburring technology
When the next step of modernization and investment in new plant technology was to be taken in 2019, several criteria were on the agenda: By purchasing a laser from the company Trumpf with fiber technology, the decision-makers at Scheidt & Bachmann relied on the technological advantages of the process. The purchase of the new cutting technology therefore also directly required modern and powerful deburring technology. And with a view to protecting employees, ergonomic improvements for the workers were also to be achieved.
So, before purchasing the new system, two system manufacturers were contacted and reference parts were sent for sample processing. In the end, the decision was made in favor of an SBML 1500 from Lissmac, which is used for deburring and edge rounding on both sides.
“This system performs double-sided processing in a single grinding pass. And the quality is so good that a single pass is actually enough to achieve a high-quality grinding result,” says Jörg Würker, Head of Mechanical Production and Head of Sheet Metal Processing at Scheidt & Bachmann GmbH. Time-consuming rework is no longer necessary. And he mentions another important aspect: occupational safety for technicians, which of course applies in the US. “If there is a sharp-edged item on an assembly line, the technician can be injured. And that can quickly lead to a legal problem,” says Würker.
The fact that the technical parameters were also handed over with all the test parts was also very helpful, especially in the start-up phase with the new system. “We definitely benefited from that,” says Würker. Dirk Schürstedt, Area Sales Manager for Metal Processing at Lissmac Maschinenbau GmbH, who has been looking after Scheidt & Bachmann since 2019, also remembers the initial contact and a pragmatic and constructive decision-making process. He adds: “All sample processing at Lissmac is always documented precisely and comprehensively and made available to the customer. This includes which machine was used for the processing, which tool, which speeds, which rotational speeds, and so on.” This enables the customer to achieve good processing results right from the start. Over time and based on production experience, the system is then usually fine-tuned so that it can be better and better aligned with the processes.
The workers initially had to get used to handling the new system technology, so targeted operator training in the user interface was carried out. All in all, Jörg Würker and Dirk Schürstedt agree that the project was implemented quickly and constructively. Today, the system is used to process sheets with thicknesses from 0.8 to 10 mm. The size of the respective sheet metal blanks ranges from the size of a cell phone to the size of a table. In 2023, the system was also retrofitted with a wet extraction system to enable aluminum to be processed and to ensure material separation.
Creation of optimized production logistics
When the SBM L 1500 was purchased in 2019, it became clear that the production logistics needed to be optimized. When two fully automated Trumpf fiber laser cutting machines with a connected Stopa storage system were purchased in 2021, the issue came up again and should now be thought through to the end. “When the employee removes the part from the laser system, they should also place it directly on the grinding machine. The continuous material flow was important to us and should be implemented,” says Würker. This was also to avoid manual work and long throughput times. Accordingly, two more systems were purchased in 2022 that could be used to implement this seamless process.
“We rely on stable and functional relationships. That is why we chose Lissmac technology again – this time for two systems with rotary brushing technology that allow us to deburr and also round edges in an adjustable quality and depth,” says the sheet metal processing manager.
“We purchased two SMD 345 S-Edition universal grinding and deburring machines. Both systems work in single-sided operation this time. However, they can be used to create a defined surface finish such as classic brush sanding. This enables greater flexibility and saves purchasing costs,” adds Lissmac specialist Schürstedt. With flexibility in mind, these two systems were also equipped with a wet extraction system.
Technology support is important
One thing is certain: Scheidt & Bachmann is very satisfied with the processing results of the Lissmac systems. “Since the new systems have been in use, we have been reliably achieving excellent deburring results,” says Jörg Würker. In addition, the company receives targeted technology support and reliable service.
For Dirk Schürstedt, it is important to be able to respond to the customer's individual production conditions and requirements with precisely tailored technology. “It's satisfying to be able to support the customer's needs over the years. As the machine manufacturer, we are also constantly developing the systems further. Customer feedback is important for this,” he says. Currently, a major focus is on the operability of the systems. These should be as simple and self-explanatory as possible to use in order to make the operator's work easier.